
Continuous Operations
Continuous operations are activities within a business or organization that are ongoing and sustained in the event of a business disruption. In the event of an interruption of operations (natural disaster or power outage, e.g.) or a looming serious threat that causes a temporary shutdown of an office or facility, a company can implement its continuous operations plan (also known as a business continuity plan). With relentless pressures on cost containment to maintain profit margins, more manufacturing companies are migrating to continuous operations in production by consolidating facilities and running them in three eight-hour shifts instead of one or two. In April 2018, electric car company Tesla, Inc. (TSLA) announced it would move to continuous operations of its Model 3 to meet an increased production target of 6,000 cars a week. **Improved Quality Control:*Streamlined processes used in continuous operations means fewer stages to oversee, allowing companies to identify production issues quickly.
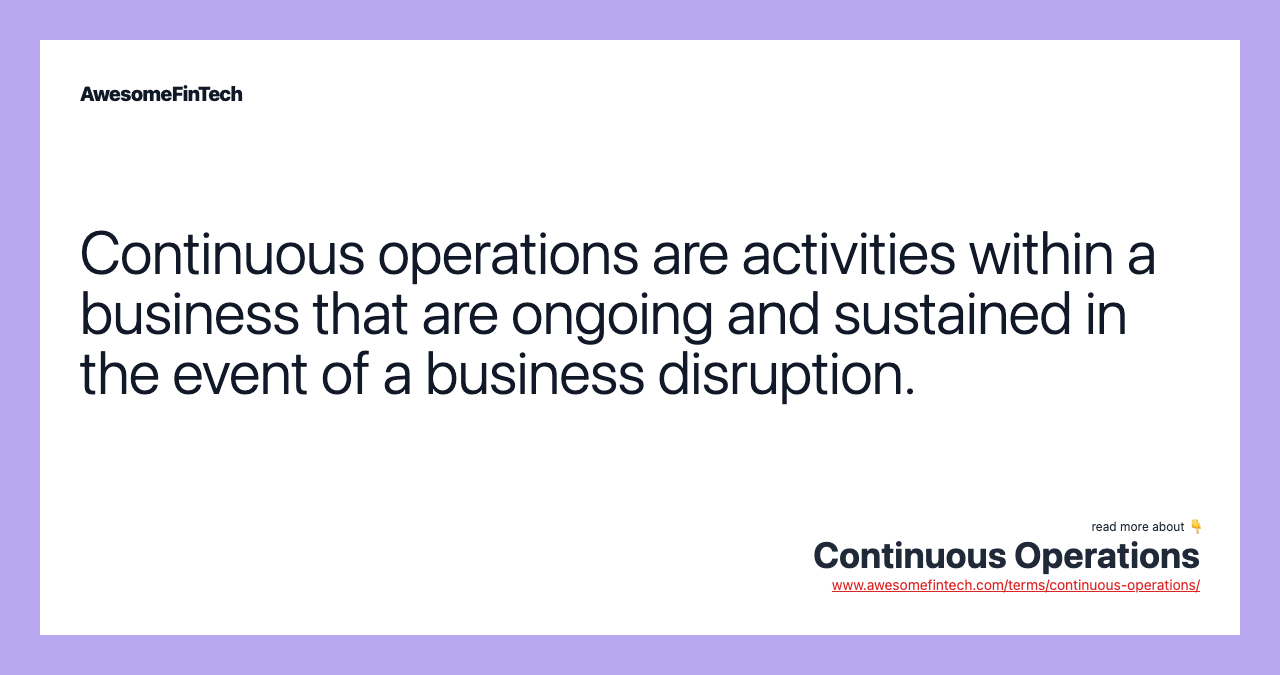
What Are Continuous Operations?
Continuous operations are activities within a business or organization that are ongoing and sustained in the event of a business disruption. Continuous operations also refers to a firm running its business around the clock, with downtime only for maintenance and repair in manufacturing facilities.
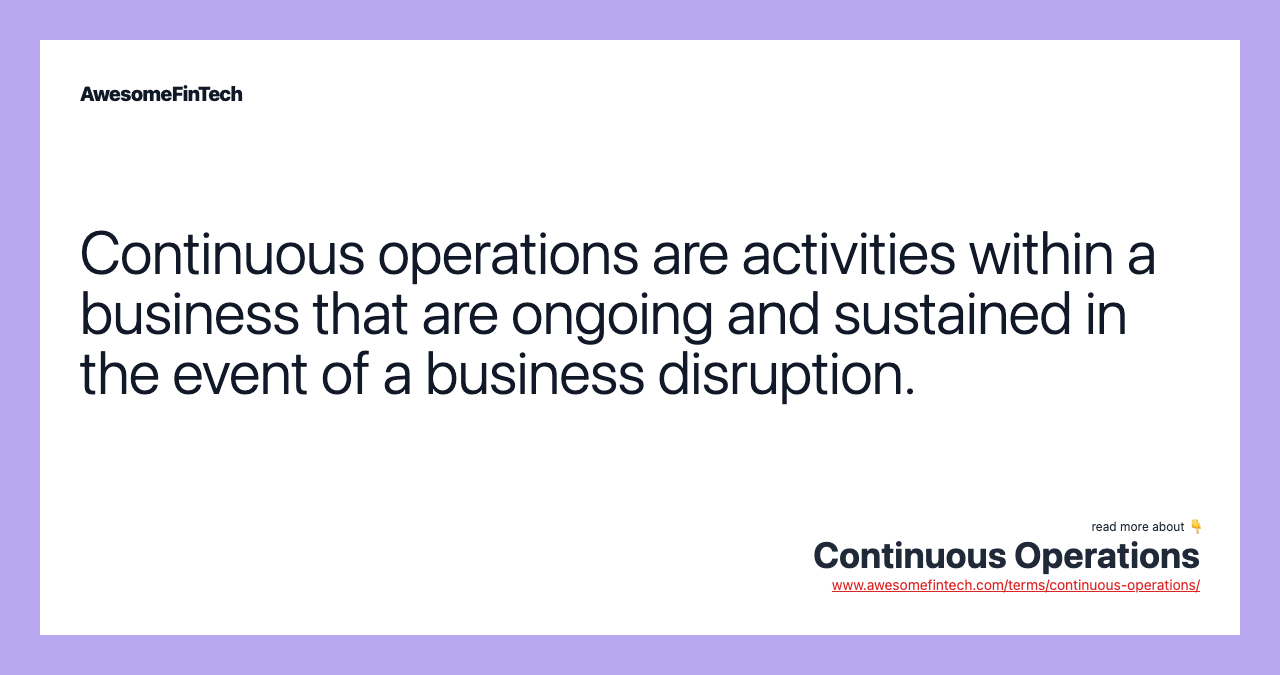
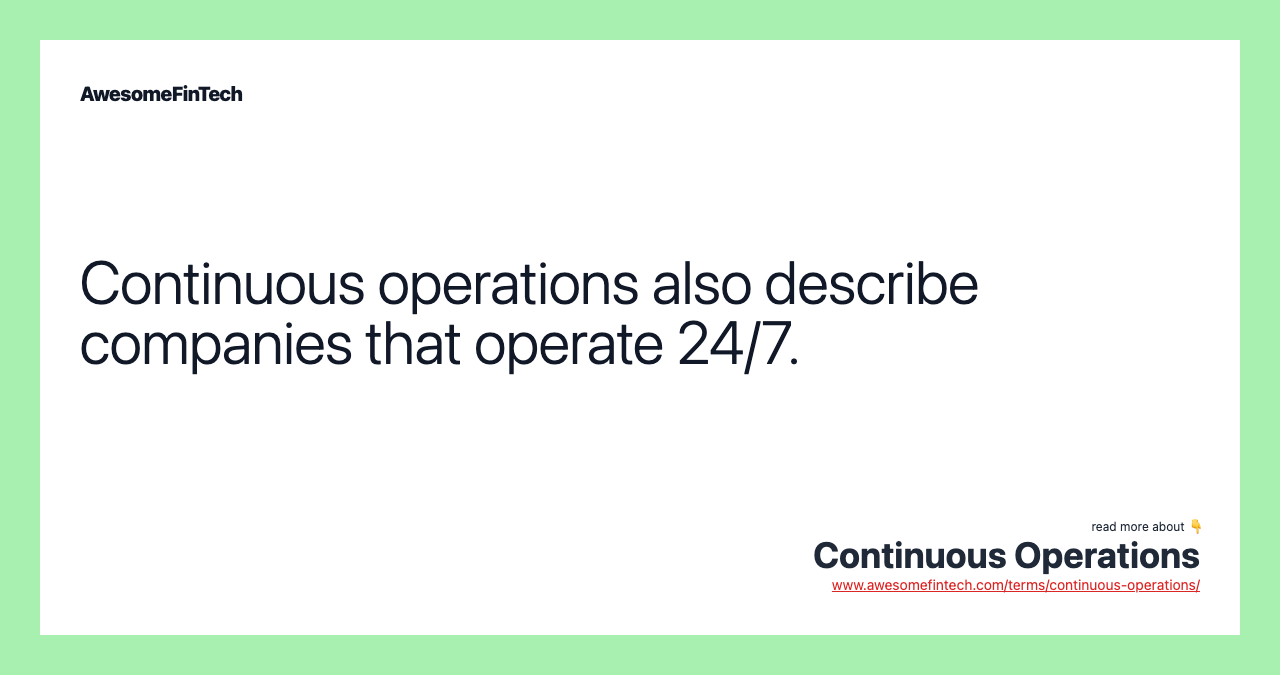
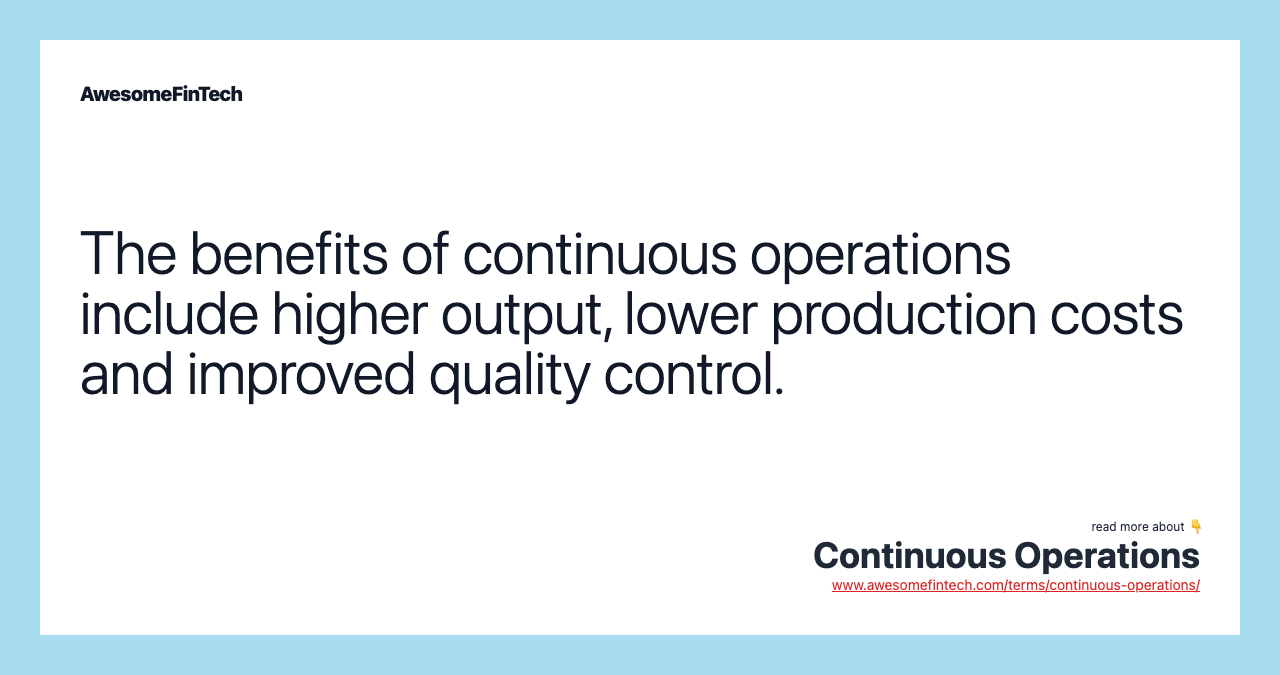
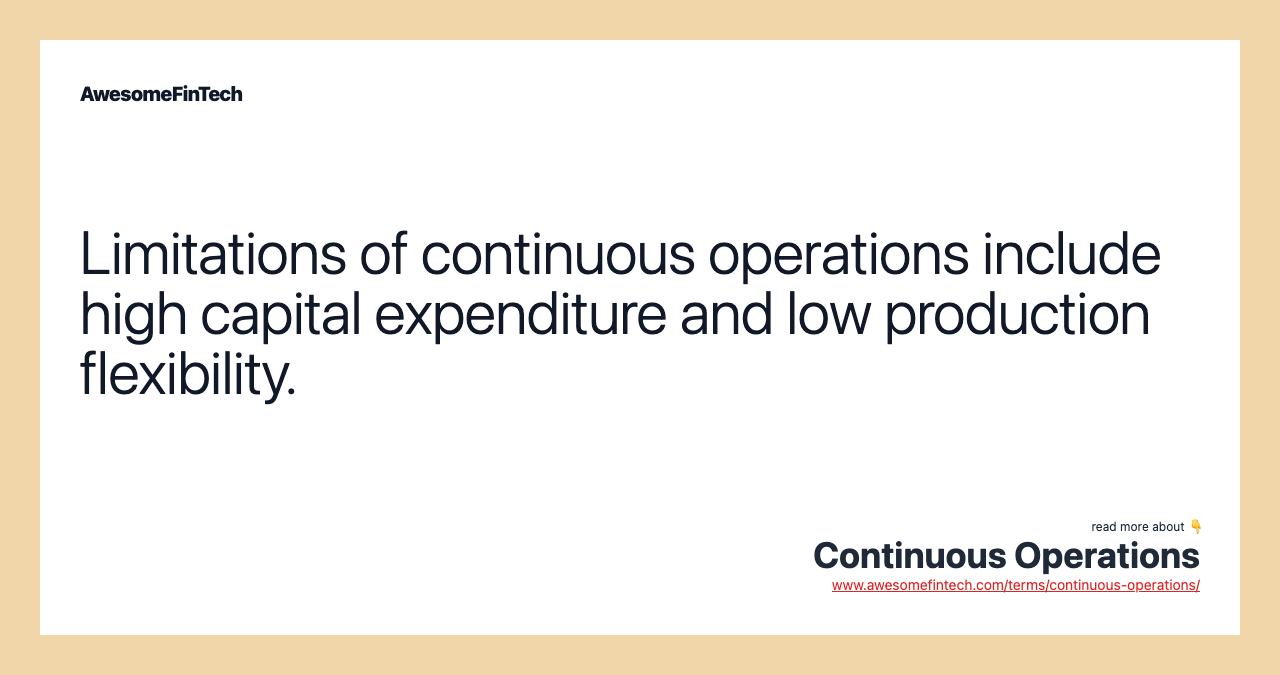
Understanding Continuous Operations
In the event of an interruption of operations (natural disaster or power outage, e.g.) or a looming serious threat that causes a temporary shutdown of an office or facility, a company can implement its continuous operations plan (also known as a business continuity plan). Typically, this generally involves deploying back-up technology systems, activating human resources in remote sites to carry out needed functions, or adding shifts at other manufacturing plants to make up for lost production.
For example, an aircraft parts manufacturer must shut down its operations in Florida due to a hurricane. The company adds a third shift at its plant in Texas to keep finished inventories constant. In the service industry, a bank whose trading systems suffer an outage in New York City quickly diverts customer orders to a back-up system in New Jersey, thus preserving continuous operations.
Round the Clock Operations
Continuous operations also apply to 24/7 business activities. This is common in industries where customers expect to be able to speak to a person live at any time of the day or night - an airline ticket holder, for example, or a credit card holder who wants to ask a question in the middle of the night.
With relentless pressures on cost containment to maintain profit margins, more manufacturing companies are migrating to continuous operations in production by consolidating facilities and running them in three eight-hour shifts instead of one or two. Food giant Nestle carried out this step in 2014 at a plant that makes frozen meals. In a statement, Nestle said, "Doing so provides the additional space we require for the continuous operations model."
Benefits of Continuous Operations
Higher Output: Higher volume becomes possible over a shorter duration due to continuous operations and eliminating unnecessary start-up and shutdown stages.
Lower Production Costs: Continuous operations encourage increased automation and the reduction of unnecessary labor, both of which lower the cost of production.
Improved Quality Control: Streamlined processes used in continuous operations means fewer stages to oversee, allowing companies to identify production issues quickly. Reduced manual production also reduces the potential for human error.
Limitations of Continuous Operations
Capital Intensive: Purchasing and installing the necessary equipment to run continuous operations requires a significant amount of capital. Companies must also train their employees the skills required to ensure 24/7 operations run smoothly which increases human resources costs.
Low Flexibility: Continuous operations establishes rigid production systems. A fault in one stage of the operation can disrupt, or halt, the entire process.
Example of Continuous Operations at Tesla
In April 2018, electric car company Tesla, Inc. (TSLA) announced it would move to continuous operations of its Model 3 to meet an increased production target of 6,000 cars a week. Founder and CEO Elon Musk said the company’s previous target of 5,000 cars provided no margin for error across Tesla’s manufacturing process and supply chain. To achieve its goal, the car maker upgraded its Fremont, California plant and made several changes to its automation processes to facilitate round the clock production.
Related terms:
Business Continuity Planning (BCP)
Business continuity planning (BCP) establishes protocols and creates prevention and recovery systems in case of a cyber-attack or natural disaster. read more
Data Analytics
Data analytics is the science of analyzing raw data in order to make conclusions about that information. read more
Inventory :
Inventory is the term for merchandise or raw materials that a company has on hand. read more
Manufacturing
Manufacturing is the processing of raw materials into finished goods using tools and processes. read more
Mergers and Acquisitions (M&A)
Mergers and acquisitions (M&A) refers to the consolidation of companies or assets through various types of financial transactions. read more
Mission Critical
A mission critical task or system is one whose failure or disruption would cause an entire operation or business to grind to a halt. read more
Production Rate
Production rate is the pace at which units of a product are manufactured within a scheduled time frame. Production rate can also refer to the amount of time it takes to produce one unit of a good. read more
Profit Margin
Profit margin gauges the degree to which a company or a business activity makes money. It represents what percentage of sales has turned into profits. read more
Supply Chain
A supply chain is a network of entities and people that work directly and indirectly to move a good or service from production to the final consumer. read more
Total Quality Management (TQM)
Total quality management (TQM) aims to hold all parties involved in the production process as accountable for the overall quality of the final product or service. read more