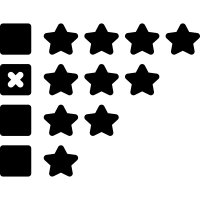
Absolute Performance Standard
The absolute performance standard is a theoretical benchmark for quality control. Having an absolute performance standard in place means companies have a way to measure their efficiency and performance. The company can find new training opportunities for those employees to boost their performance levels to meet the others based on the performance standards put in place. The absolute performance standard is a theoretical quality control benchmark, which ensures zero defects, error, and losses. The absolute performance standard is a good way for a company to measure its progress and efficiency.
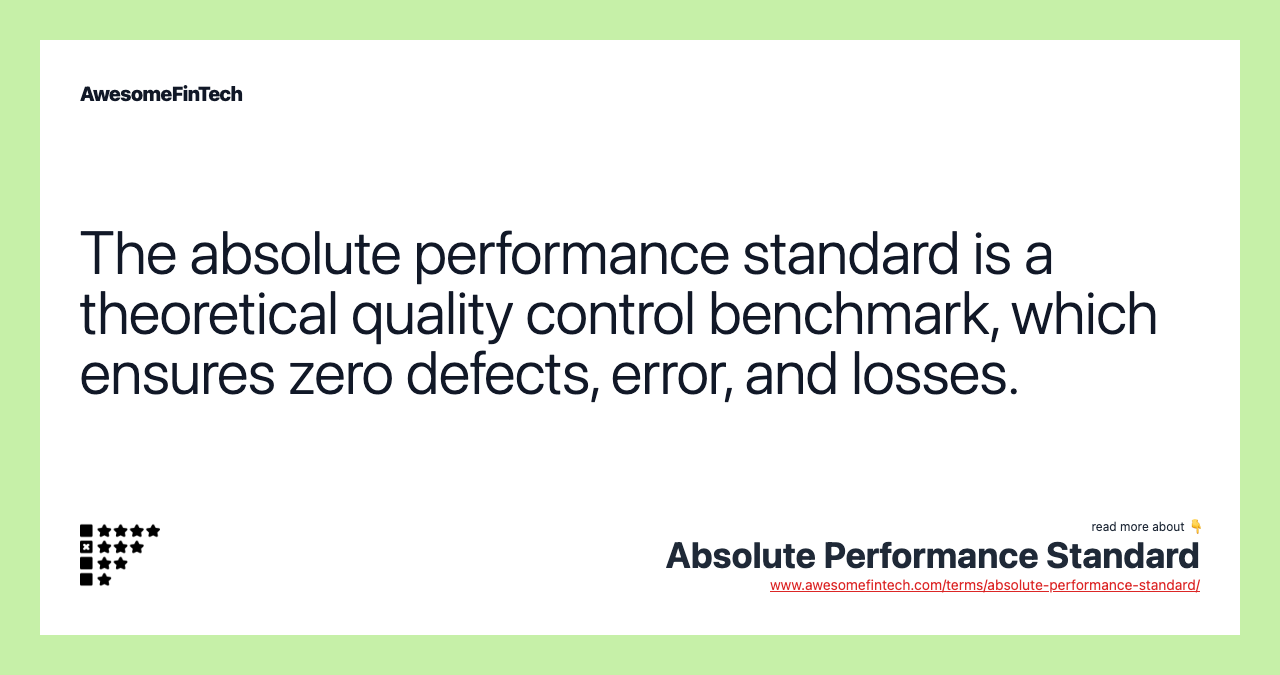
What Is Absolute Performance Standard?
The absolute performance standard is a theoretical benchmark for quality control. Although it is unattainable, it can be a good way to measure how well a business and its workers are doing. An organization can measure how far the business and its processes are falling from the mark of perfection the absolute performance standard represents.
Optimally, the business would move incrementally toward the absolute performance standard as it improves its processes. When used in this way, the absolute performance standard can measure an organization's progress, and how effective and efficient it is at running its business.
The absolute performance standard is a good way for a company to measure its progress and efficiency.
Performance standards, though, should be attainable, specific, observable, meaningful, measurable and stated in terms of quality, quantity, timeliness, or cost.
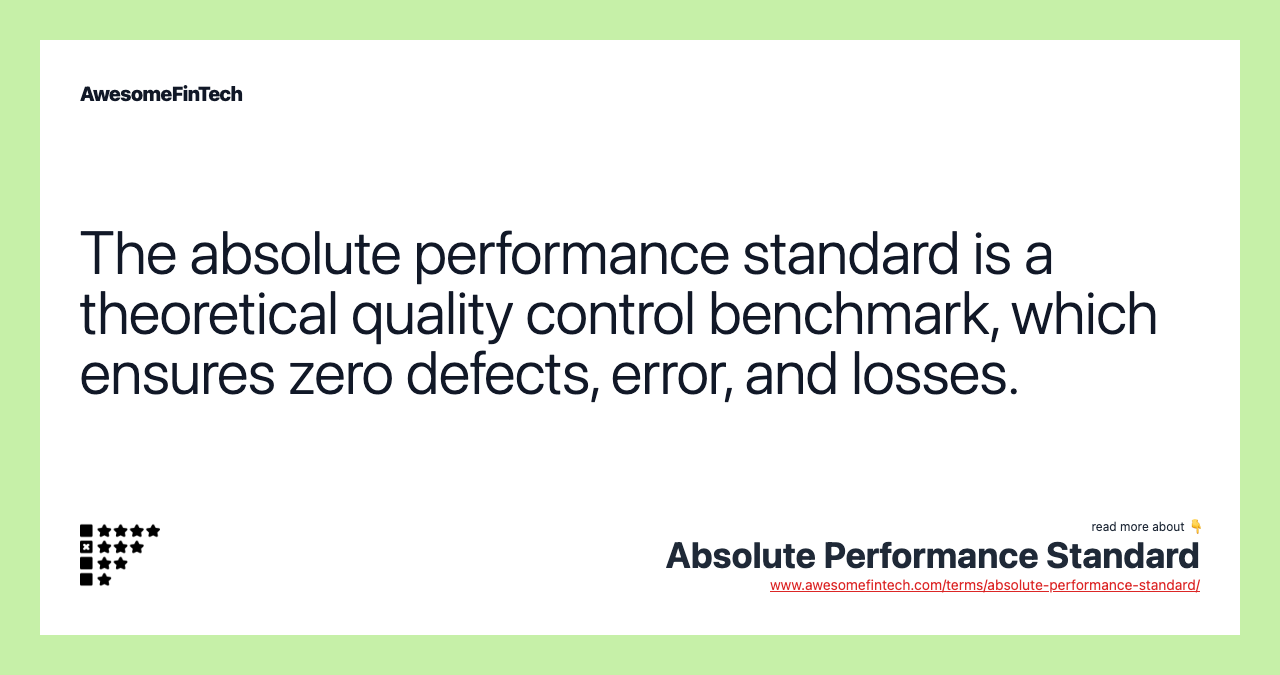
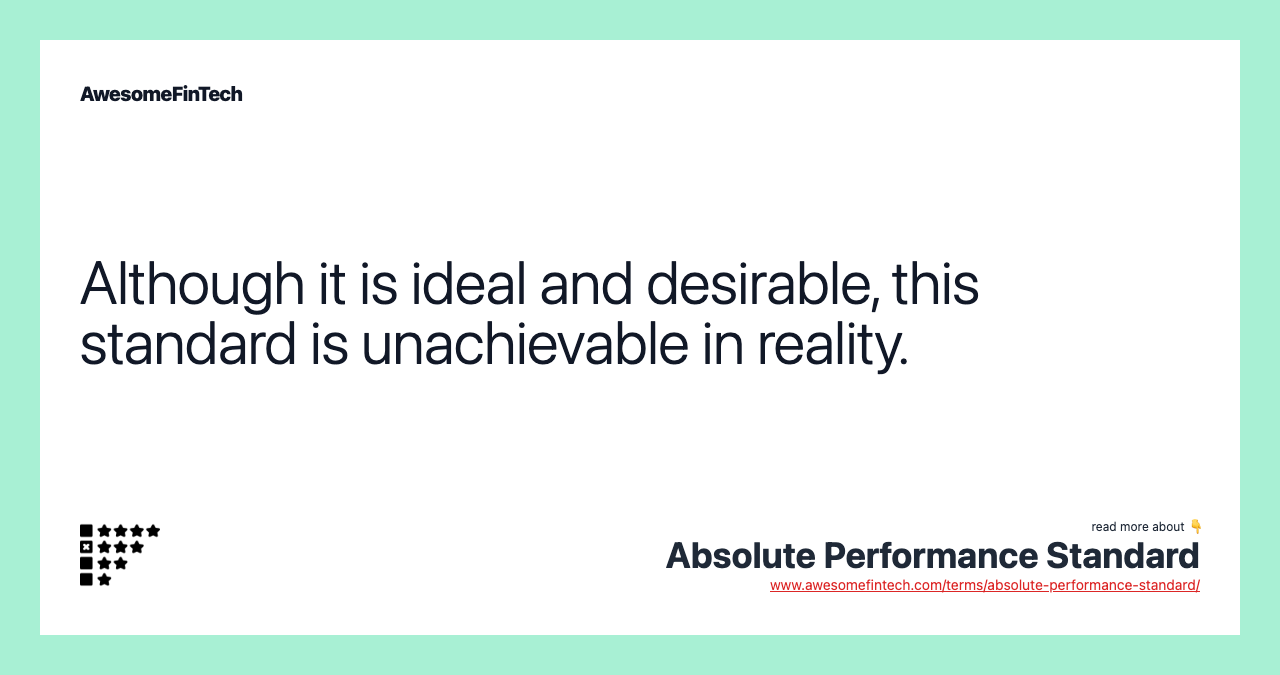
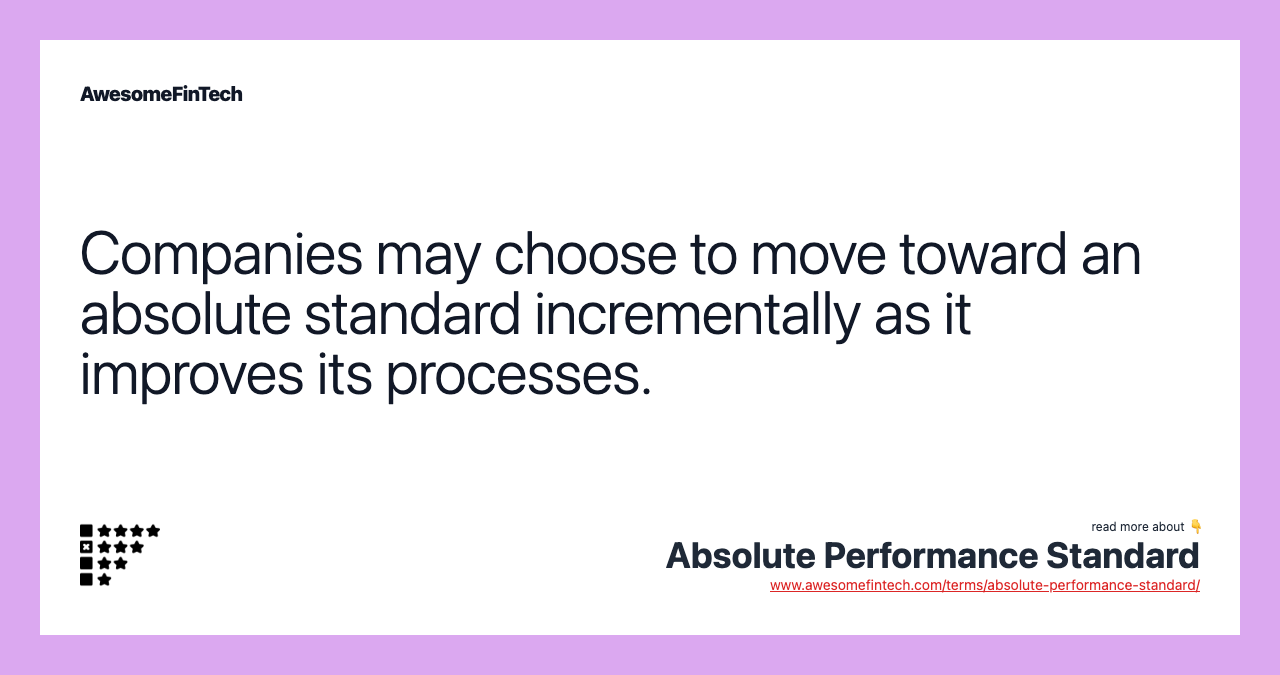
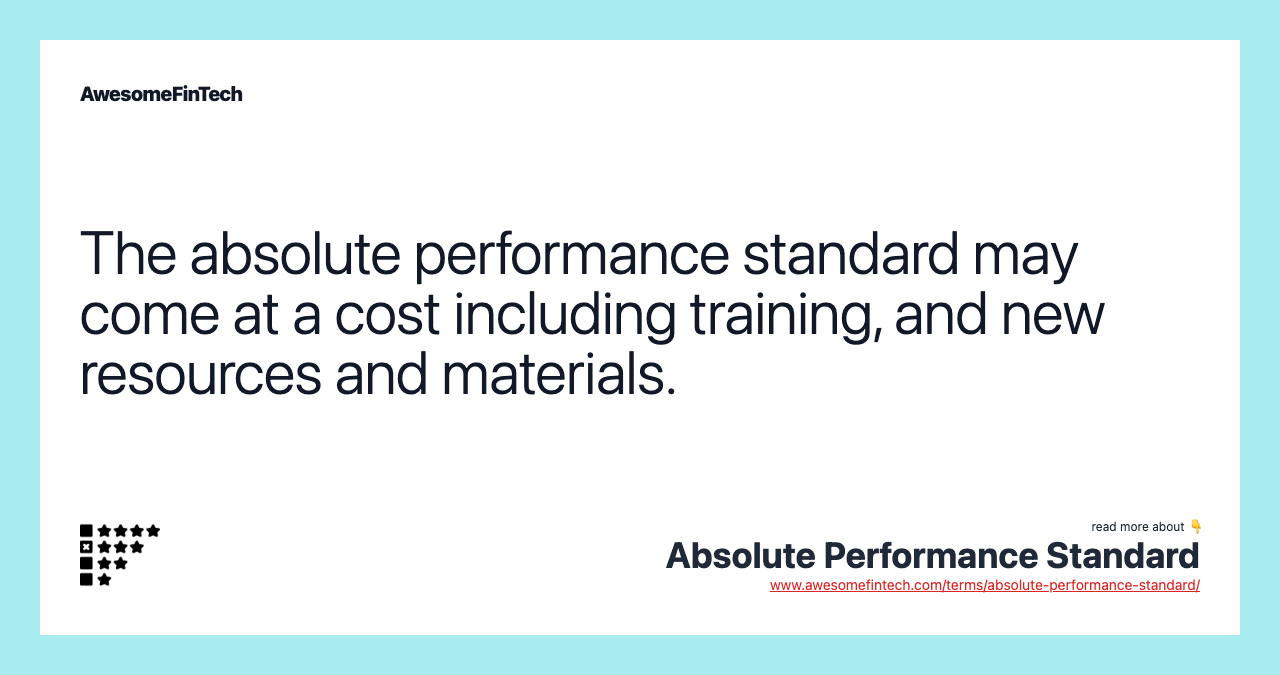
Understanding the Absolute Performance Standard
The absolute performance standard is a quality control concept companies adopt in order to improve their efficiency. Quality control is a business process that ensures there are no defects or errors in production and that product quality is consistent and/or improved. Because it relies on an absolutely perfect operation, the standard is both ideal and unattainable.
In order for a company to successfully adopt an absolute performance standard, there are a few steps it must take.
Having an absolute performance standard in place means companies have a way to measure their efficiency and performance. They can also find opportunities for improvement and how to implement these strategies. Say, for instance, a production team in a manufacturing company is comprised of 25 members, and only five employees are not meeting their goalsPerformance standards should be attainable, specific, observable, meaningful, measurable, and stated in terms of quality, quantity, timeliness, or cost. The company can find new training opportunities for those employees to boost their performance levels to meet the others based on the performance standards put in place.
Disadvantages of Absolute Performance Standard
As mentioned above, an absolute performance standard is great in theory but is impossible to achieve in reality. No individual or organization can execute a perfect operation with zero defects, errors, or losses. Even though it may be an ideal, there are some disadvantages when it comes to adopting a measure like this.
One consideration companies must keep in mind is what it would cost a company's labor pool. Because there are certain standards employees must live up to, the team may feel pressured to achieve its goals — especially if it involves pay incentives. This may have the reverse effect, and cause more errors in their performance.
Furthermore, implementing these standards requires a considerable investment of capital. Company heads may be required to budget for new training plans and may need to purchase new technologies, equipment, and machinery. Given how long it takes to implement new strategies, it's also a huge time commitment that both management and the employees must make.
Examples of Absolute Performance Standard
Many organizations implement different forms of performance standards that measure different parts of their business. One example is putting in a zero defects or losses goal for its team. For example, a manufacturer may implement a zero defects standard as part of its quality control to ensure the products it makes and ships to retailers are complete and without flaws.
The standard may also apply to bank branches which encourage employees to finish each quarter in the fiscal year with no losses. The employees may need to follow best practices to prevent cash shortages and losses from checks.
Other companies may implement a pay-for-performance incentive program. This is based on merit for workers who do well in their jobs.
Related terms:
Benchmark
A benchmark is a standard against which the performance of a security, mutual fund or investment manager can be measured. read more
Gross Domestic Product (GDP)
Gross domestic product (GDP) is the monetary value of all finished goods and services made within a country during a specific period. read more
Mergers and Acquisitions (M&A)
Mergers and acquisitions (M&A) refers to the consolidation of companies or assets through various types of financial transactions. read more
Pareto Analysis
Pareto analysis states that 80% of a project's results are due to 20% of the work, or conversely, 80% of problems can be traced to 20% of the causes. read more
PDCA Cycle
The PDCA Cycle, which stands for Plan-Do-Check-Act, is a problem-solving iterative technique that uses four steps to improve business processes. read more
Performance Management
Performance management is a corporate management tool that helps managers to monitor and evaluate employees' work. read more
Quality Control & Example
Quality control is a process by which a business ensures that product quality is maintained or improved. Discover what quality control is and how it works. read more
Quality of Earnings
A company's quality of earnings is revealed by dismissing anomalies, accounting tricks, or one-time events that may skew the numbers on real performance. read more