
Material Requirements Planning (MRP)
Table of Contents Expand What Is Material Requirements Planning (MRP)? How Material Requirements Planning (MRP) Works Steps of Material Requirements Planning (MRP) Material Requirements Planning (MRP) in Manufacturing Types of Data Considered by Material Requirements Planning (MRP) Advantages and Disadvantages of Material Requirements Planning (MRP) MRP Systems: Background Material requirements planning (MRP) is a computer-based inventory management system designed to improve productivity for businesses. There are several advantages to the MRP process: Assurance that materials and components will be available when needed Minimized inventory levels and costs associated Optimized inventory management Reduced customer lead times Increased manufacturing efficiency Increased labor productivity Increased overall customer satisfaction Of course, there are also disadvantages to the MRP process: Heavy reliance on input data accuracy (garbage in, garbage out) MRP systems can often be difficult and expensive to implement Lack of flexibility when it comes to the production schedule Introduces the temptation to hold more inventory than needed As data analysis and technology became more sophisticated, more comprehensive systems were developed to integrate MRP with other aspects of the manufacturing process. Material requirements planning (MRP) is a system that helps manufacturers plan, schedule, and manage their inventory during the manufacturing process. Advantages of the MRP process include the assurance that materials and components will be available when needed, minimized inventory levels, reduced customer lead times, optimized inventory management, and improved overall customer satisfaction.
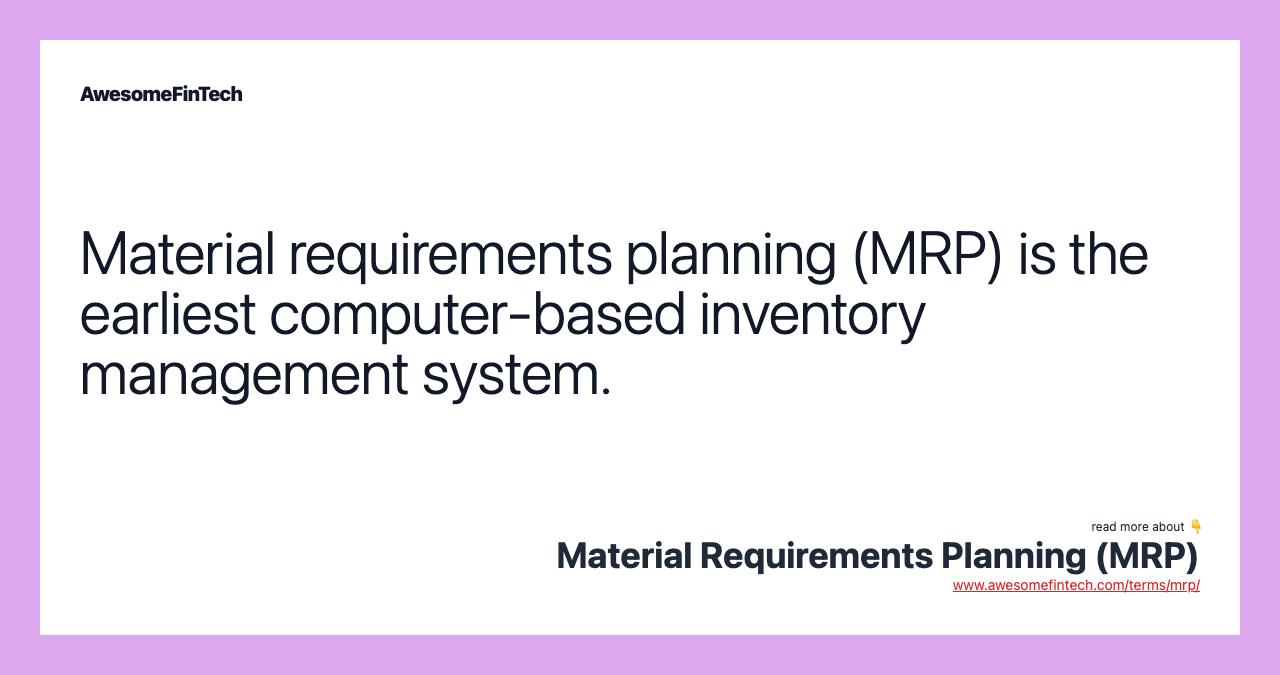
What Is Material Requirements Planning (MRP)?
Material requirements planning (MRP) is a computer-based inventory management system designed to improve productivity for businesses.
Companies use material requirements-planning systems to estimate quantities of raw materials and schedule their deliveries.
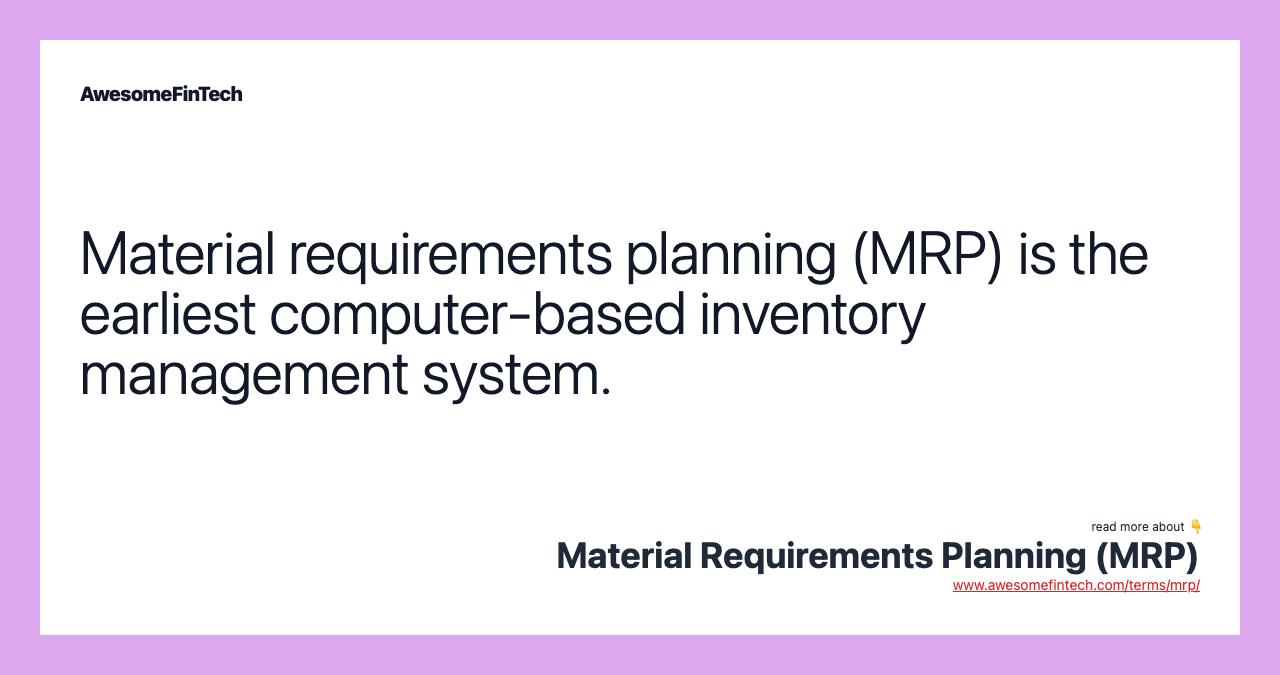
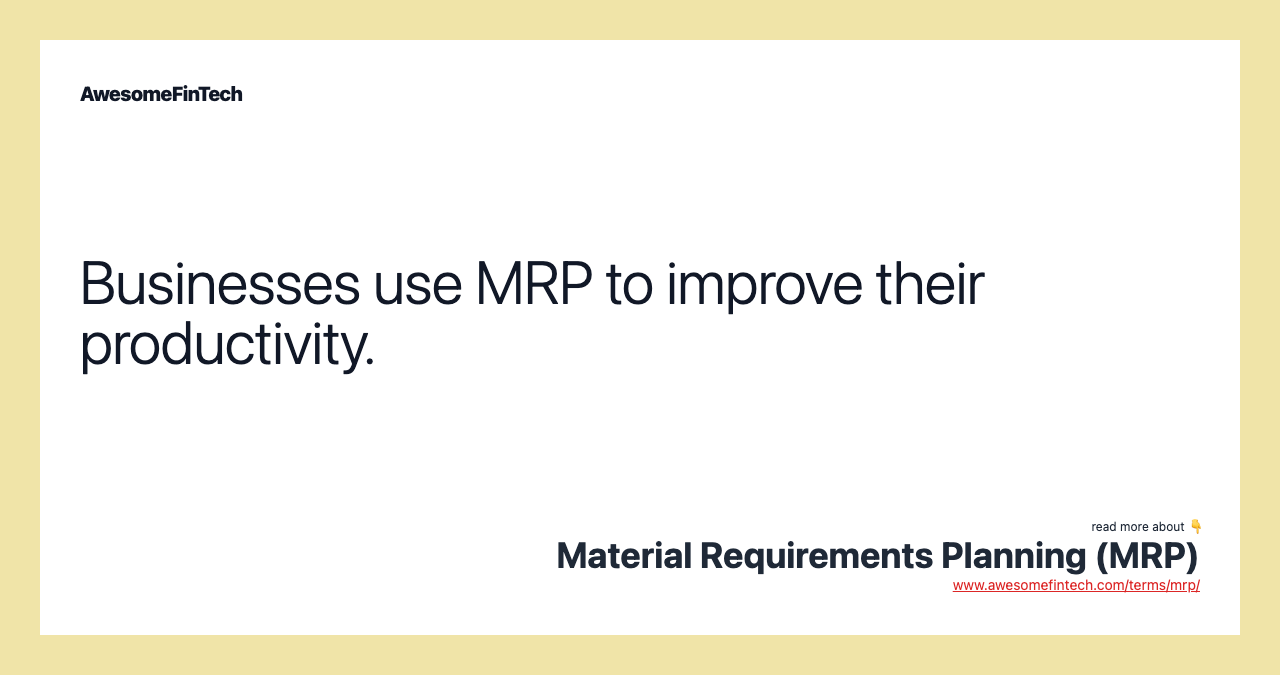
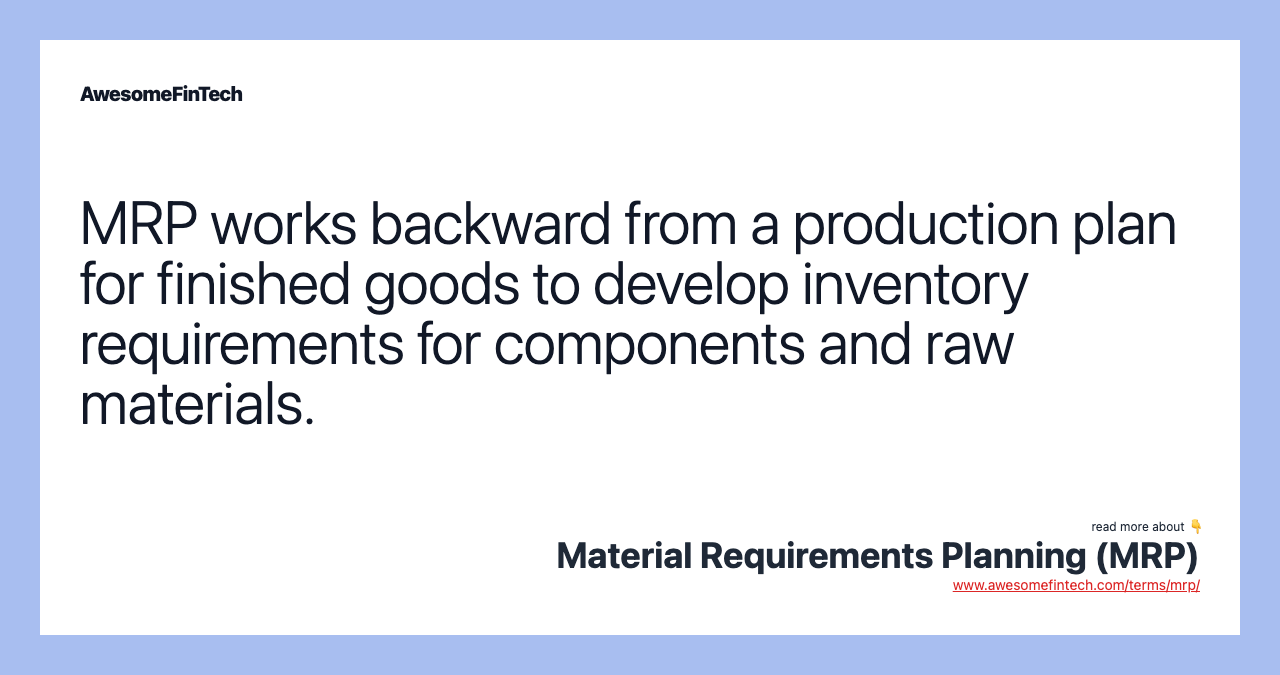
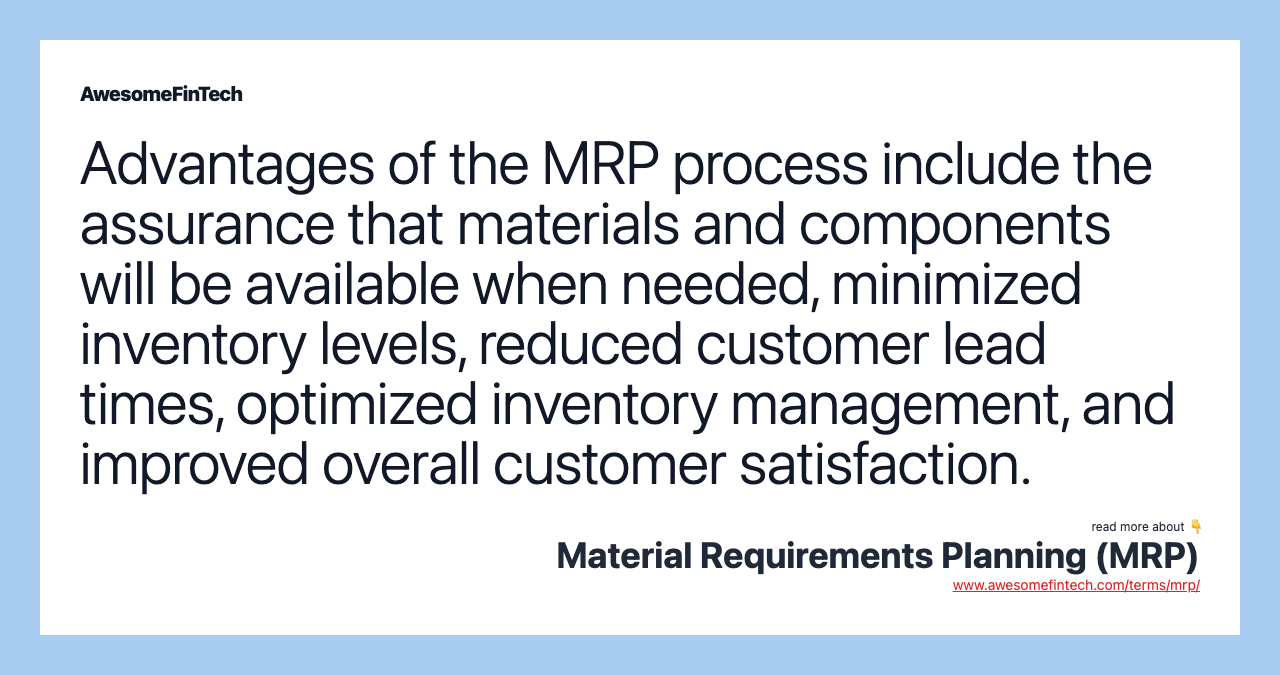
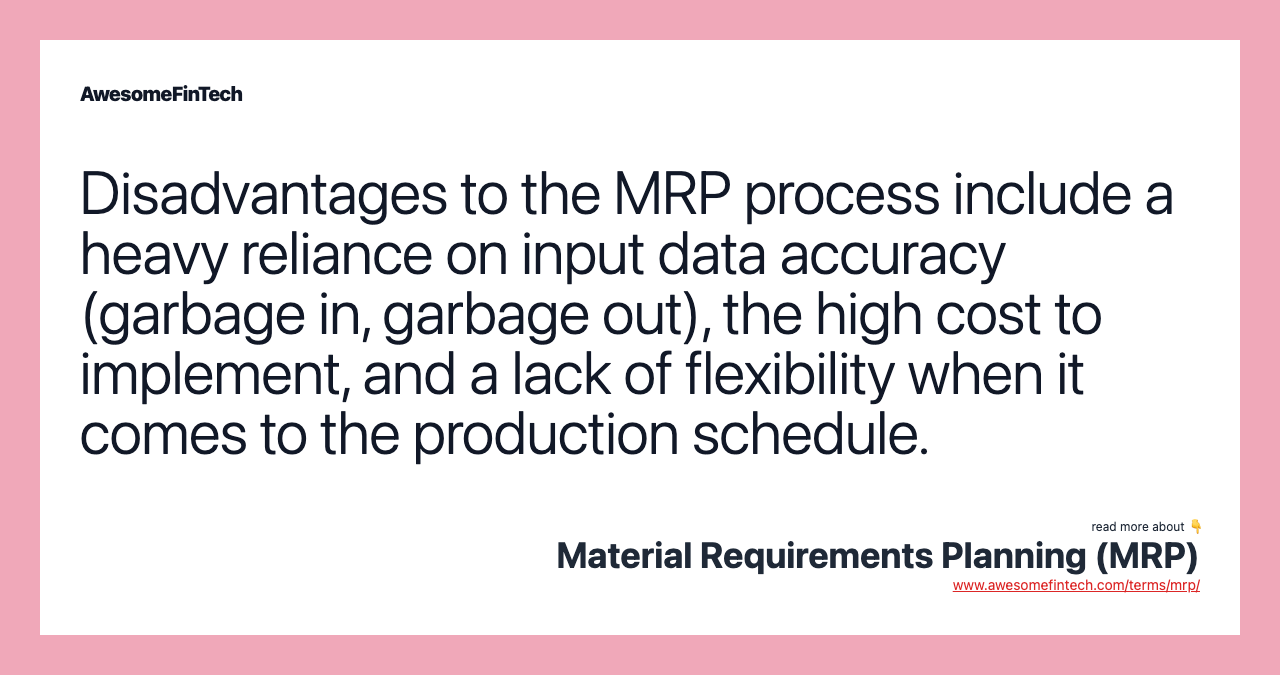
How Material Requirements Planning (MRP) Works
MRP is designed to answer three questions:
- What is needed?
- How much is needed?
- When is it needed?
MRP works backward from a production plan for finished goods, which is converted into a list of requirements for the subassemblies, component parts, and raw materials needed to produce the final product within the established schedule.
In other words, it's basically a system for trying to figure out the materials and items needed to manufacture a given product. MRP helps manufacturers get a grasp of inventory requirements while balancing both supply and demand.
By parsing raw data — like bills of lading and shelf life of stored materials — this technology provides meaningful information to managers about their need for labor and supplies, which can help companies improve their production efficiency.
Steps of Material Requirements Planning (MRP)
The MRP process can be broken down into four basic steps:
- Estimating demand and the materials required to meet it. The initial step of the MRP process is determining customer demand and the requirements to meet it. Utilizing the bill of materials — which is simply a list of raw materials, assemblies, and components needed to manufacture an end product — MRP breaks down demand into specific raw materials and components.
- Check demand against inventory and allocate resources. This step involves checking demand against what you already have in inventory. The MRP then distributes resources accordingly. In other words, the MRP allocates inventory into the exact areas it is needed.
- Production scheduling. The next step in the process is simply to calculate the amount of time and labor required to complete manufacturing. A deadline is also provided.
- Monitor the process. The final step of the process is simply to monitor it for any issues. The MRP can automatically alert managers for any delays and even suggest contingency plans in order to meet build deadlines.
Material Requirements Planning (MRP) in Manufacturing
A critical input for material requirements planning is a bill of materials (BOM) — an extensive list of raw materials, components, and assemblies required to construct, manufacture or repair a product or service.
BOM specifies the relationship between the end product (independent demand) and the components (dependent demand). Independent demand originates outside the plant or production system, and dependent demand refers to components.
Companies need to manage the types and quantities of materials they purchase strategically; plan which products to manufacture and in what quantities; and ensure that they are able to meet current and future customer demand — all at the lowest possible cost.
MRP helps companies maintain low inventory levels. Making a bad decision in any area of the production cycle will cause the company to lose money. By maintaining appropriate levels of inventory, manufacturers can better align their production with rising and falling demand.
Types of Data Considered by Material Requirements Planning (MRP)
The data that must be considered in an MRP scheme include:
Advantages and Disadvantages of Material Requirements Planning (MRP)
There are several advantages to the MRP process:
Of course, there are also disadvantages to the MRP process:
MRP Systems: Background
Material requirements planning was the earliest of the integrated information technology (IT) systems that aimed to improve productivity for businesses by using computers and software technology.
MRP FAQs
What Is MRP?
Material requirements planning (MRP) is a system that helps manufacturers plan, schedule, and manage their inventory during the manufacturing process. It is primarily a software-based system.
MRP's objective is threefold:
- Make sure raw materials are available for production when required
- Maintain the lowest possible material and component levels
- Plan and schedule manufacturing activities
How Does MRP Benefit a Business?
MRP benefits a business in the following ways:
What Are the Inputs of MRP?
The three basic inputs of an MRP system are the master production schedule (MPS), inventory status file (ISF), and bill of materials (BOM).
The MPS is simply the quantity and timing of all end goods to be produced over a specific time period. MPS is estimated through customer orders and demand forecasts.
The ISF contains important real-time information on a company's inventory. It lets managers know what they have on hand, where that inventory is, and the overall status of the inventory.
The BOM is a detailed list of raw materials, components, and assemblies required to construct, manufacture or repair a product or service.
Related terms:
Assemble-to-Order (ATO)
Assemble-to-order is a production strategy whereby components are assembled according to specific orders, as opposed to assembling an item to fill a stock level. read more
Bill of Materials (BOM)
A bill of materials is an extensive list of raw materials, components, and instructions required to construct, manufacture, or repair a product or service. read more
Closed Loop MRP
Closed Loop MRP (Manufacturing Resource Planning) is a computerized system used for production planning and inventory control. read more
Delivery
The term “delivery” refers to the act of a commodity, currency, security, cash or another instrument that is the subject of a contract. read more
Enterprise Resource Planning (ERP)
Enterprise resource planning (ERP) is used by a company to manage key parts of its business such as accounting, manufacturing, sales, and marketing. read more
Inventory Management
Inventory management is the process of ordering, storing and using a company's inventory: raw materials, components, and finished products. read more
Just in Time (JIT) Inventory
A just-in-time (JIT) inventory system is a management strategy that aligns raw-material orders from suppliers directly with production schedules. read more
Manufacturing Resource Planning (MRP II)
Manufacturing Resource Planning (MRP II) evolved from early Materials Requirement Planning (MRP) systems by including the integration of additional data, such as employee and financial needs. read more
Production Efficiency
Production efficiency describes a maximum capacity level in which an entity can no longer produce more of a good without lowering the production of another. read more
Purchase Order Lead Time
Purchase order lead time is the number of days from when a company orders its production inputs to when those items arrive at the manufacturing plant. read more