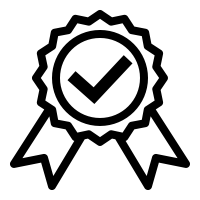
Quality Control & Example
Table of Contents What Is Quality Control? Understanding Quality Control Quality Control Methods The Role of Quality Control Inspectors The Benefits of Quality Control Example of Quality Control Quality Control FAQs In food and drug manufacturing, quality control prevents products that make customers sick, and in manufacturing, quality control can ensure that accidents don't happen when people use a product. Table of Contents What Is Quality Control? Understanding Quality Control Quality Control Methods The Role of Quality Control Inspectors The Benefits of Quality Control Example of Quality Control Quality Control FAQs Having quality control in place within a business can only help ensure product quality and the overall success of a business. In food and drug manufacturing, quality control includes ensuring the product does not make a consumer sick, so the company performs chemical and microbiological testing of samples from the production line.
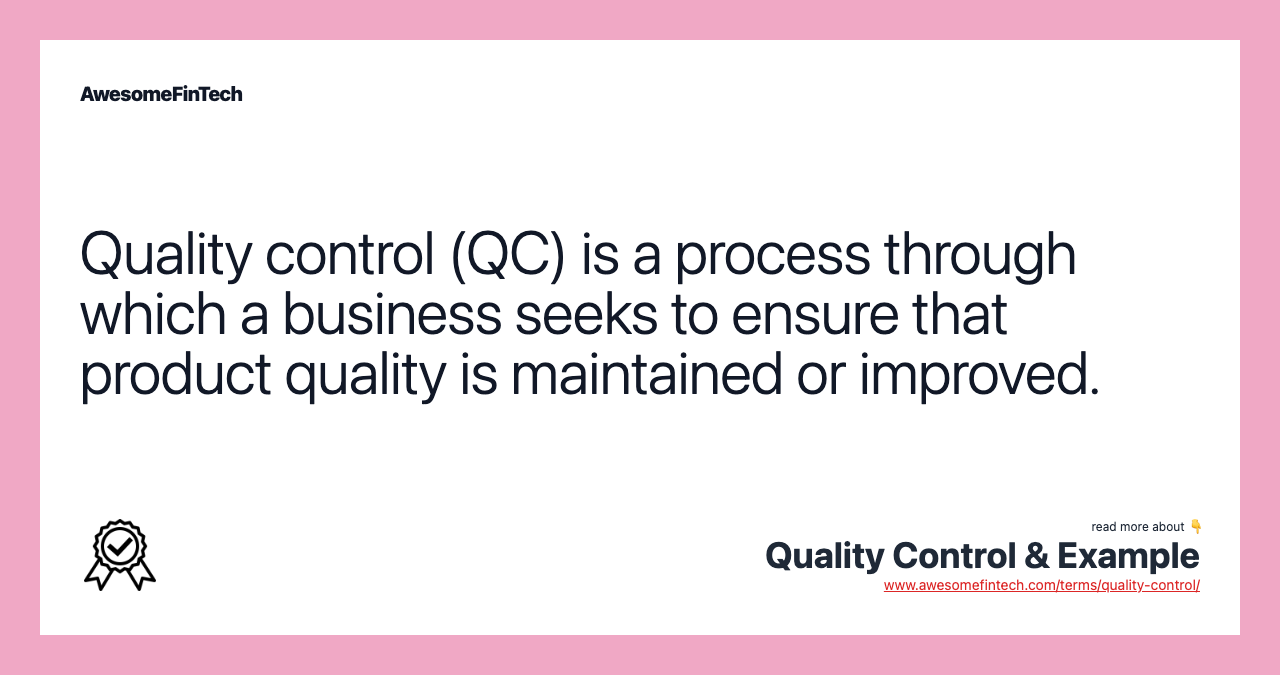
What Is Quality Control?
Quality control (QC) is a process through which a business seeks to ensure that product quality is maintained or improved. Quality control requires the company to create an environment in which both management and employees strive for perfection. This is done by training personnel, creating benchmarks for product quality, and testing products to check for statistically significant variations.
A significant aspect of quality control is the establishment of well-defined controls. These controls help standardize both production and reactions to quality issues. Limiting room for error by specifying which production activities are to be completed by which personnel reduces the chance that employees will be involved in tasks for which they do not have adequate training.
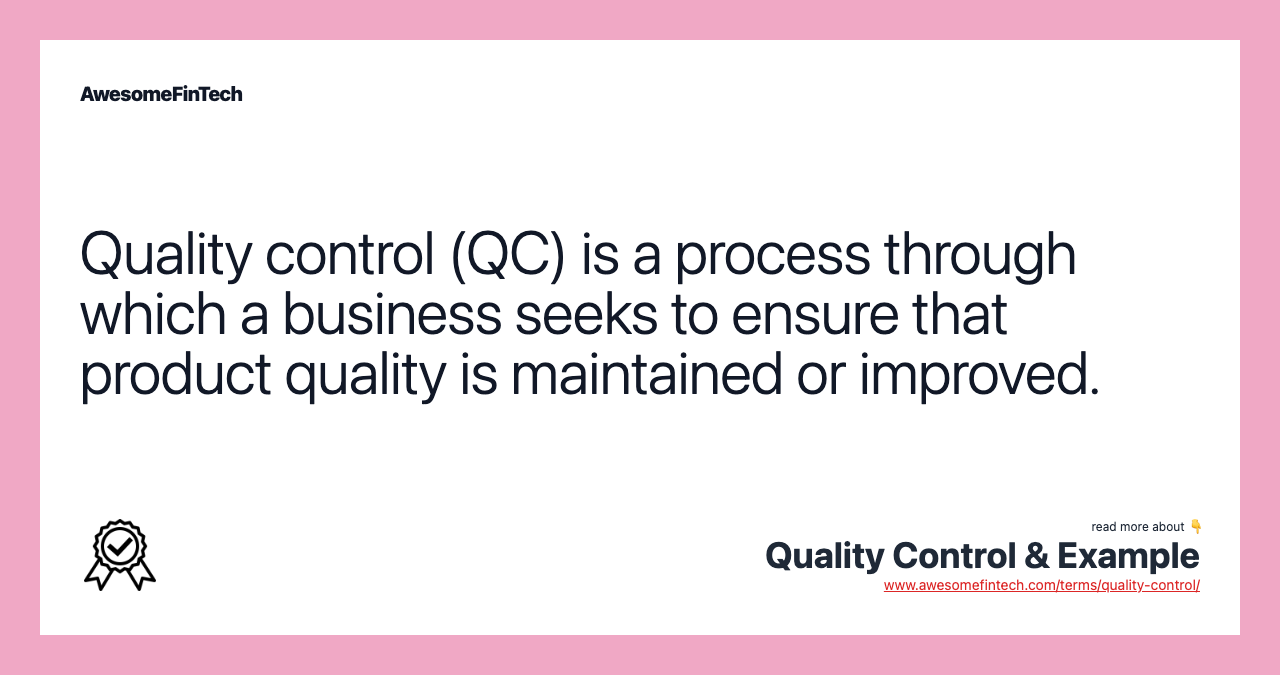
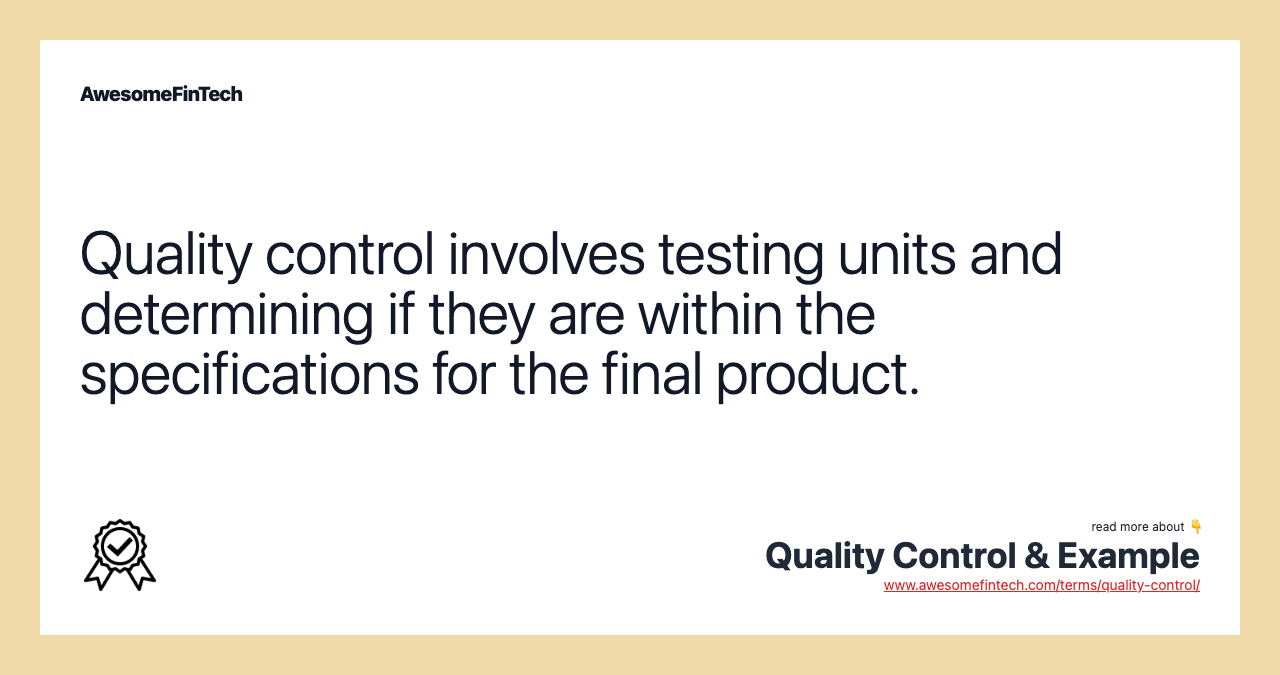
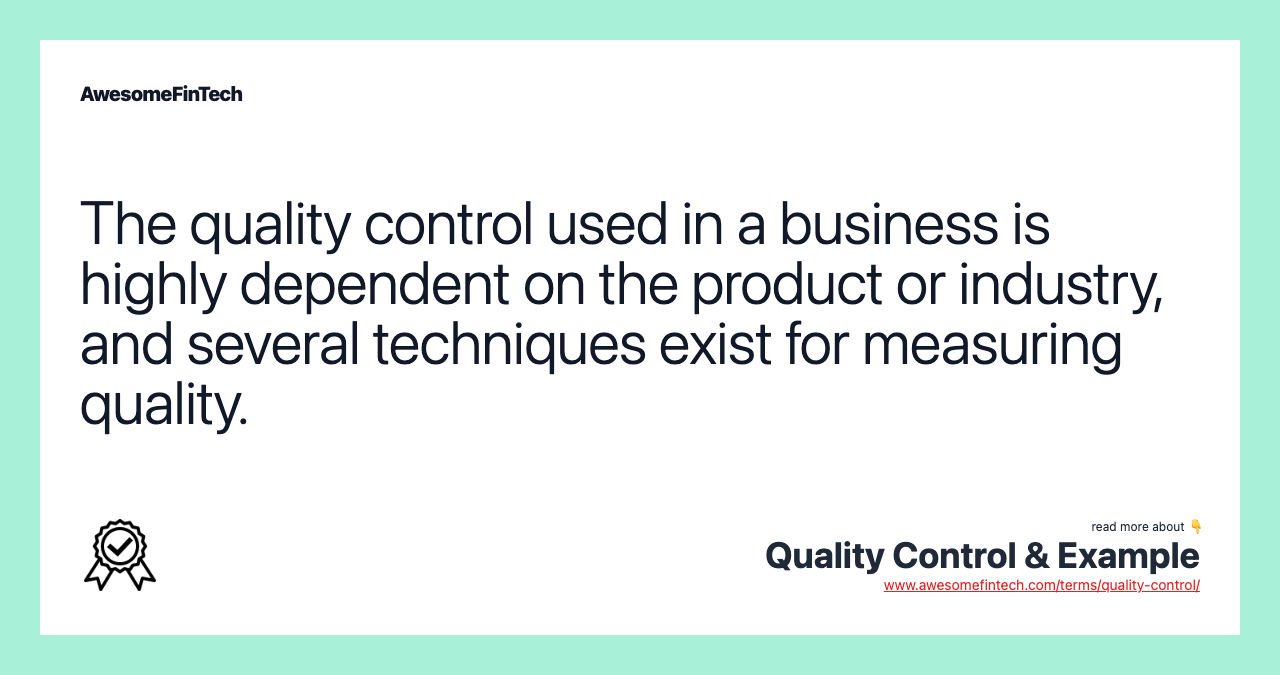
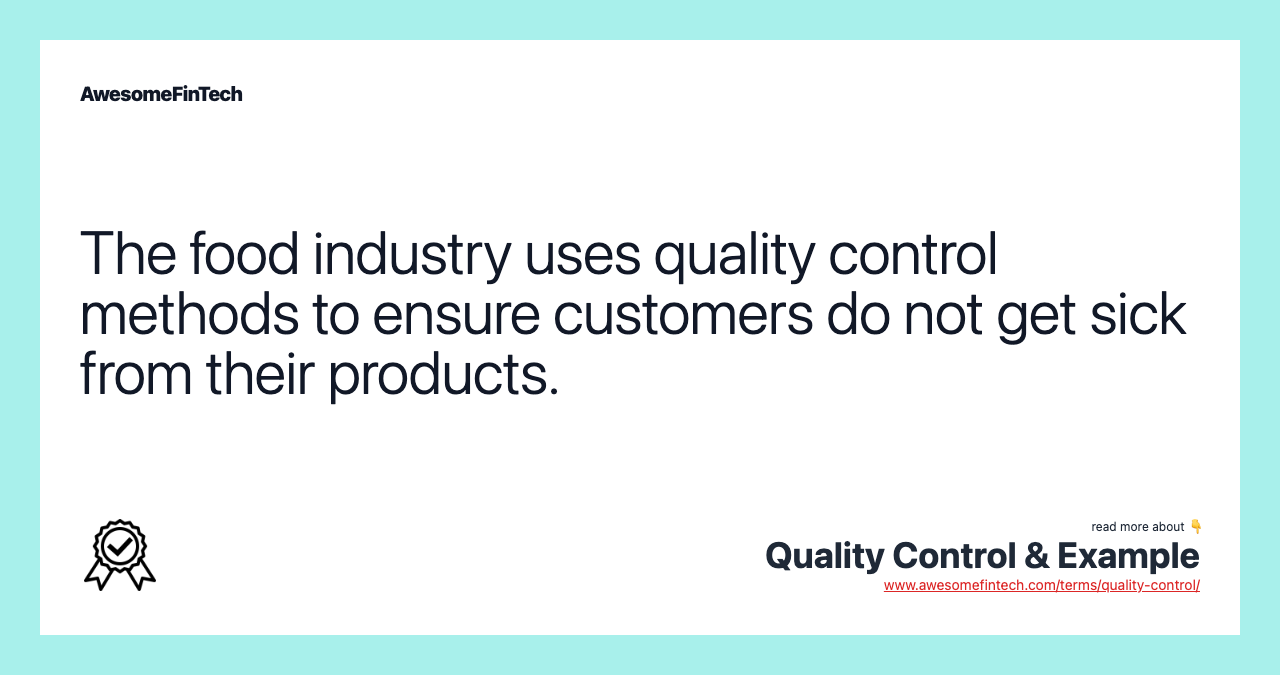
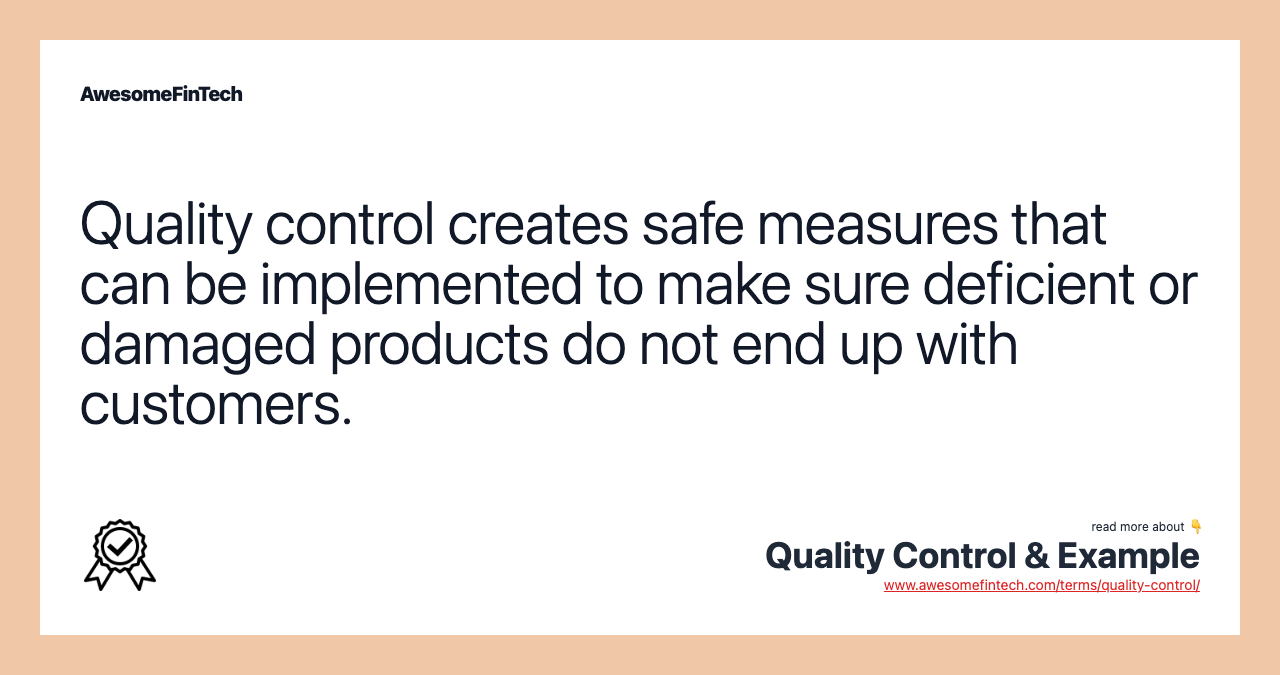
Understanding Quality Control
Quality control involves testing units and determining if they are within the specifications for the final product. The purpose of the testing is to determine any needs for corrective actions in the manufacturing process. Good quality control helps companies meet consumer demands for better products.
Quality testing involves each step of the manufacturing process. Employees often begin with the testing of raw materials, pull samples from along the manufacturing line, and test the finished product. Testing at the various stages of manufacturing helps identify where a production problem is occurring and the remedial steps it requires to prevent it in the future.
The quality control used in a business is highly dependent on the product or industry. In food and drug manufacturing, quality control includes ensuring the product does not make a consumer sick, so the company performs chemical and microbiological testing of samples from the production line. Because the appearance of prepared food affects consumer perception, the manufacturers may prepare the product according to its package directions for visual inspection.
In automobile manufacturing, quality control focuses on how parts fit together and interact and ensure engines operate smoothly and efficiently. In electronics, testing might involve using meters that measure the flow of electricity.
Quality Control Methods
There are several methods of measuring the performance of quality control. A quality control chart is a graphic that depicts whether sampled products or processes are meeting their intended specifications — and, if not, the degree by which they vary from those specifications. When each chart analyzes a specific attribute of the product, it is called a univariate chart. When a chart measures variances in several product attributes, it is called a multivariate chart.
X-Bar Chart
Randomly selected products are tested for the given attribute or attributes the chart is tracking. A common form of a quality control chart is the X-Bar Chart, where the y-axis on the chart tracks the degree to which the variance of the tested attribute is acceptable. The x-axis tracks the samples tested. Analyzing the pattern of variance depicted by a quality control chart can help determine if defects are occurring randomly or systematically.
Taguchi Method
The Taguchi Method of quality control is another approach that emphasizes the roles of research and development, product design, and product development in reducing the occurrence of defects and failures in products. The Taguchi Method considers design to be more important than the manufacturing process in quality control and tries to eliminate variances in production before they can occur.
100% Inspection Method
This 100% inspection method is a quality control process that involves looking at and assessing all parts of a product. This type of quality control is done to rule out flaws in products. This method is often used to evaluate valuable metals and produce. When conducting the 100% inspection method calls for data about the manufacturing process and software to analyze inventory.
The challenge for using this method is that looking at every single item that makes up a product is expensive, and it could destabilize or render the product unusable. For example, if you use this method to examine organic strawberries, you would risk the delicate berries being bruised or mushed, rendering them unsellable to customers.
Quality control methods help standardize both production and reactions to quality issues in various industries from food production to automobile manufacturing.
The Role of Quality Control Inspectors
Quality control inspectors protect the consumer from defective products and the company from damage to its reputation due to inferior manufacturing processes. If the testing process reveals issues with the product, the inspector can fix the problem himself, return the product for repairs, or tag the product for rejection. When issues arise, the inspector notifies supervisors and works with them to correct the problem.
The Benefits of Quality Control
Implementing quality control procedures ensures you are selling the best products to your customers. In addition, practicing quality control has a positive impact on employee conduct. Quality control can inspire employees to create high-quality goods leading to greater customer satisfaction.
Quality control protocols may help you lower your inspection costs and use your resources in a more cost-effective manner, too.
Example of Quality Control
In 1986, Motorola, Inc. created a quality control methodology called Six Sigma, which uses data-driven review to keep defects to a minimum. The process focused on cycle-time improvement to reduce defects in its manufacturing of products to no more than 3.4 occurrences per million units.
This methodology was created to minimize mistakes while documenting all the manufacturing procedures.
Motorola introduced this method because, at the time, they faced fierce competition from similar companies overseas, primarily the success of the Japanese manufacturing market, and complaints by Motorola's customers were high.
After implementing this then-new form of quality control, the company's performance improved dramatically. By the end of the initial five-year period (1986-1991), Motorola had reached its target for improvement in every sector of business.
The continued use of Six Sigma and Lean Six Sigma (another form) occurs in the 21st century and is used by Microsoft and local governments. Six Sigma uses a five-factor approach (DMAIC) to define, measure, analyze, improve, and control to help companies identify and address quality control problems and fix them.
Quality Control FAQs
What Does Quality Control Mean?
Quality control means how a company measures that its product quality is maintained (if it is good) or improved if need be. Quality control can be done in many ways, from testing products, reviewing manufacturing processes, and creating benchmarks. This is all done to monitor significant variations in a product.
What Are the 4 Types of Quality Control?
There are several methods of quality control. These include an x-bar chart, Six Sigma, 100% inspection mode, and the Taguchi Method.
Why Is Quality Control Important?
Quality control ensures that defective goods do not go out to the public. Companies that have quality control methods in place often have employees who pay close attention to their work.
In food and drug manufacturing, quality control prevents products that make customers sick, and in manufacturing, quality control can ensure that accidents don't happen when people use a product.
What Is an Example of Quality Control?
An aspect of quality control in food production would be overseeing the ingredient specifications, reviewing supplier lists, and ensuring the facility where the food product is made is sanitary.
What Is the Difference Between Quality Assurance and Quality Control?
Quality assurance is about how a process is performed or how a product is made. For example, if milk is labeled non-fat, the factory would have a method to ensure the type of milk in the carton is reflected by the label on the package. Quality control focuses on quality management and how the overall quality of the products overseen by the company.
The Bottom Line
Having quality control in place within a business can only help ensure product quality and the overall success of a business. The environment of quality control influences employees' attitudes about the workplace and creates a sense of ownership in the products and company as a whole. Quality control can be done in various ways, from training personnel to creating data-driven tools to test products and set standards. Quality control methods help create a safe work environment and product safety that benefits customers and the company alike.
Related terms:
Acceptance Sampling
Acceptance sampling is a statistical quality-control measure that lets a company determine the quality of a product lot by testing randomly selected samples. read more
Benchmark
A benchmark is a standard against which the performance of a security, mutual fund or investment manager can be measured. read more
ISO 9000
ISO 9000 is a set of international standards, established by the International Organization for Standardization, that apply to quality management systems. read more
Lean Six Sigma
Lean Six Sigma is a team-focused managerial approach that seeks to improve performance by eliminating waste and defects. read more
Mergers and Acquisitions (M&A)
Mergers and acquisitions (M&A) refers to the consolidation of companies or assets through various types of financial transactions. read more
Production Rate
Production rate is the pace at which units of a product are manufactured within a scheduled time frame. Production rate can also refer to the amount of time it takes to produce one unit of a good. read more
Quality Control Chart
A quality control chart is a graphic that depicts whether sampled products or processes are meeting their intended specifications. read more
Raw Materials
Raw materials are commodities companies use in the primary production or manufacturing of goods. read more
Six Sigma
A quality-control program developed in 1986 to improve efficiency. Since then, it has evolved into a more general business-management philosophy. read more
Statistical Significance & Uses
Statistical significance is a determination that a relationship between two or more variables is caused by something other than chance. read more