
Lean Enterprise
Lean enterprise refers to a production principle stating that any component of a business enterprise that fails to directly benefit a final product is superfluous. Although both terms came into popular usage in the 1990s, the concept itself was devised by Toyota Motor Corporation when it introduced the Toyota Production System (TPS). Developed by Eiji Toyoda and Taiichi Ohno, the Toyota Production System (TPS) integrated socio-technical management philosophy and was practiced between 1948 and 1975. The lean enterprise philosophy was also inspired by telecommunications giant Motorola, which implemented a manufacturing principle known as Lean Six Sigma in 1986. The underlying principles behind lean enterprise were originated by Toyota Motor Corporation's Toyota Production System (TPS) and by Motorola's Lean Six Sigma program, both of which stress removing wasteful production elements. _Value stream:_ This breaks down the life cycle of a product or service, including the acquisition of raw materials, the manufacturing of goods, the sale and delivery of inventory, and the ultimate consumption of items by end-users. _Flow_: If any iteration of the value stream is stagnant or inefficient, it is considered wasteful and antithetical to creating customer value. Lean enterprise refers to a production principle stating that any component of a business enterprise that fails to directly benefit a final product is superfluous.
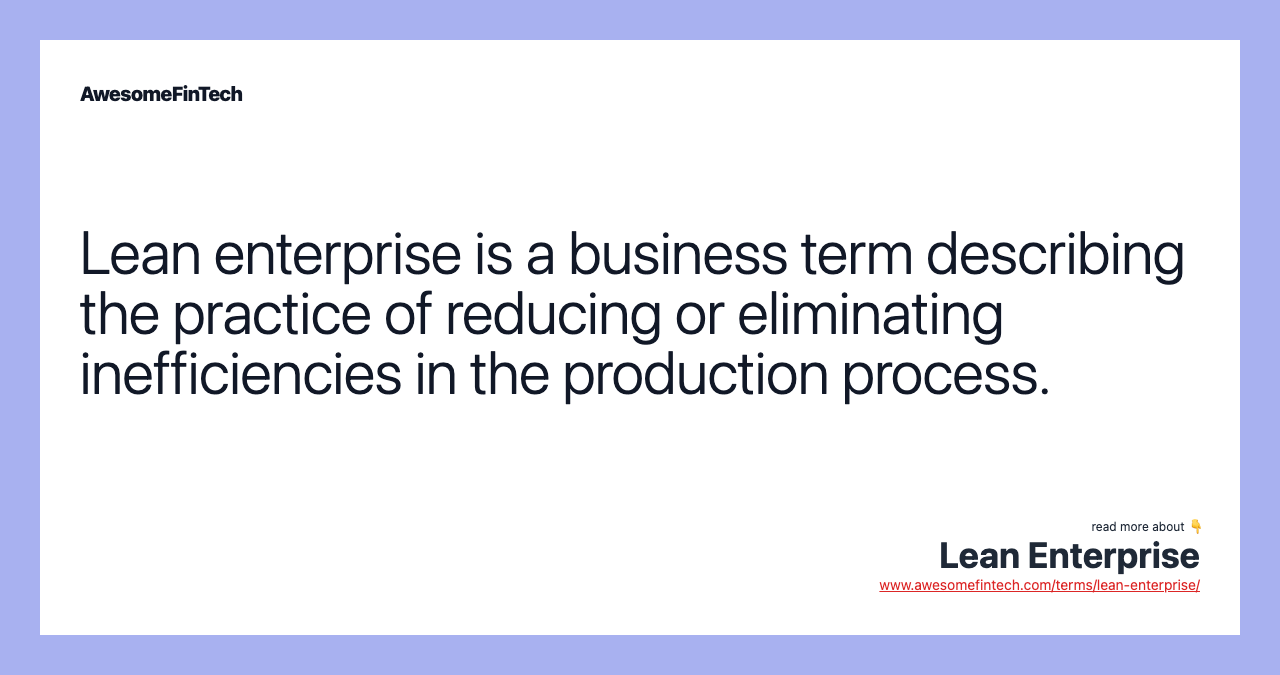
What Is Lean Enterprise?
Lean enterprise refers to a production principle stating that any component of a business enterprise that fails to directly benefit a final product is superfluous. Lean enterprise focuses on value creation while eliminating waste and non-essential processes.
The most valuable elements of a product or a service are largely decided by consumers, based on the discretionary income they are willing to pay for an item.
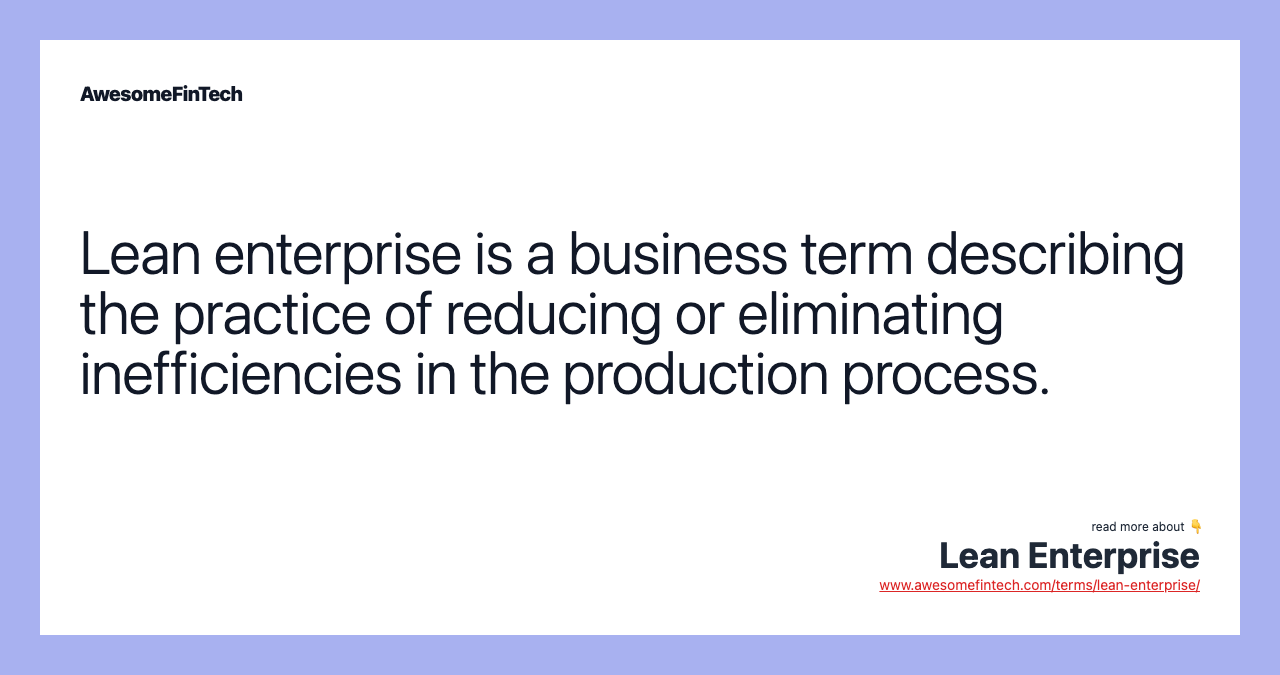
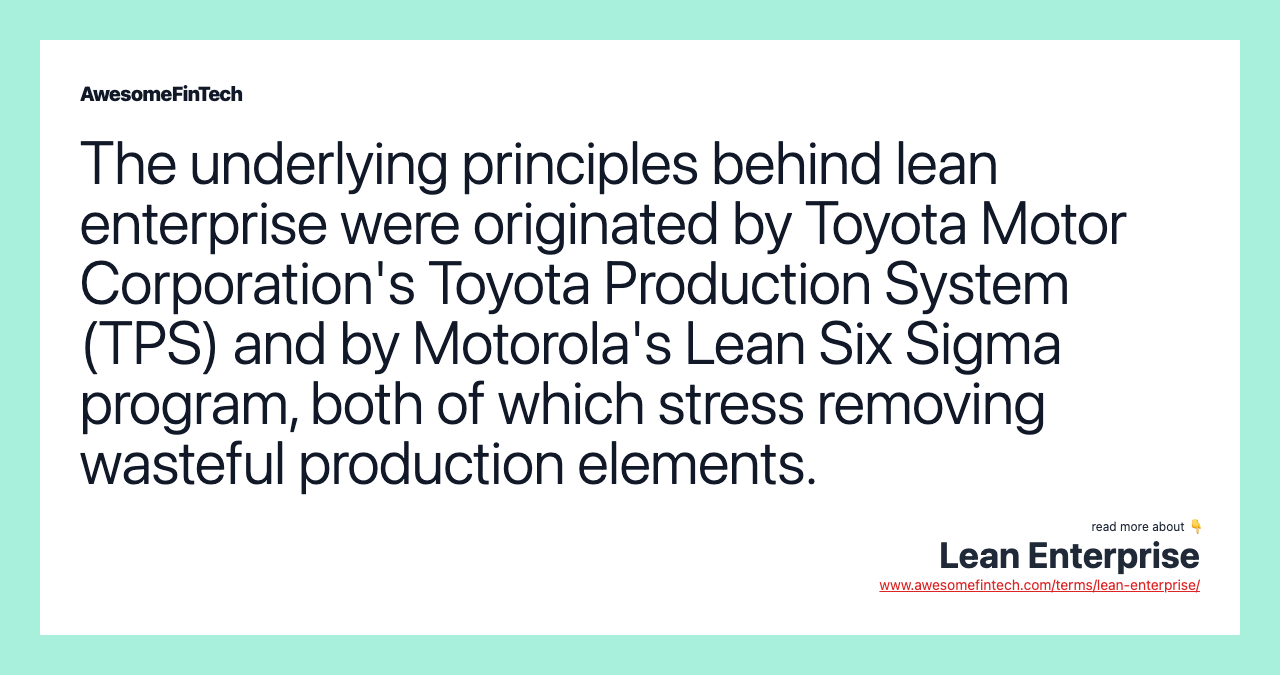
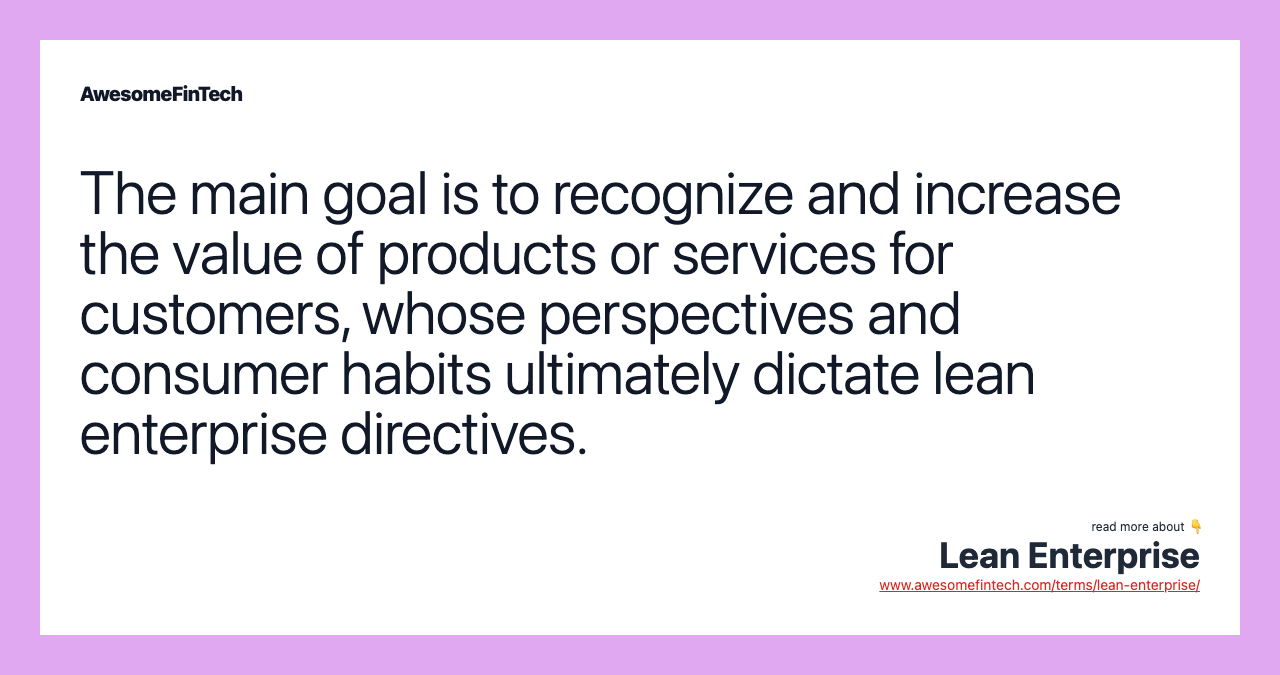
Understanding Lean Enterprise
Lean enterprise is sometimes simply referred to as "lean." Although both terms came into popular usage in the 1990s, the concept itself was devised by Toyota Motor Corporation when it introduced the Toyota Production System (TPS).
Developed by Eiji Toyoda and Taiichi Ohno, the Toyota Production System (TPS) integrated socio-technical management philosophy and was practiced between 1948 and 1975. The lean enterprise philosophy was also inspired by telecommunications giant Motorola, which implemented a manufacturing principle known as Lean Six Sigma in 1986.
This quality-control methodology uses a data-driven review to limit mistakes and defects in the production process. At its core, a company that adopts lean enterprise combines these two disciplines in order to maximize value for customers while slashing the money and resources spent on creating the products and services in question.
Lean Enterprise Principles
According to Lean Thinking: Banish Waste and Create Wealth in Your Corporation, co-written by economists James Womack and Daniel T. Jones, lean enterprise is characterized by the following five chief tenets:
Lean Enterprise and Lean Six Sigma
By heavily borrowing ideals from Lean Six Sigma principles, lean enterprise seeks to eliminate "muda," a Japanese term that roughly translates to "waste" and refers to the inefficiencies that can be radically reduced or jettisoned.
Specifically, the following eight discrete categories comprise muda, easily memorized by the acronym "DOWNTIME," for Defects, Overproduction, Waiting, Non-Utilized Talent, Transportation, Inventory, Motion, Extra-Processing.
Related terms:
Accounting
Accounting is the process of recording, summarizing, analyzing, and reporting financial transactions of a business to oversight agencies, regulators, and the IRS. read more
Just in Time (JIT) Inventory
A just-in-time (JIT) inventory system is a management strategy that aligns raw-material orders from suppliers directly with production schedules. read more
Lean Six Sigma
Lean Six Sigma is a team-focused managerial approach that seeks to improve performance by eliminating waste and defects. read more
PDCA Cycle
The PDCA Cycle, which stands for Plan-Do-Check-Act, is a problem-solving iterative technique that uses four steps to improve business processes. read more
Product Life Cycle
Every product has a life cycle, and reevaluating it at each phase is considered important to managing its commercial success. read more
Productivity
Productivity measures the efficiency of production in macroeconomics. Read about productivity in the workplace and how productivity impacts investments. read more
Quality Control & Example
Quality control is a process by which a business ensures that product quality is maintained or improved. Discover what quality control is and how it works. read more