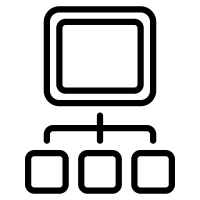
Operations Management (OM)
Operations management (OM) is the administration of business practices to create the highest level of efficiency possible within an organization. Operations managers acquire, develop, and deliver goods to clients based on client needs and the abilities of the company. Operations management handles various strategic issues, including determining the size of manufacturing plants and project management methods and implementing the structure of information technology networks. Operations management is concerned with controlling the production process and business operations in the most efficient manner possible. Modern operations management revolves around four theories: business process redesign (BPR), reconfigurable manufacturing systems, Six Sigma, and lean manufacturing. Other operational issues include the management of inventory levels, including work-in-process levels and raw materials acquisition, quality control, materials handling, and maintenance policies.
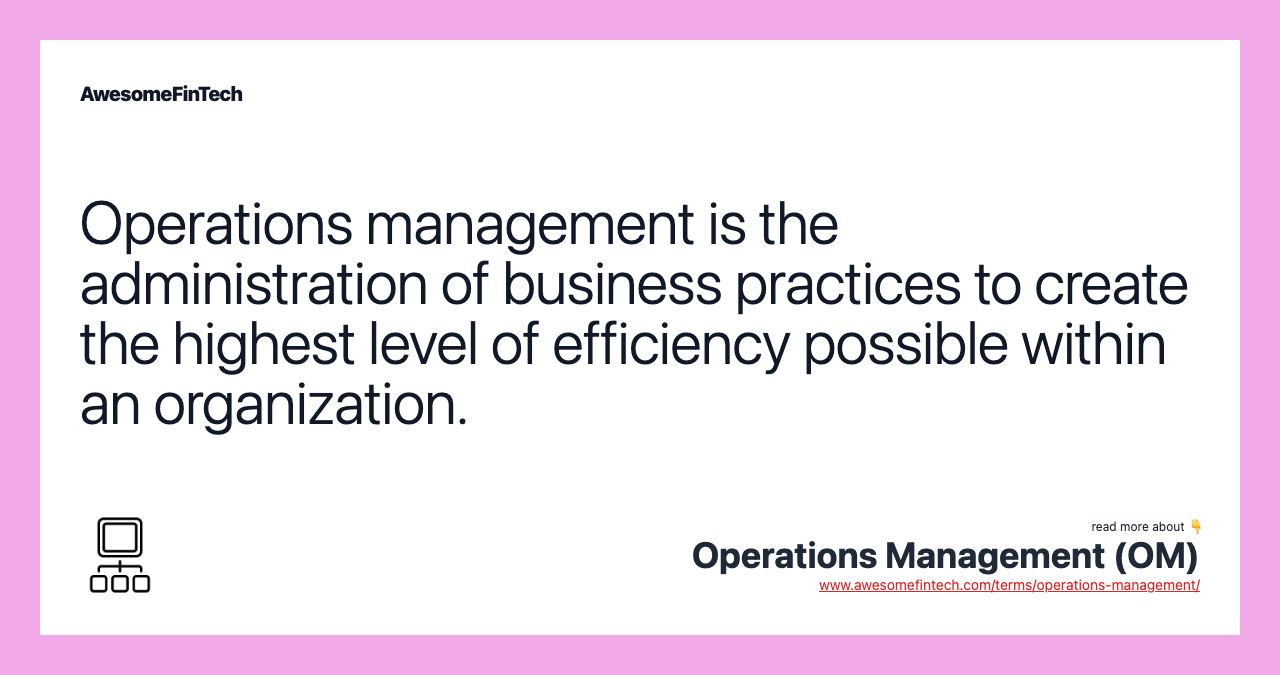
What Is Operations Management (OM)?
Operations management (OM) is the administration of business practices to create the highest level of efficiency possible within an organization. It is concerned with converting materials and labor into goods and services as efficiently as possible to maximize the profit of an organization. Operations management teams attempt to balance costs with revenue to achieve the highest net operating profit possible.
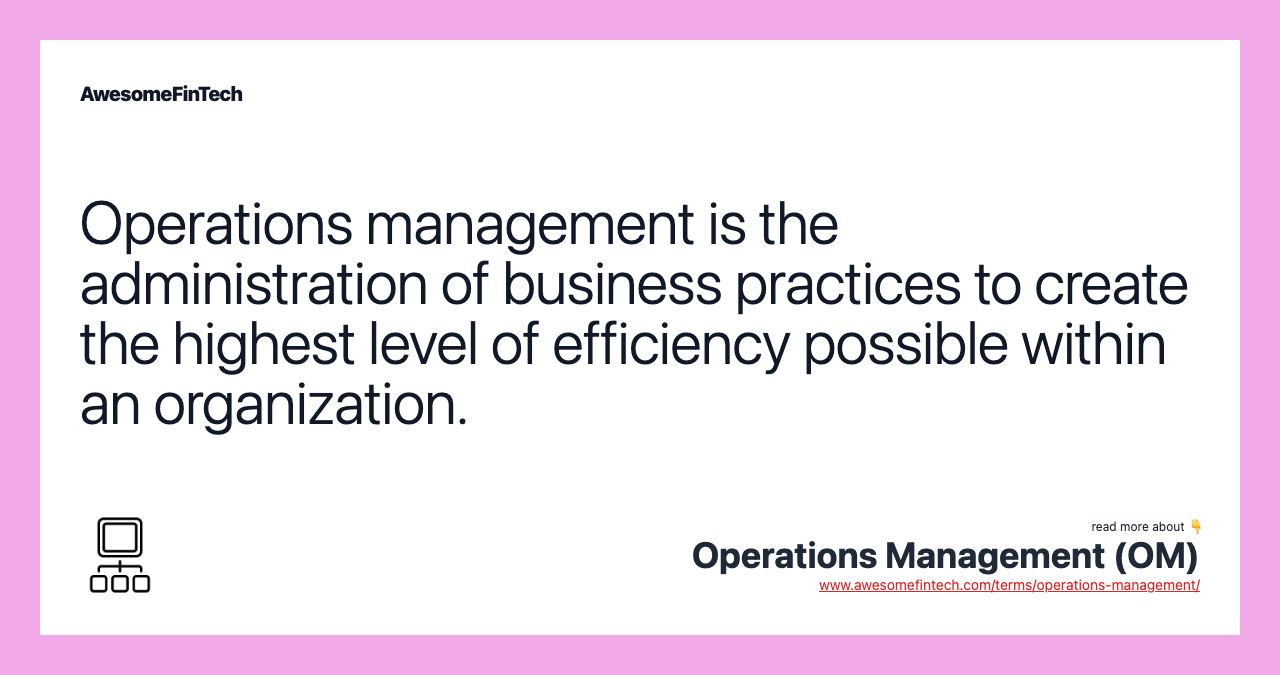
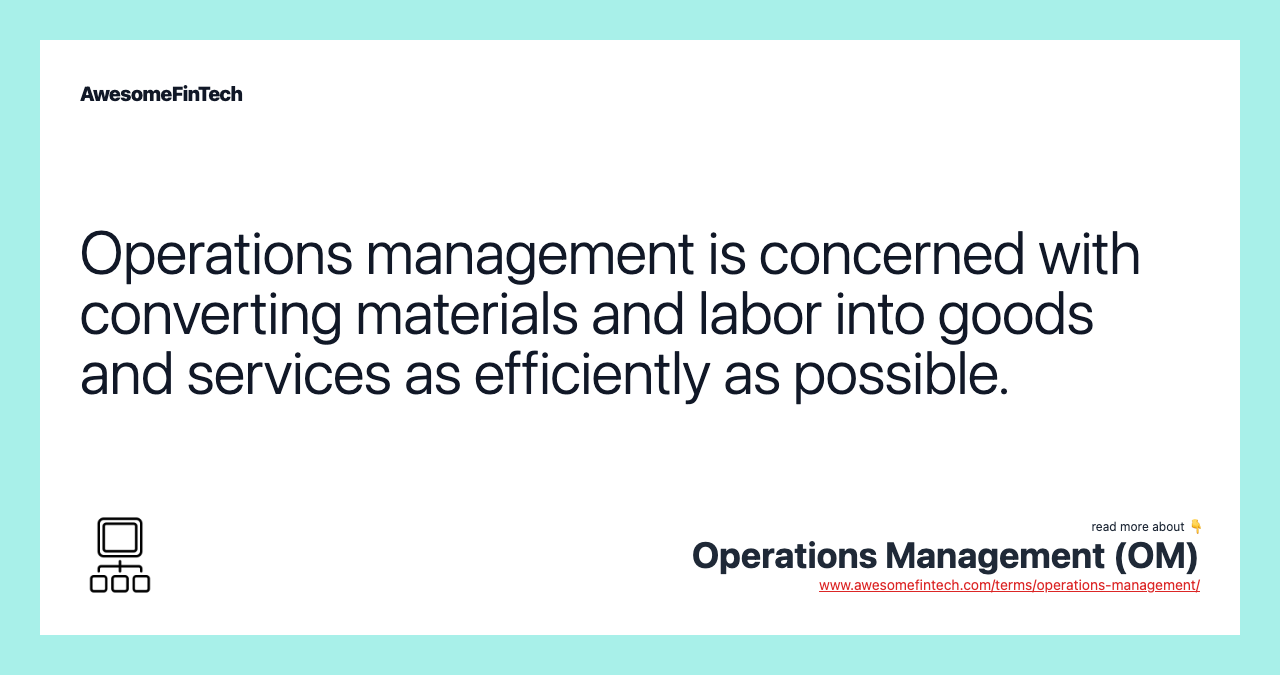
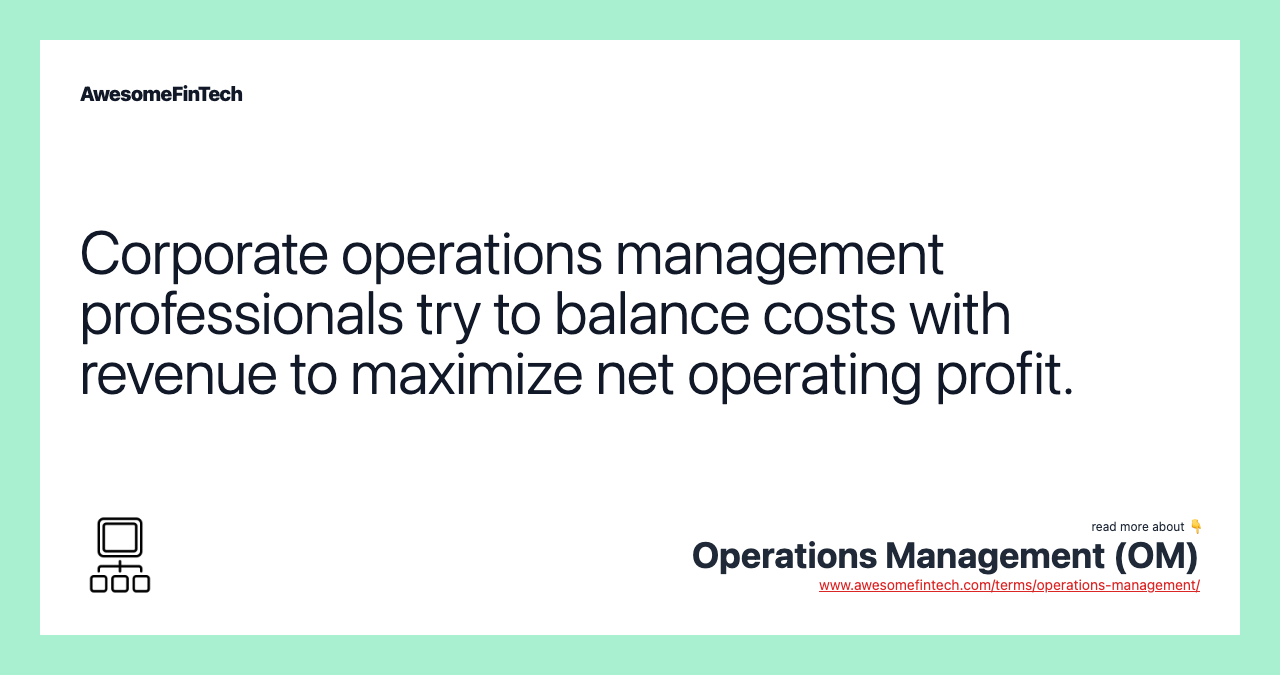
Understanding Operations Management (OM)
Operations management involves utilizing resources from staff, materials, equipment, and technology. Operations managers acquire, develop, and deliver goods to clients based on client needs and the abilities of the company.
Operations management handles various strategic issues, including determining the size of manufacturing plants and project management methods and implementing the structure of information technology networks. Other operational issues include the management of inventory levels, including work-in-process levels and raw materials acquisition, quality control, materials handling, and maintenance policies.
Operations management entails studying the use of raw materials and ensuring minimal waste occurs. Operations managers utilize numerous formulas, such as the economic order quantity formula to determine when and how large of an inventory order to process and how much inventory to hold on hand.
The combination of understanding and coordinating the work of a company are central to becoming a successful operations manager.
Operations and Supply Chain Management
A critical function of operations management relates to the management of inventory through the supply chain. To be an effective operations management professional, one must be able to understand the processes that are essential to what a company does and get them to flow and work together seamlessly. The coordination involved in setting up business processes in an efficient way requires a solid understanding of logistics.
An operations management professional understands local and global trends, customer demand, and the available resources for production. Operations management approaches the acquisition of materials and the use of labor in a timely, cost-effective manner to deliver customer expectations. Inventory levels are monitored to ensure excessive quantities are on hand. Operations management is responsible for finding vendors that supply the appropriate goods at reasonable prices and have the ability to deliver the product when needed.
Another large facet of operations management involves the delivery of goods to customers. This includes ensuring products are delivered within the agreed time commitment. Operations management also typically follows up with customers to ensure the products meet quality and functionality needs. Finally, operations management takes the feedback received and distributes the relevant information to each department to use in process improvement.
Special Considerations
Operations managers are involved in coordinating and developing new processes while reevaluating current structures. Organization and productivity are two key drivers of being an operations manager, and the work often requires versatility and innovation.
An MBA in operations management can give someone a global perspective on industry trends and an awareness of any financial regulations and political uncertainties that can affect an organization. It also gives someone a solid grasp of the inherent complexities and the tools needed to respond well to change.
What Is the Purpose of Operations Management (OM)?
Operations management is concerned with controlling the production process and business operations in the most efficient manner possible. OM professionals attempt to balance operating costs with revenue to maximize net operating profit.
What Are Some Systems of OM?
Modern operations management revolves around four theories: business process redesign (BPR), reconfigurable manufacturing systems, Six Sigma, and lean manufacturing. BPR is focused on analyzing and designing workflow and business processes within a company. The goal of BPR is to help companies dramatically restructure the organization by designing the business process from the ground up. Reconfigurable manufacturing systems are designed to incorporate accelerated change in structure, hardware, and software components.
This allows systems to adjust rapidly to the capacity to which they can continue production and how efficiently they function in response to market or intrinsic system changes. Six Sigma is an approach that focuses on quality. The word "six" references the control limits, which are placed at six standard deviations from the normal distribution mean. Tools used within the Six Sigma process include trending charts, potential defect calculations, and other ratios. Lean manufacturing is a systematic elimination of waste within the manufacturing process. This theory sees resource use for any reason other than value creation for customers as wasteful and seeks to eliminate wasteful resource expenditures as much as possible.
What Is an Example of Operations Management?
Operations management is prevalent in the healthcare sector. The current healthcare system overuses expensive, technological, and emergency-based treatment. High costs from care often remain uncompensated due to uninsured patients. A prevalence of services in expensive settings creates a burden on taxpayers, health insurance holders, and healthcare institutions themselves.
Related terms:
Business Process Redesign (BPR)
A business process redesign is an overhaul of a company's central business processes to effect substantial changes. read more
Economic Order Quantity (EOQ) & Formula
Economic order quantity (EOQ) is the ideal order quantity that a company should make for its inventory given a set cost of production, demand rate, and other variables. read more
Factors of Production
Factors of production are the inputs needed for the creation of a good or service. The factors of production include land, labor, entrepreneurship, and capital. read more
Just in Time (JIT) Inventory
A just-in-time (JIT) inventory system is a management strategy that aligns raw-material orders from suppliers directly with production schedules. read more
Mergers and Acquisitions (M&A)
Mergers and acquisitions (M&A) refers to the consolidation of companies or assets through various types of financial transactions. read more
Material Requirements Planning (MRP)
Material requirements planning is among the first software-based integrated information systems designed to improve productivity for businesses. read more
Operating Profit
Operating profit is the total earnings from a company's core business operations, excluding deductions of interest and tax. read more
Productivity
Productivity measures the efficiency of production in macroeconomics. Read about productivity in the workplace and how productivity impacts investments. read more
Supply Chain Management (SCM)
Supply chain management (SCM) is the management of the flow of goods and services as well as overseeing the processes of converting original materials into final products. read more