
Production Rate
Production rate, in terms of manufacturing, refers to the number of goods that can be produced during a given period of time. With fewer errors and ultimately less downtime in the process to correct the errors, the production process can flow more smoothly and help to boost the overall production rate. The process of monitoring and ensuring the highest product quality is maintained throughout the production process is called quality control (QC). Quality control involves testing of the product's quality to determine if it meets the predetermined standards. The production rate for construction companies might be the rate at which workers should complete a certain task, such as a road. Management might review the elements of production to discern where errors or slowdowns occur and then take measures to address those issues to increase the production rate.
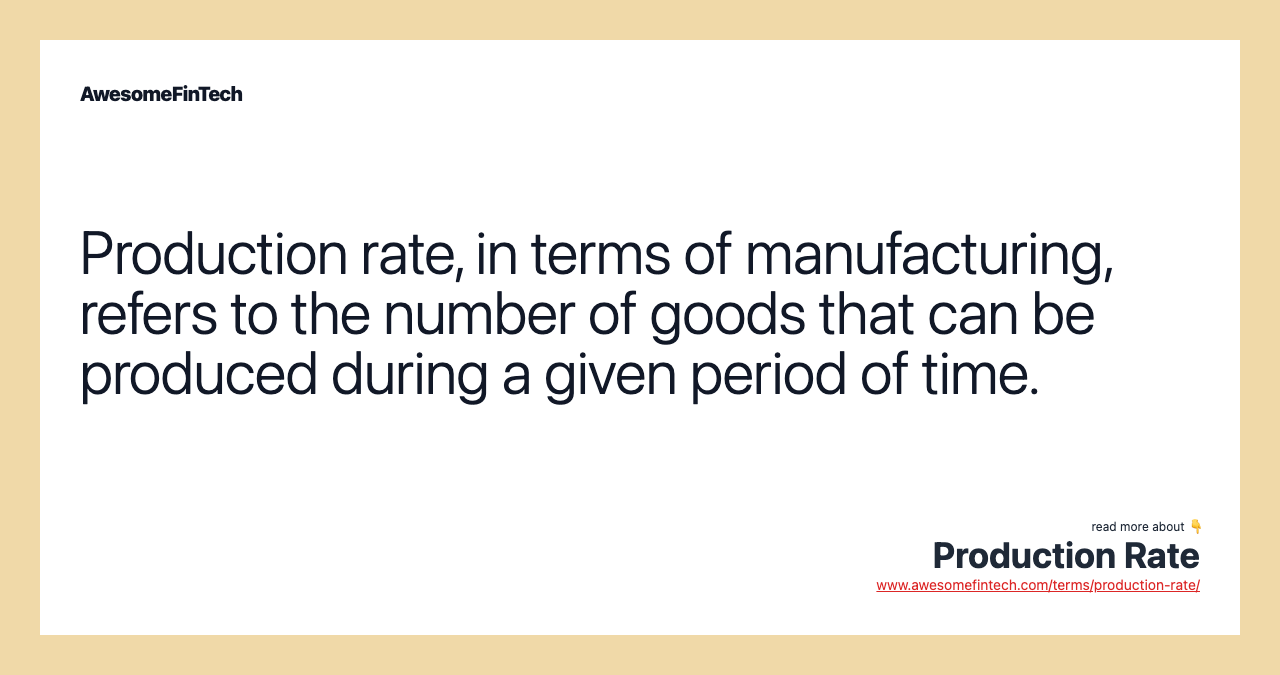
What Is the Production Rate?
Production rate, in terms of manufacturing, refers to the number of goods that can be produced during a given period of time. Alternatively, the production rate is also the amount of time it takes to produce one unit of a good.
Production rate, in the construction industry, is the rate at which workers are expected to complete a certain segment, such as a road or building. The production rate will depend on the speed at which workers are expected to operate, which is typically categorized as slow, average, or fast.
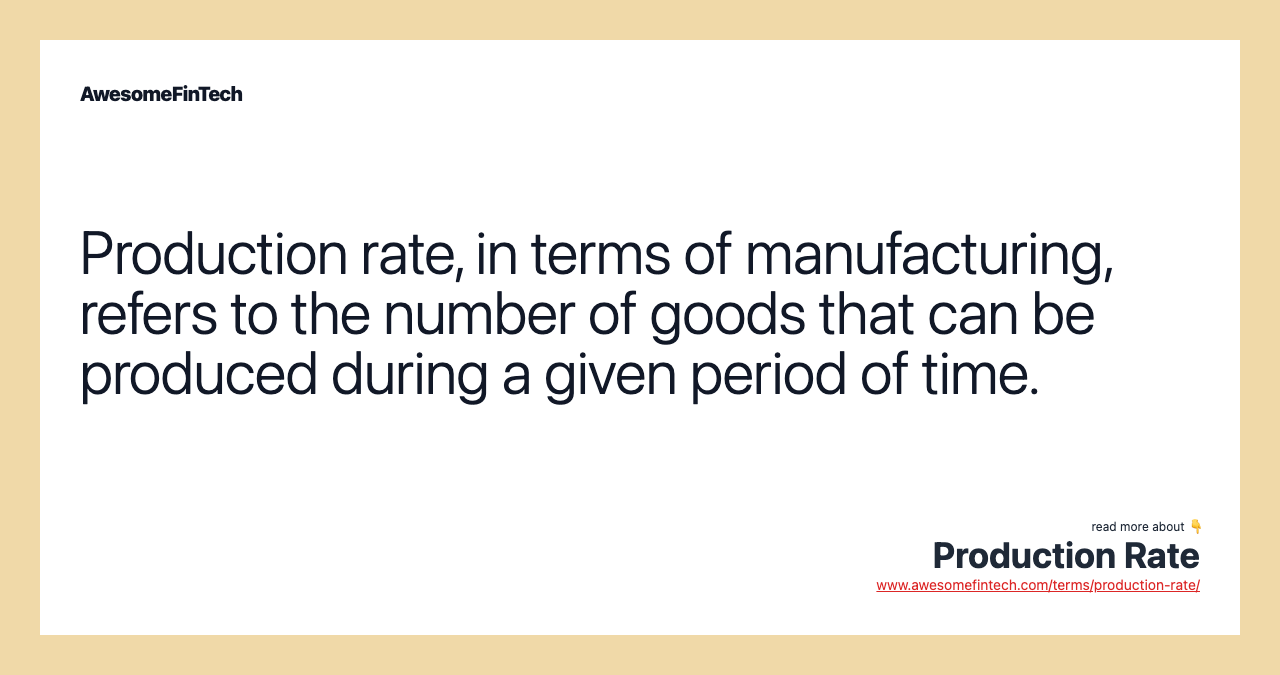
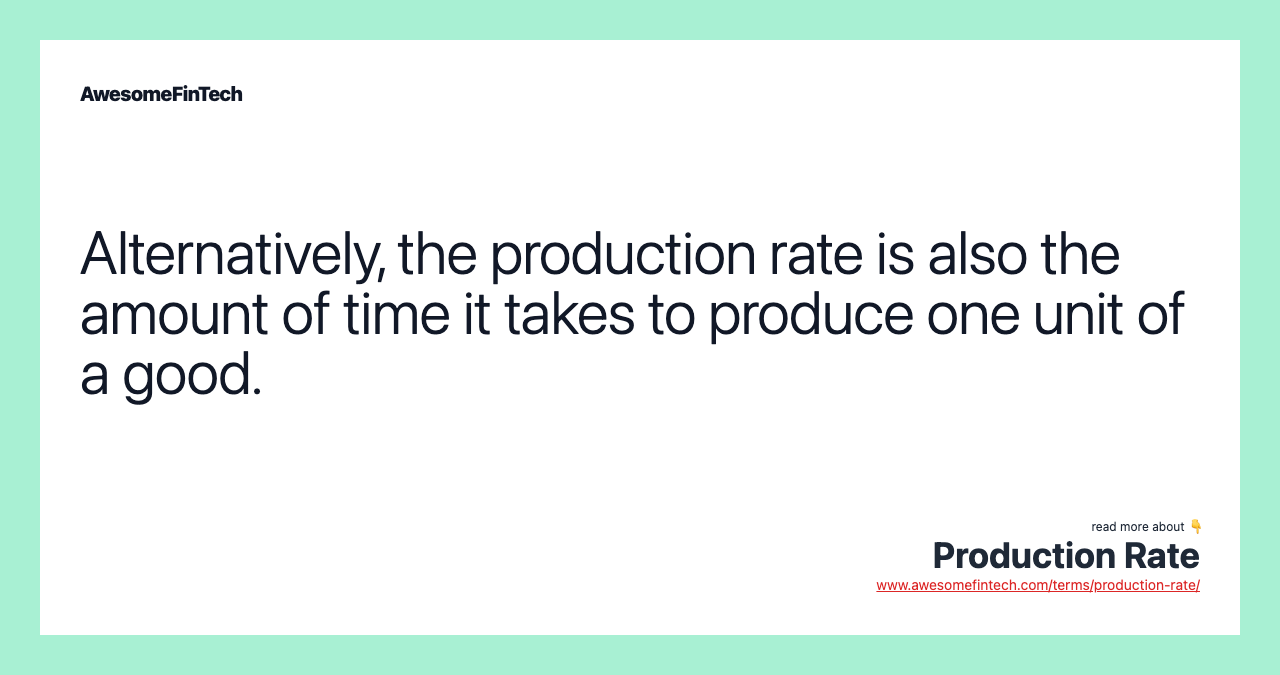
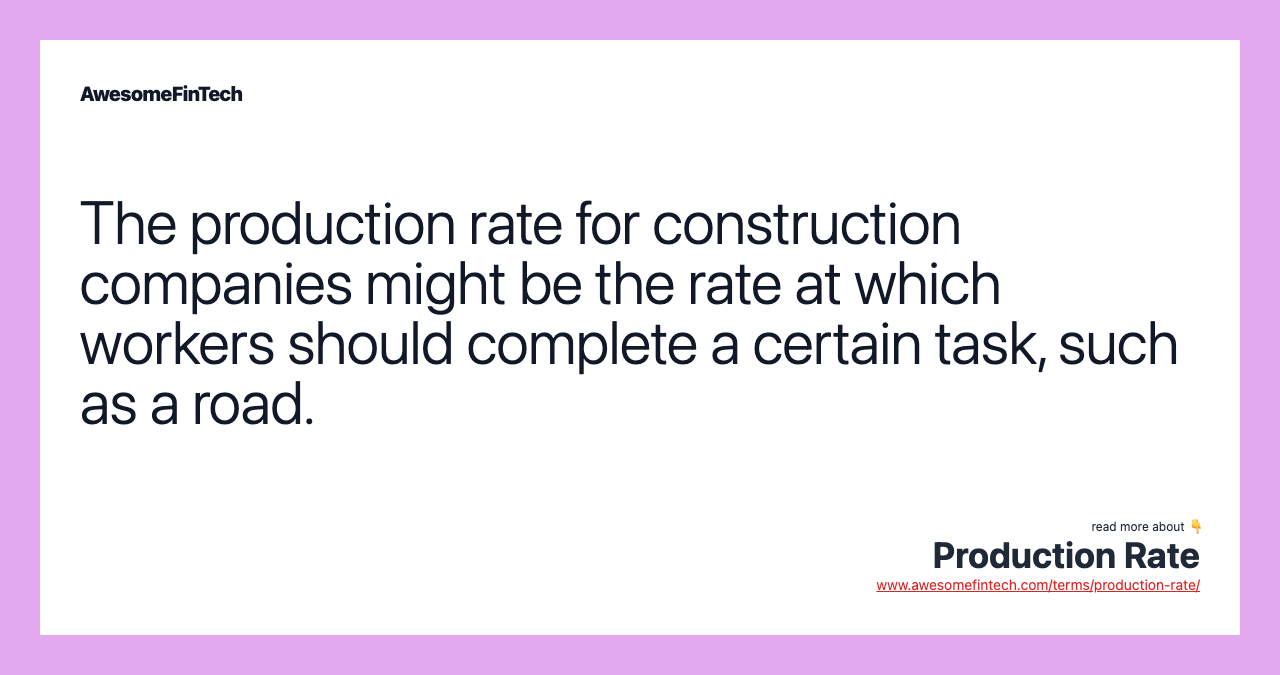
Understanding Production Rate
Companies often strive for high production rates to help lower the time and cost of a project or the production process. However, a higher production rate can also lead to a decrease in quality if more mistakes are made as employees push to have more units produced or more of a building completed. As a result, there is a point in the process at which a decrease in quality can lead to higher costs, even as the production or construction process is taking less time.
The production rate can be impacted by both internal and external factors. If there is not adequate training of employees or enough skilled personnel to perform the production work, the production rate will likely decline. Outside factors can also affect the production rate of any operation. For example, if a crucial source of raw materials becomes inaccessible or limited, the production rate may be forced to slow or halt.
Production rate can be expressed as a factor of the maximum output possible minus the rate of defects in the products. Any production line can expect to see some degree of flaws in the items produced. The frequency and severity of the defects will reduce the number of viable, usable products that will be generated.
Quality Control
Management might review the elements of production to discern where errors or slowdowns occur and then take measures to address those issues to increase the production rate. The process of monitoring and ensuring the highest product quality is maintained throughout the production process is called quality control (QC).
Quality control involves testing of the product's quality to determine if it meets the predetermined standards. QC also looks to make improvements to the process and establish controls as to how the process is to be carried out. For example, QC might limit a portion of the process to specific employees that have specialized training to cut down on errors and reduce the chances of employees performing a task for which they do not have training.
With fewer errors and ultimately less downtime in the process to correct the errors, the production process can flow more smoothly and help to boost the overall production rate.
Special Considerations
The nature of the material and the complexity of the product can affect the production rate. The more intricate and precise the end product is, the more time may be needed to complete the product. As manufacturing becomes more efficient, through new methods or techniques that reduce the possibility of defects in the process, the production rate will likely increase.
Production rate can play a significant factor in pricing the product. Rapidly produced, lower-quality products can often be set at a low price in the market since the less time needed for production translates into lower labor costs required to make each unit. However, a higher production rate might translate into more units produced, but if each unit has a low price, there's less profit per unit being generated. As a result, the company would need to produce at an elevated production rate to achieve higher profitability.
However, goods that require a longer time investment, with a slower production rate, would need to be priced higher to compensate for the added labor cost and outlays that went into creating the product. Whether the higher price is acceptable to the company's prospective customers can depend on if they're willing to pay more for the higher quality and the price and quality of comparable products being offered by the competition.
Example of Production Rate
For example, let's say that workers at a manufacturing plant can produce 5,000 units per week using 50 hours of labor. As a result, the production rate per hour would be 100 units (5,000 / 50 hours) minus any defective units. The 100 unit per hour production rate could be used as a baseline number for comparative purposes. So, as the company makes adjustments and improvements, management and QA can monitor if the hourly production rate and the number of defects increase or decrease.
Related terms:
Accounting
Accounting is the process of recording, summarizing, analyzing, and reporting financial transactions of a business to oversight agencies, regulators, and the IRS. read more
Ending Inventory
Ending inventory is a common financial metric measuring the final value of goods still available for sale at the end of an accounting period. read more
Product Lifecycle Management (PLM)
Product lifecycle management refers to the handling of a good as it moves through five typical stages of its lifespan, from development to decline. read more
Productivity
Productivity measures the efficiency of production in macroeconomics. Read about productivity in the workplace and how productivity impacts investments. read more
Quality Control & Example
Quality control is a process by which a business ensures that product quality is maintained or improved. Discover what quality control is and how it works. read more
Raw Materials
Raw materials are commodities companies use in the primary production or manufacturing of goods. read more
What Is Trade?
A basic economic concept that involves multiple parties participating in the voluntary negotiation. read more