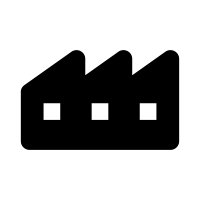
Manufacturing Production
Manufacturing production refers to the methodology of how to most efficiently manufacture and produce goods for sale, beyond just a bill of materials. One limitation of make-to-order (MTO) products is that the production costs tend to be higher than make-to-stock (MTS) products because of the amount of customization required to fulfill the customer's order. The make-to-assemble (MTA) strategy is a hybrid of MTS and MTO in that companies stock basic parts based on demand predictions, but do not assemble them until customers place their order. Whether it is one or the other, manufacturers need to match their production methods to the needs and desires of the market, the available resources, order volume and size, seasonal shifts in demand, overhead costs (such as labor and inventory), and numerous other variables. A company that uses the make-to-assemble (MTA) strategy stocks the basic parts needed for production but does not begin to assemble them until a customer places an order.
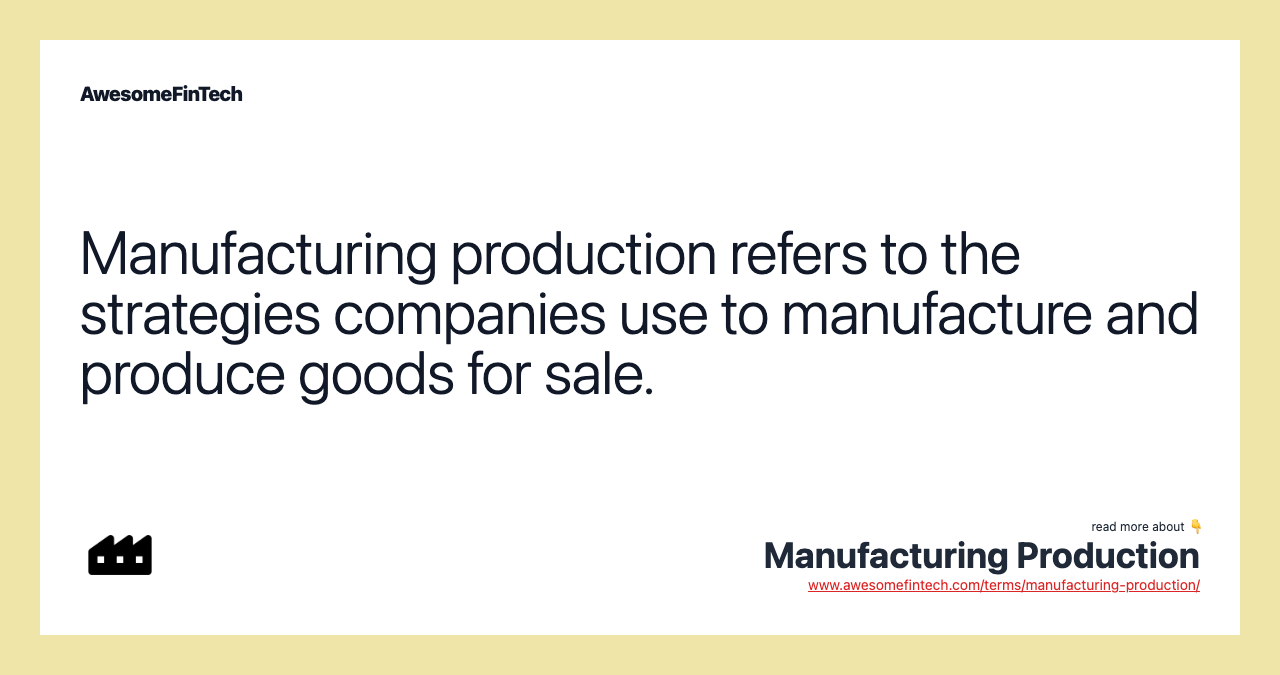
What Is Manufacturing Production?
Manufacturing production refers to the methodology of how to most efficiently manufacture and produce goods for sale, beyond just a bill of materials. Three common types of manufacturing production processes are: make to stock (MTS), make to order (MTO), and make to assemble (MTA). Such strategies have advantages and disadvantages in labor costs, inventory control, overhead, customization, and the speed of production and filling orders.
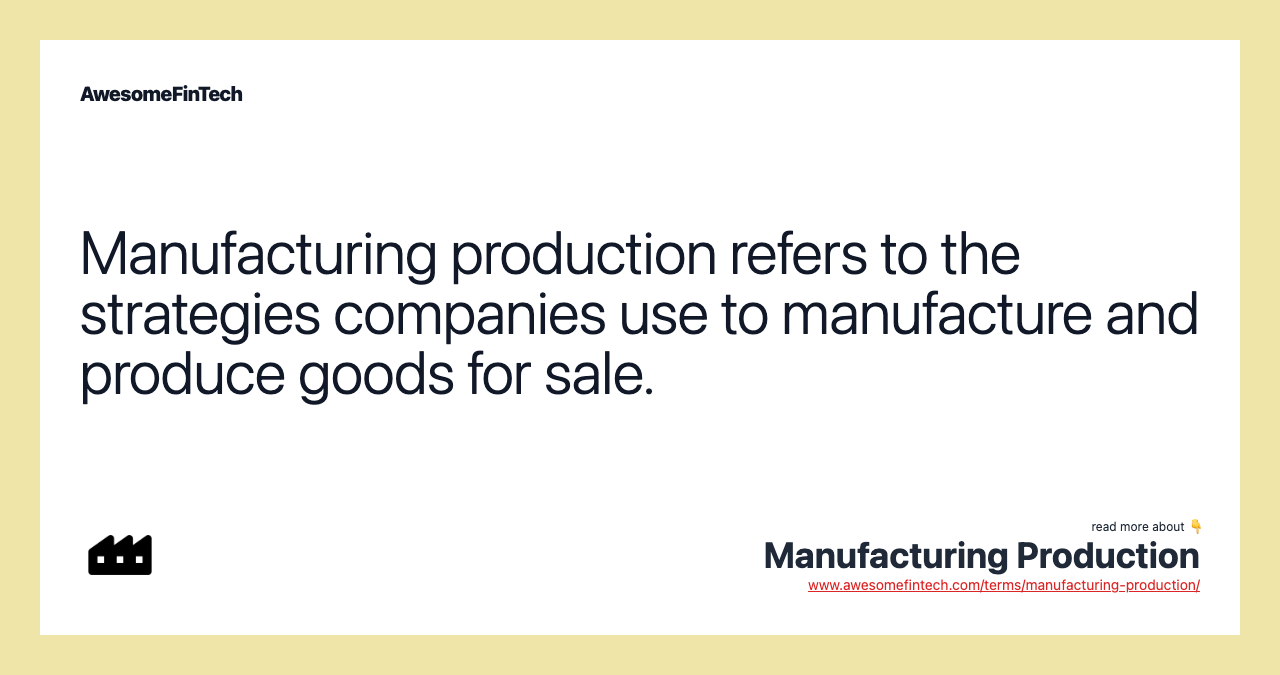
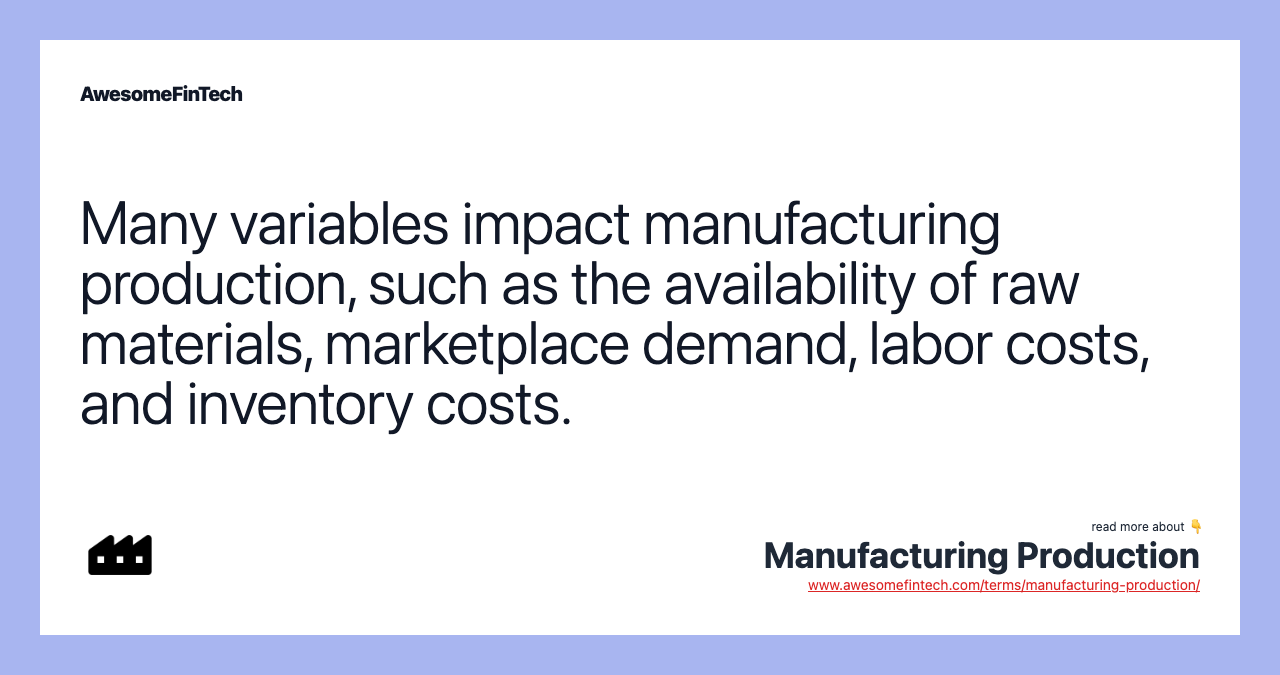
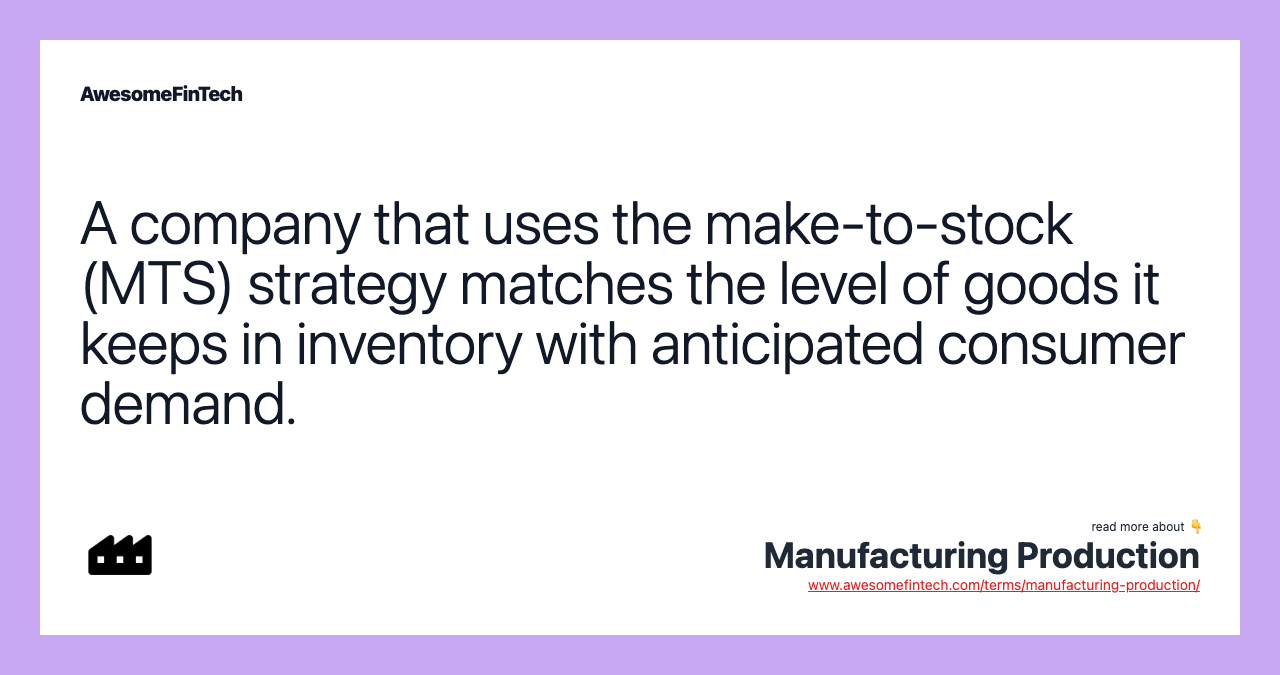
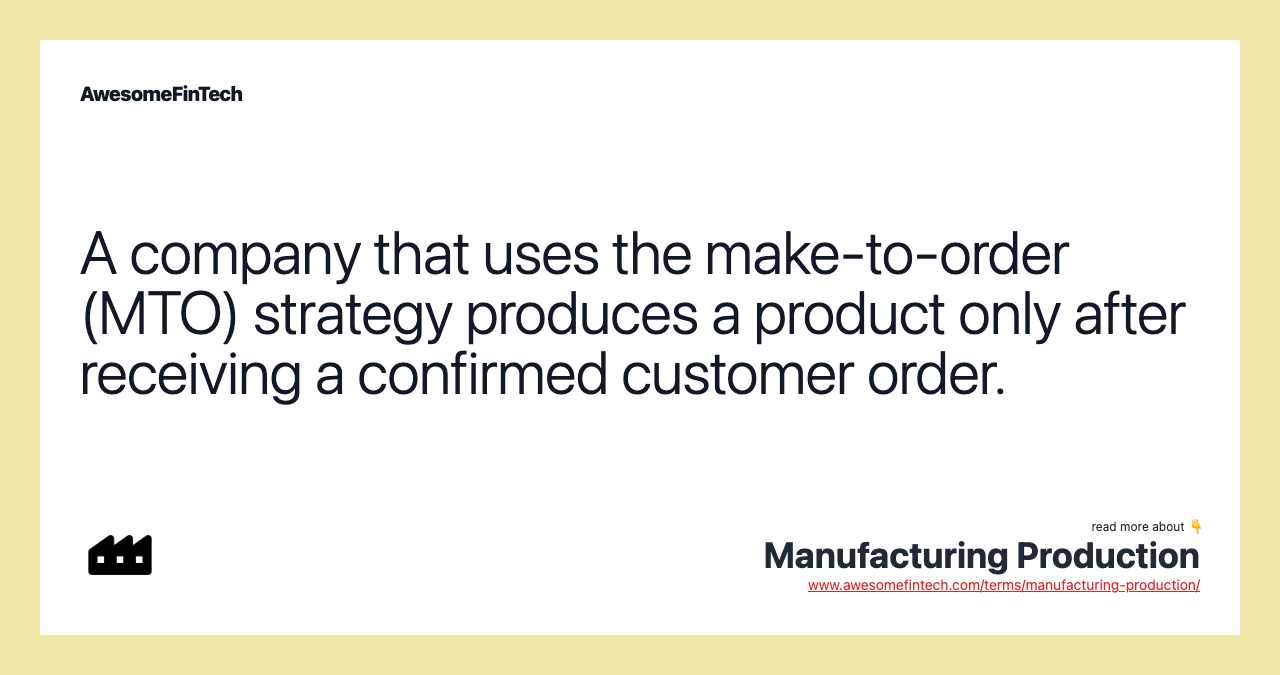
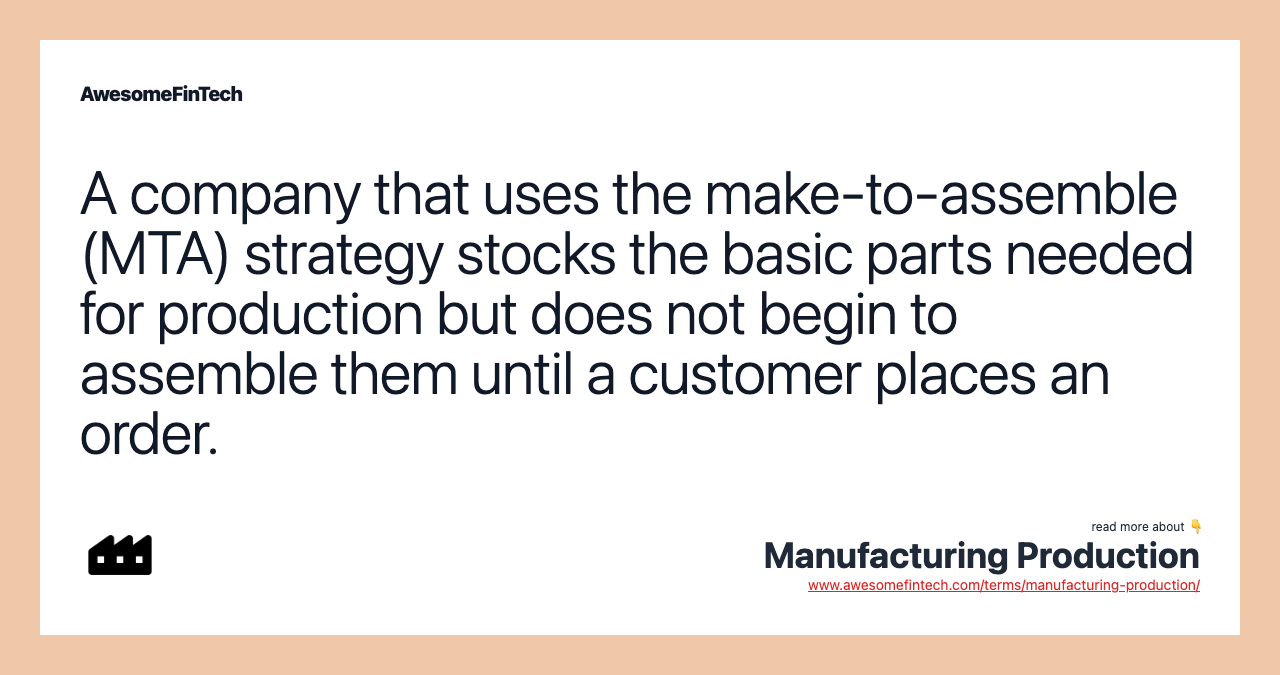
Understanding Manufacturing Production
Manufacturing is the creation and assembly of components and finished products for sale on a large scale. It can utilize a number of methods, including human and machine labor, and biological and chemical processes, to turn raw materials into finished goods by using tools.
Production is similar to manufacturing but broader in scope. It refers to the processes and techniques that are used to convert raw materials or semi-finished goods into finished products or services with or without the use of machinery. Whether it is one or the other, manufacturers need to match their production methods to the needs and desires of the market, the available resources, order volume and size, seasonal shifts in demand, overhead costs (such as labor and inventory), and numerous other variables.
Types of Manufacturing Production
Make to Stock (MTS)
The make-to-stock (MTS) strategy is a traditional production strategy that is based on demand forecasts. It is best utilized when there is a predictable demand for a product, such as for toys and apparel at Christmastime. MTS can be problematic when demand is more difficult to predict, however. When used with a business or product that has an unpredictable business cycle, MTS can lead to too much inventory and a dent in profits, or too little inventory and a missed opportunity.
Make to Order (MTO)
The make-to-order (MTO) strategy (also known as "built to order") allows customers to order products built to their specifications, which is especially useful with heavily customized products. Examples of make-to-order products include computers and computer products, automobiles, heavy equipment, and other big-ticket items. Companies can alleviate inventory problems with MTO, but the customer wait time is usually significantly longer. This demand-based strategy cannot be used with all product types.
One limitation of make-to-order (MTO) products is that the production costs tend to be higher than make-to-stock (MTS) products because of the amount of customization required to fulfill the customer's order.
Make to Assemble
The make-to-assemble (MTA) strategy is a hybrid of MTS and MTO in that companies stock basic parts based on demand predictions, but do not assemble them until customers place their order. The advantage of such a strategy is that it allows fast customization of products based on customer demand. As such, a good example is found in the restaurant industry, which prepares a number of raw materials in advance and then awaits a customer order to start assembly. One downside to MTA is a company may receive too many orders to handle given the labor and components it has on hand.
Special Considerations
The just-in-time (JIT) inventory system is an example of a strategy that focuses on one component of manufacturing production — inventory management. The system benefits companies because it allows them to decrease waste and inventory costs by only receiving goods used in production at the time they are needed.
Companies that employ a JIT inventory system do not store large inventories of parts and raw materials needed to produce their goods. Instead, deliveries of these items arrive at the production facility in smaller quantities as needed to complete production. To make a JIT strategy work, efficient scheduling is of the essence to ensure production is not delayed because of the lack of materials. Electronic inventory systems help managers monitor inventory and respond quickly when production materials get too low.
Related terms:
Assemble-to-Order (ATO)
Assemble-to-order is a production strategy whereby components are assembled according to specific orders, as opposed to assembling an item to fill a stock level. read more
Bill of Materials (BOM)
A bill of materials is an extensive list of raw materials, components, and instructions required to construct, manufacture, or repair a product or service. read more
Business Cycle : How Is It Measured?
The business cycle depicts the increase and decrease in production output of goods and services in an economy. read more
Inventory Management
Inventory management is the process of ordering, storing and using a company's inventory: raw materials, components, and finished products. read more
Inventory :
Inventory is the term for merchandise or raw materials that a company has on hand. read more
Just In Case (JIC)
Just in case (JIC) refers to an inventory strategy where companies keep large inventories on hand in case of a large and sudden increase in demand. read more
Just in Time (JIT) Inventory
A just-in-time (JIT) inventory system is a management strategy that aligns raw-material orders from suppliers directly with production schedules. read more
Make to Order (MTO)
Make to order (MTO) is a business production strategy that typically allows consumers to purchase products that are customized to their specifications. read more
Make To Stock (MTS)
Make to stock (MTS) is a traditional production strategy, used by manufacturers, that attempts to tailor inventory with consumer demand forecasts. read more
Manufacturing
Manufacturing is the processing of raw materials into finished goods using tools and processes. read more