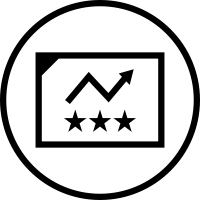
Lean Six Sigma
Lean Six Sigma is a team-focused managerial approach that seeks to improve performance by eliminating waste and defects. Lean Six Sigma was introduced by Michael George and Robert Lawrence Jr. in their 2002 book _Lean Six Sigma: Combining Six Sigma with Lean Speed_ as a combination and refinement of lean enterprise and Six Sigma tenets. It combines Six Sigma methods and tools and the lean manufacturing/lean enterprise philosophy, striving to eliminate waste of physical resources, time, effort and talent while assuring quality in production and organizational processes. Six Sigma's DMAIC phases are utilized in Lean Six Sigma. Lean Six Sigma can see its origins in the United States in the 1980s as a combination of management principles and processes that originated in Japan.
What Is Lean Six Sigma?
Lean Six Sigma is a team-focused managerial approach that seeks to improve performance by eliminating waste and defects. It combines Six Sigma methods and tools and the lean manufacturing/lean enterprise philosophy, striving to eliminate waste of physical resources, time, effort and talent while assuring quality in production and organizational processes. Simply put, under the tenets of Lean Six Sigma any use of resources that doesn't create value for the end customer is considered a waste and should be eliminated.
Understanding Lean Six Sigma
Lean Six Sigma can see its origins in the United States in the 1980s as a combination of management principles and processes that originated in Japan. In an effort to compete with Japan's better products, U.S. managers adopted some Japanese manufacturing principles that focused on reducing waste in the form of non-value-adding actions. In the 1990s, such principles were adopted by large U.S. manufacturers. Lean Six Sigma was introduced by Michael George and Robert Lawrence Jr. in their 2002 book Lean Six Sigma: Combining Six Sigma with Lean Speed as a combination and refinement of lean enterprise and Six Sigma tenets.
Lean Six Sigma Tenets
The "lean" concept of management lends its focus on the reduction and elimination of eight kinds of waste known as "DOWNTIME," which is an abbreviation of defects, overproduction, waiting, non-utilized talent, transportation, inventory, motion, and extra-processing. "Lean" refers to any method, measure or tool that helps in the identification and elimination of waste.
The term Six Sigma refers to tools and techniques that are used to improve manufacturing processes. It was introduced by an engineer at Motorola in 1986 and inspired by Japan's Kaizen model. It was trademarked by the company in 1993. Its intent is to improve processes by identifying and eliminating the causes of defects and variations in business and manufacturing processes. Six Sigma's DMAIC phases are utilized in Lean Six Sigma. The acronym stands for define, measure, analyze, improve and control and refers to a data-driven method for improving, optimizing and stabilizing business and manufacturing processes.
The combination of lean management concepts and Six Sigma's tools and techniques makes clear what processes are prone to variation and then reduces those variations as a way to ensure continued improvement.
Lean Six Sigma Levels
Lean Six Sigma training uses "Belt" levels to denote expertise similar to Six Sigma.
Related terms:
Accounting
Accounting is the process of recording, summarizing, analyzing, and reporting financial transactions of a business to oversight agencies, regulators, and the IRS. read more
Kaizen
Kaizen is a Japanese business philosophy that focuses on continuous improvement and involves all employees. Kaizen means "change for the better." read more
Lean Enterprise
Lean enterprise is a production and management philosophy that considers any part of the enterprise that does not add value to be superfluous. read more
Manufacturing
Manufacturing is the processing of raw materials into finished goods using tools and processes. read more
PDCA Cycle
The PDCA Cycle, which stands for Plan-Do-Check-Act, is a problem-solving iterative technique that uses four steps to improve business processes. read more
Quality Control & Example
Quality control is a process by which a business ensures that product quality is maintained or improved. Discover what quality control is and how it works. read more
Six Sigma Certification
Six Sigma certification is a verification of an individual's command of a well-regarded method of professional skills development. read more
Six Sigma
A quality-control program developed in 1986 to improve efficiency. Since then, it has evolved into a more general business-management philosophy. read more
Total Quality Management (TQM)
Total quality management (TQM) aims to hold all parties involved in the production process as accountable for the overall quality of the final product or service. read more