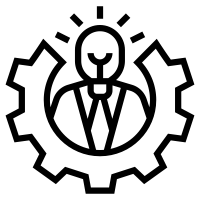
Capacity Management
Capacity management refers to the act of ensuring a business maximizes its potential activities and production output — at all times, under all conditions. Since capacity can change due to changing conditions or external influences — including seasonal demand, industry changes, and unexpected macroeconomic events — companies must remain nimble enough to constantly meet expectations in a cost-effective manner. Companies that poorly execute capacity management may experience diminished revenues due to unfulfilled orders, customer attrition, and decreased market share. Companies that poorly execute capacity management may experience diminished revenues due to unfulfilled orders, customer attrition, and decreased market share. Capacity management refers to the act of ensuring a business maximizes its potential activities and production output — at all times, under all conditions.
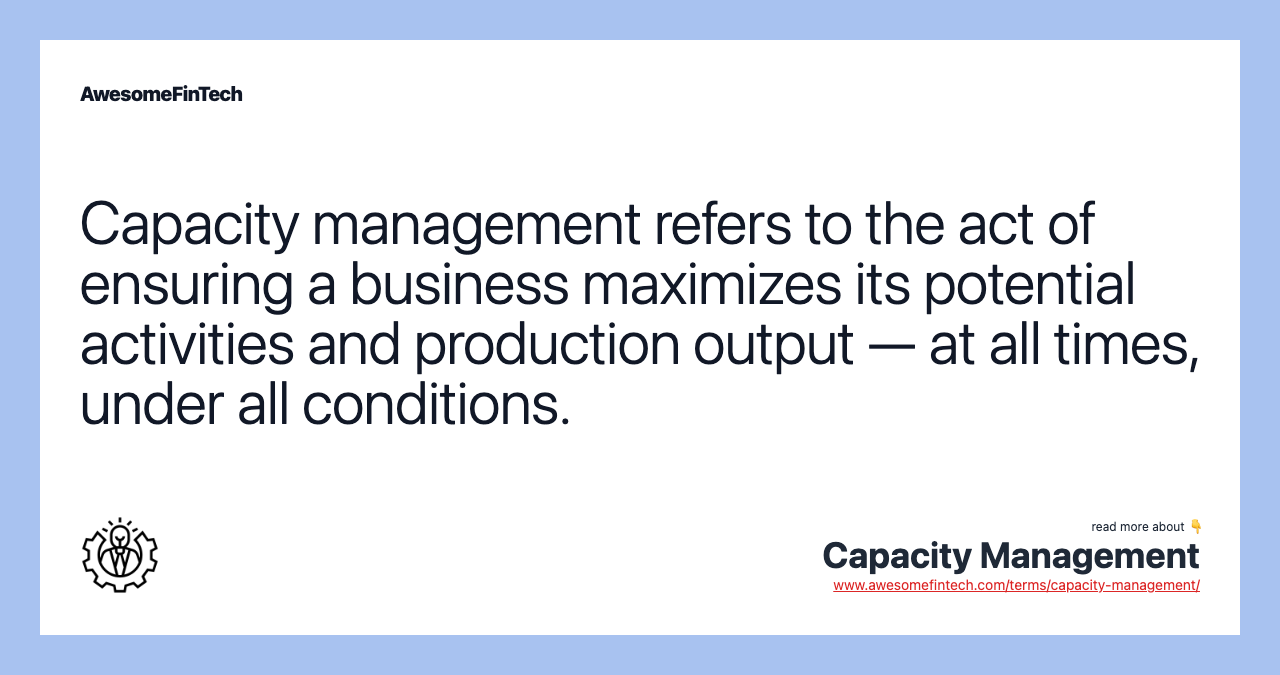
What Is Capacity Management?
Capacity management refers to the act of ensuring a business maximizes its potential activities and production output — at all times, under all conditions. The capacity of a business measures how much companies can achieve, produce, or sell within a given time period. Consider the following examples:
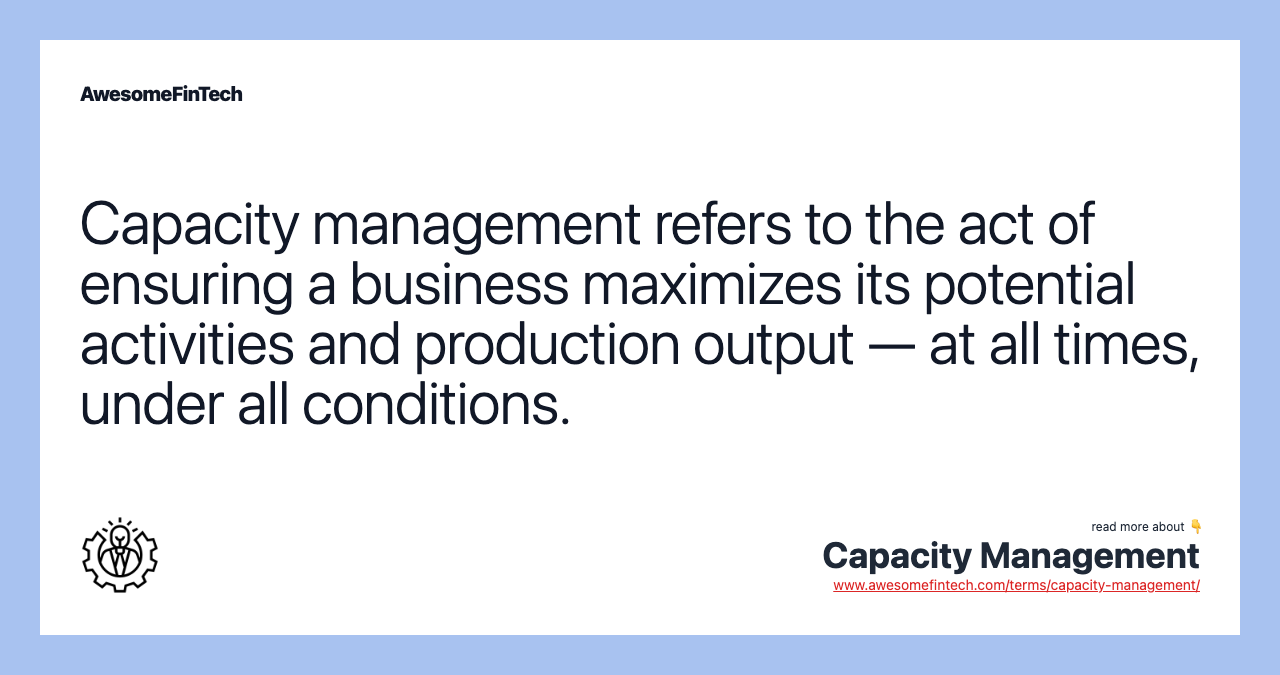
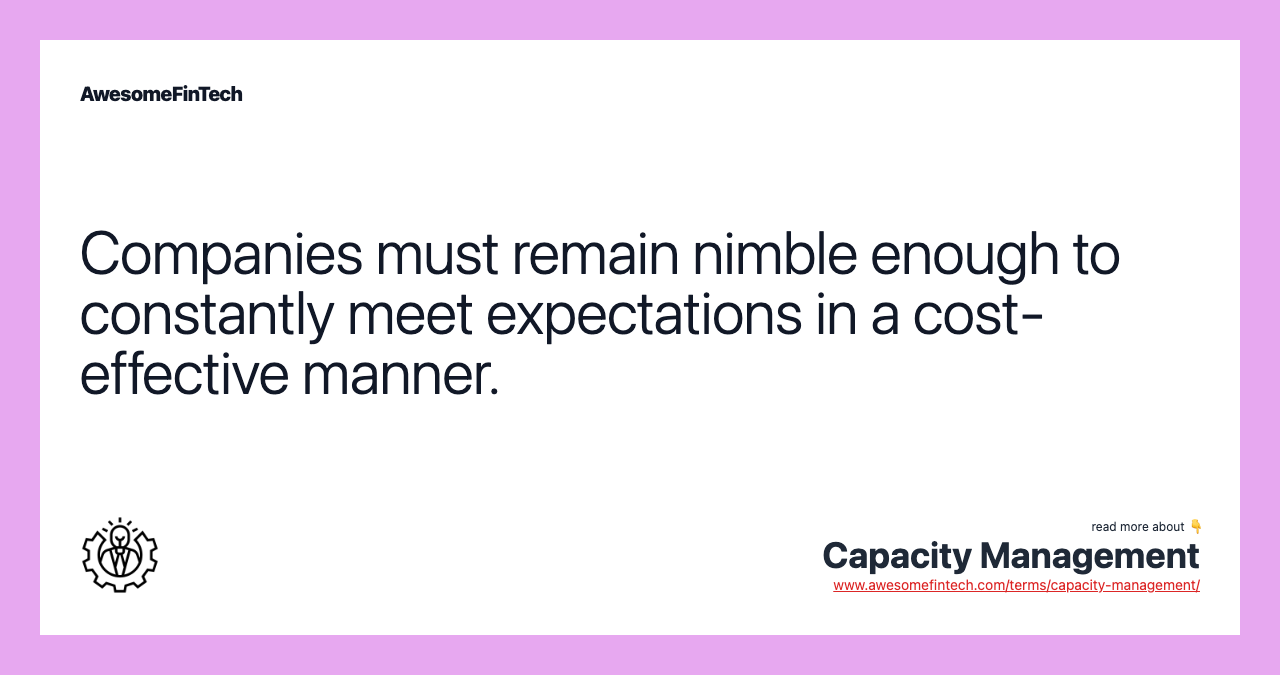
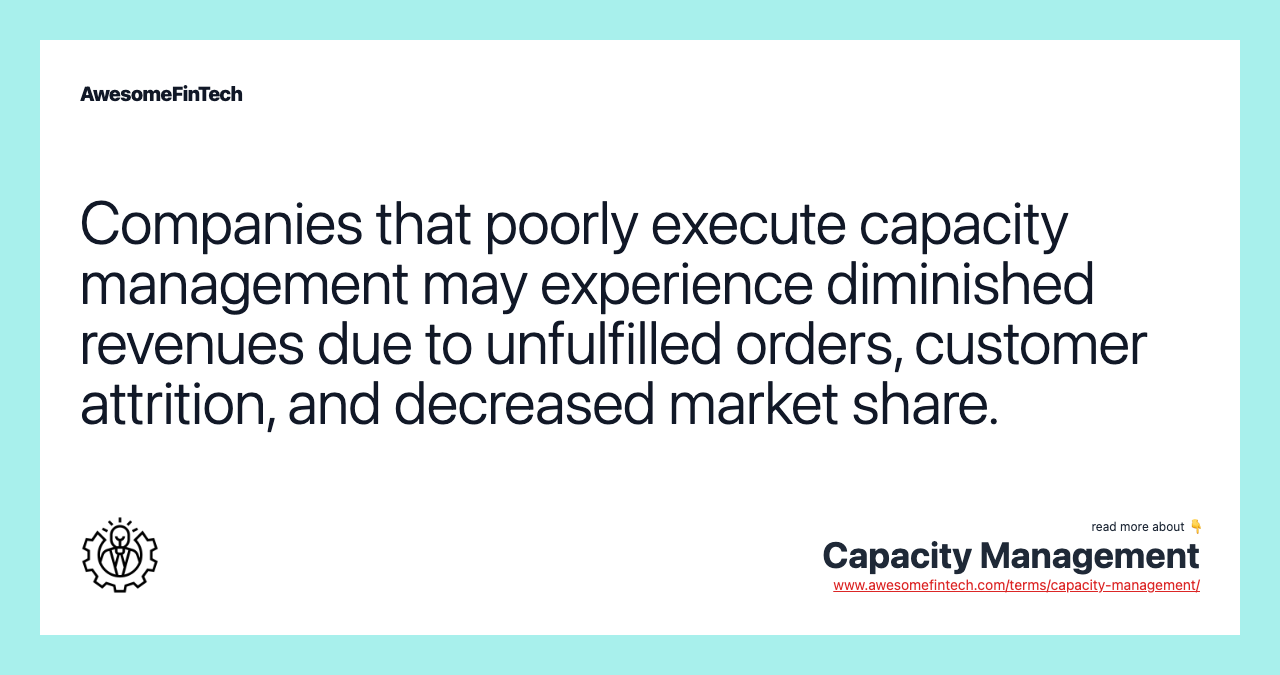
Understanding Capacity Management
Since capacity can change due to changing conditions or external influences — including seasonal demand, industry changes, and unexpected macroeconomic events — companies must remain nimble enough to constantly meet expectations in a cost-effective manner. For example, raw material resources may need to be adjusted, depending on demand and the business's current on-hand inventory.
Implementing capacity management may entail working overtime, outsourcing business operations, purchasing additional equipment, and leasing or selling commercial property.
Companies that poorly execute capacity management may experience diminished revenues due to unfulfilled orders, customer attrition, and decreased market share. As such, a company that rolls out an innovative new product with an aggressive marketing campaign must commensurately plan for a sudden spike in demand. The inability to replenish a retail partner's inventory in a timely manner is bad for business.
Businesses thus face inherent challenges in their attempts to produce at capacity while minimizing production costs. For instance, a company may lack the requisite time and personnel needed to conduct adequate quality control inspections on its products or services. Furthermore, machinery might break down due to overuse and employees may suffer stress, fatigue, and diminished morale if pushed too hard.
Capacity management is of particular concern to large companies because it's relatively easy to purchase additional hardware for smaller organizations at a low cost; however, when a business grows, adding new software becomes exponentially more expensive. Thus capacity management must take into account several different aspects related to growth and production costs.
Space Management
Capacity management also means calculating the proportion of spacial capacity that is actually being used over a certain time period. Consider a company operating at a maximum capacity that houses 500 employees across three floors of an office building. If that company downsizes by reducing the number of employees to 300, it will then be operating at 60% capacity (300 / 500 = 60%). But given that 40% of its office space is left unused, the firm is spending more on per-unit cost than before.
Consequently, the company might decide to allocate its labor resources to only two floors and cease leasing the unused floor in a proactive effort to reduce expenditures on rent, insurance, and utility costs associated with the empty space.
Related terms:
Attrition
Attrition is the gradual but deliberate reduction in staff as employees retire or resign and are not replaced. read more
Branch Manager
A branch manager is an executive who is in charge of the branch office of a bank or financial institution. read more
What Is Commercial Property?
Commercial property is buildings and land that are intended for profit-generating activities rather than regular residential purposes. read more
The Conference Board (CB)
The Conference Board (CB) is a not-for-profit research organization which distributes vital economic information to its peer-to-peer business members. read more
Downsizing
Downsizing is the permanent reduction of a company's labor force through the elimination of unproductive workers or divisions. read more
Factors of Production
Factors of production are the inputs needed for the creation of a good or service. The factors of production include land, labor, entrepreneurship, and capital. read more
Mergers and Acquisitions (M&A)
Mergers and acquisitions (M&A) refers to the consolidation of companies or assets through various types of financial transactions. read more
Operations Management (OM)
Operations management (OM) is the administration of business practices to create the highest level of efficiency possible within an organization. read more
Outsourcing
Outsourcing is a practice used by different companies to reduce costs by transferring portions of work to outside suppliers rather than completing it internally. read more
Quality Control & Example
Quality control is a process by which a business ensures that product quality is maintained or improved. Discover what quality control is and how it works. read more