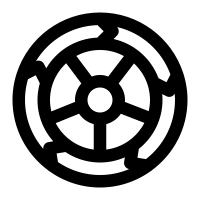
Six Sigma
5. Finally, the team adds controls to the process to ensure it does not regress and become ineffective once again. Lean Six Sigma is a team-focused managerial approach that seeks to improve performance by eliminating waste and defects. In recent years, Six Sigma has evolved into a more general business-management philosophy, focused on meeting customer requirements, improving customer retention, and improving and sustaining business products and services. Therefore, practitioners of Six Sigma are those business people who use statistics, financial analysis, and project management to achieve improved business functionality. 1. A team of people, led by a Six Sigma champion, defines a faulty process on which to focus, decided through an analysis of company goals and requirements.
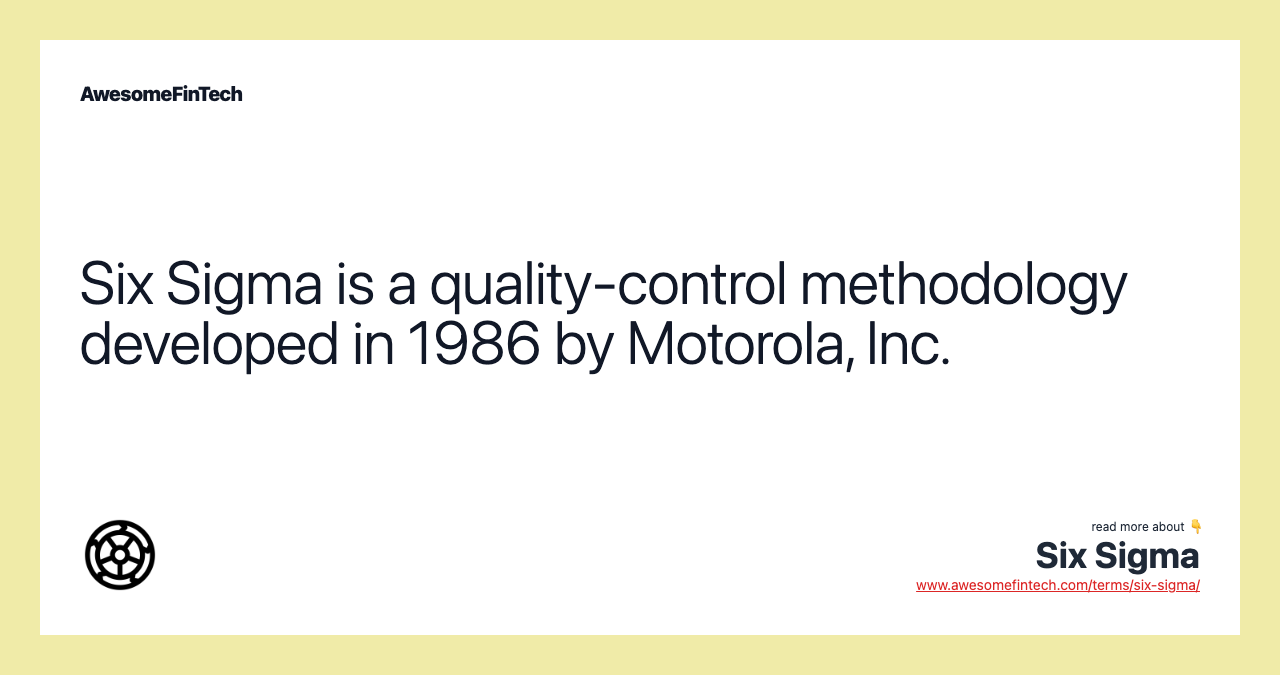
What Is Six Sigma?
Six Sigma is a quality-control methodology developed in 1986 by Motorola, Inc. The method uses a data-driven review to limit mistakes or defects in a corporate or business process. Six Sigma emphasizes cycle-time improvement while at the same time reducing manufacturing defects to a level of no more than 3.4 occurrences per million units or events. In other words, the system is a method to work faster with fewer mistakes.
Six Sigma points to the fact that, mathematically, it would take a six-standard-deviation event from the mean for an error to happen. Because only 3.4 out of a million randomly (and normally) distributed, events along a bell curve would fall outside of six-standard-deviations (where sigma stands in for "standard deviation").
In recent years, Six Sigma has evolved into a more general business-management philosophy, focused on meeting customer requirements, improving customer retention, and improving and sustaining business products and services. Six Sigma applies to all industries. Many vendors, including Motorola itself, offer Six Sigma training with the special certifications carrying the names of yellow belt, green belt, and black belt.
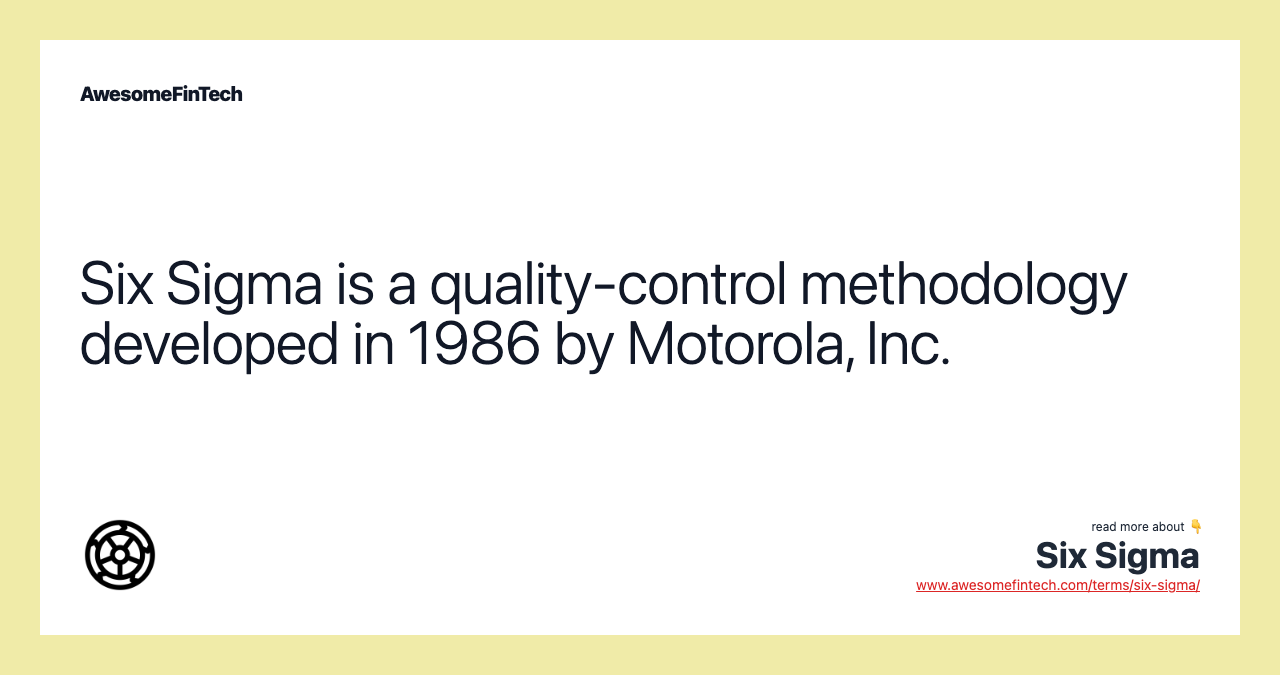
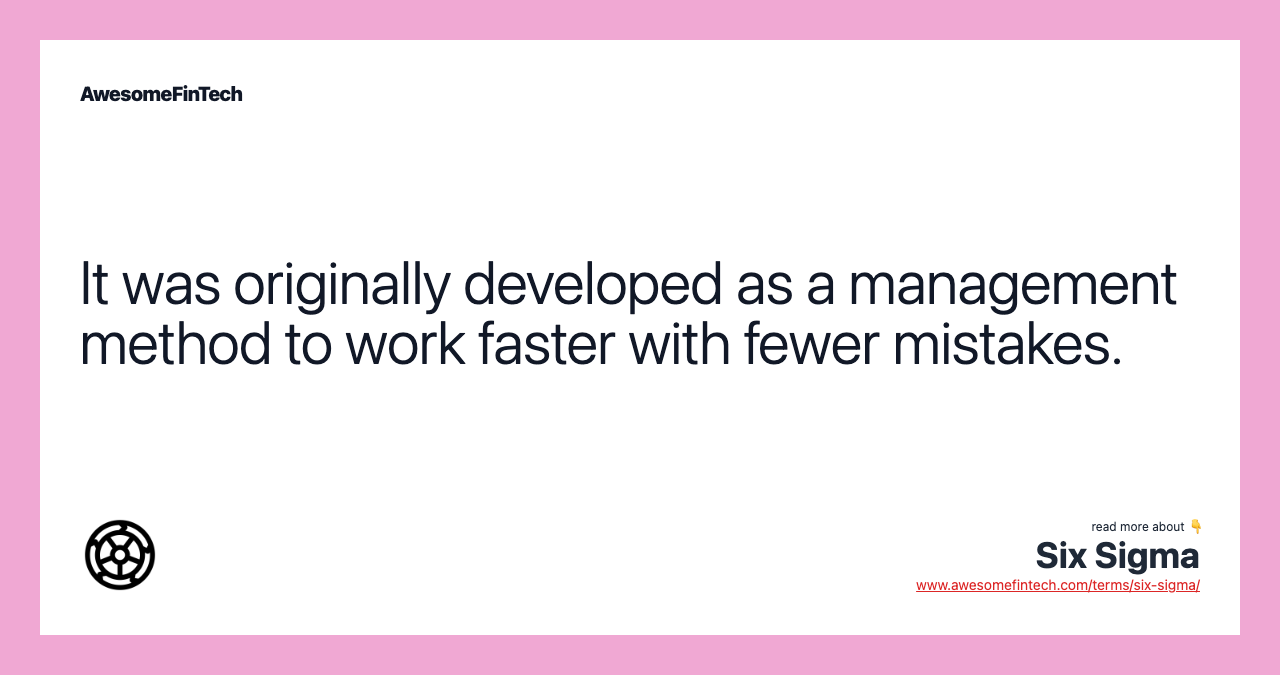
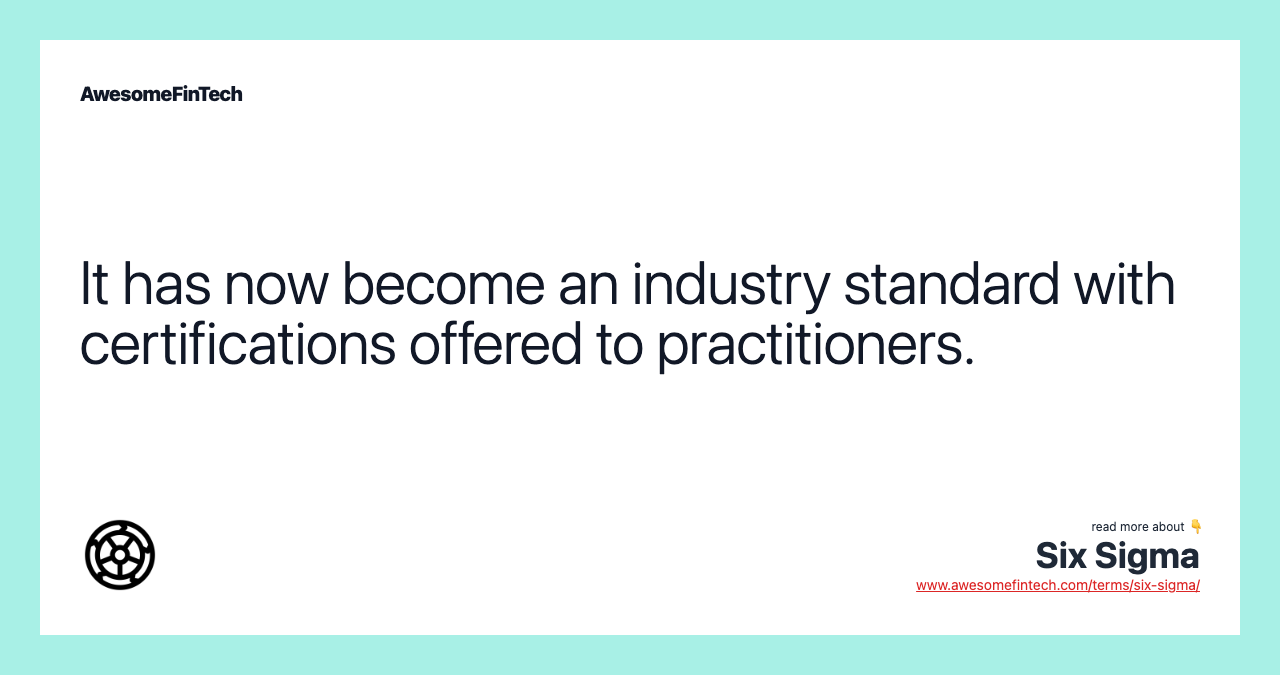
Understanding Six Sigma
Six Sigma represents a management ideology, which focuses on statistical improvements to a business process. It advocates for qualitative measurements of success over qualitative markers. Therefore, practitioners of Six Sigma are those business people who use statistics, financial analysis, and project management to achieve improved business functionality.
Six Sigma evolved to define numerous ideas within the business sphere and is sometimes confusing. First, it's a statistical benchmark. Any business process, which produces less than 3.4 defects per 1 million chances, is considered efficient. A defect is anything produced outside of consumer satisfaction.
Second, it is a training and certification program, which teaches the core principles of Six Sigma. Practitioners may achieve the Six Sigma certification belt levels, ranging from white belt to black belt. Finally, it's a philosophy, which promotes the idea that all business processes can be measured and optimized.
The 5 Steps of Six Sigma
True believers and practitioners in the Six Sigma method follow an approach called DMAIC, which stands for define, measure, analyze, improve, and control. It is a statistically driven methodology that companies implement as a mental framework for business process improvement. The ideology behind DMAIC is that a business may solve any seemingly unsolvable problem by following the DMAIC steps.
- A team of people, led by a Six Sigma champion, defines a faulty process on which to focus, decided through an analysis of company goals and requirements. This definition outlines the problem, goals, and deliverables for the project.
- The team measures the initial performance of the process. These statistical measures make up a list of potential inputs, which may cause the problem and help the team understand the process's benchmark performance.
- Then the team analyzes the process by isolating each input, or potential reason for the failure, and testing it as the root of the problem. Through analysis, the team identifies the reason for process error.
- From there, the team works to improve system performance.
- Finally, the team adds controls to the process to ensure it does not regress and become ineffective once again.
Lean Six Sigma is a team-focused managerial approach that seeks to improve performance by eliminating waste and defects. It combines Six Sigma methods and tools and the lean manufacturing-lean enterprise philosophy, striving to reduce waste of physical resources, time, effort, and talent while assuring quality in production and organizational processes. Under the tenets of Lean Six Sigma, any use of resources that do not create value for the end customer is considered a waste and should be eliminated.
Real-World Examples of Six Sigma
Six Sigma is used by both corporations and local governments. Below are two examples of how six sigma improved operational efficiency, saved money, and increased customer satisfaction.
Microsoft Inc.
Microsoft Corporation (MSFT) is one of the largest software producers in the world. In an effort to improve the reliability and availability of its networks worldwide, Microsoft implemented Six Sigma methodologies as outlined on the company's website. The goal was to use a robust data-driven process to help eradicate any defects in their systems and data centers to systematically reduce IT (information technology) infrastructure failures.
The company first established standards for all of its hardware and software to create a baseline measurement for detecting defects. Microsoft used root-cause analysis, including collecting data from past high-priority incidents, server failures, and recommendations from product group members and customers. Using the historical data, Microsoft established baseline standards from which to measure going forward.
Large amounts of data were collected on a daily and weekly basis from various servers. Data analysis and reporting identified the defects and remediation steps for each defect were then established. The incidents were prioritized based on how severe the defects impacted the business and the company's underlying services.
Using Six Sigma methodologies, the teams executed eradication initiatives of the defects. As a result, remediation of defects improved by 40% within the first year. The mean or average time between server failures improved from 18 days to 125 days. As a result of Six Sigma, Microsoft improved the availability of its servers, boosted customer productivity, and increased customer satisfaction.
Local Government
As reported by TheVoiceCalifornia.com, in Ventura County, California, the county is crediting the use of Lean Six Sigma for a savings of $43 million. The local government began to use the program on a county-wide level in 2008 and has trained more than 5,000 employees on employing the methodology. The county states the savings are coming from hard budget items, which no longer need funding as well as savings in employee hours.
Related terms:
Acceptable Quality Level (AQL)
An acceptable quality level (AQL) is a statistical measurement of the maximum acceptable number of defective goods in a particular sample size. read more
Accounting
Accounting is the process of recording, summarizing, analyzing, and reporting financial transactions of a business to oversight agencies, regulators, and the IRS. read more
Bell Curve
A bell curve describes the shape of data conforming to a normal distribution. read more
Deliverables
Deliverables in project management refer to the quantifiable goods or services that will be provided upon the completion of a project. read more
Financial Analysis
Financial analysis is the process of assessing specific entities to determine their suitability for investment. read more
Lean Enterprise
Lean enterprise is a production and management philosophy that considers any part of the enterprise that does not add value to be superfluous. read more
Lean Six Sigma
Lean Six Sigma is a team-focused managerial approach that seeks to improve performance by eliminating waste and defects. read more
Mean
The mean is the mathematical average of a set of two or more numbers that can be computed with the arithmetic mean method or the geometric mean method. read more
PDCA Cycle
The PDCA Cycle, which stands for Plan-Do-Check-Act, is a problem-solving iterative technique that uses four steps to improve business processes. read more
Project Management
Project management involves the planning and organizing of a company's resources to move a specific task, event, or duty toward completion. read more