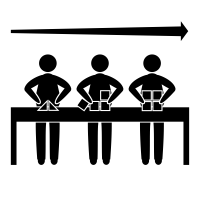
Assembly Line
An assembly line is a production process that breaks the manufacture of a good into steps that are completed in a pre-defined sequence. Assembly lines, on the other hand, have workers (or machines) complete a specific task on the product as it continues along the production line rather than complete a series of tasks. Companies use a design for assembly (DFA) approach to analyze a product and its design in order to determine assembly order and identify issues that can affect each task. This allows the company to manufacture a new product that has been designed with mass production in mind, with the tasks, task order, and assembly line layout already predetermined. An assembly line is a production process whereby the manufacture of a good is a sequence of steps completed in a pre-defined sequence.
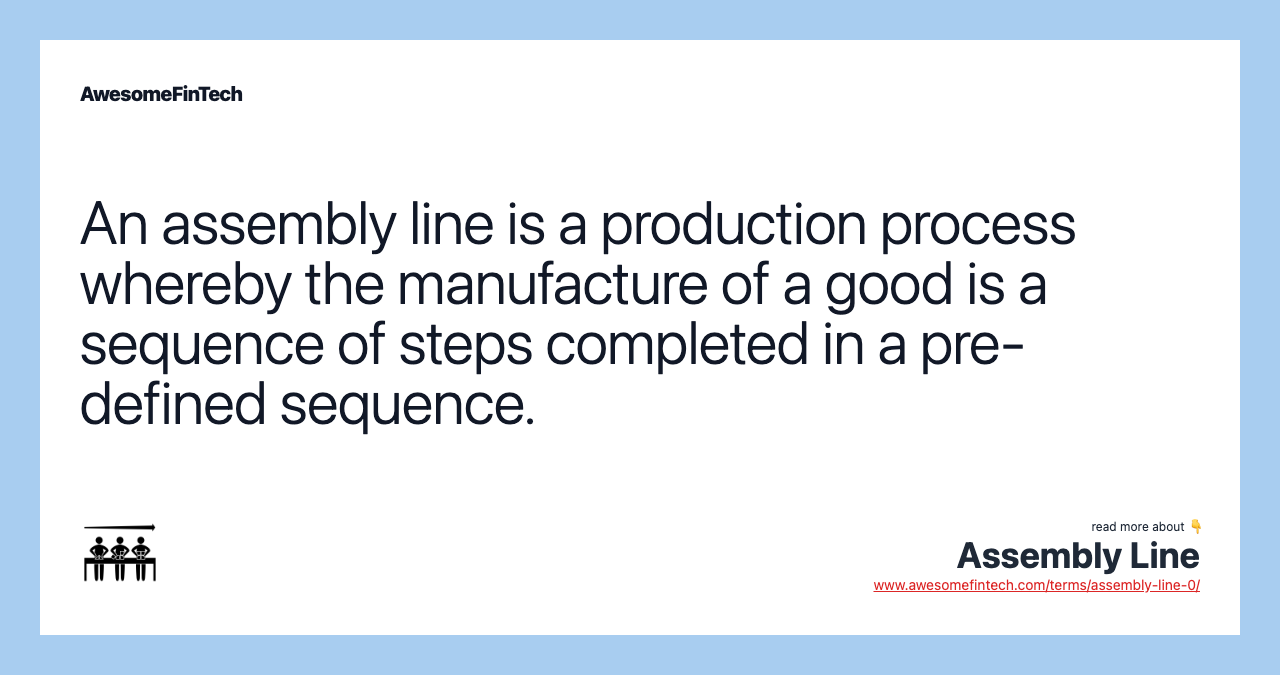
What Is an Assembly Line?
An assembly line is a production process that breaks the manufacture of a good into steps that are completed in a pre-defined sequence. Assembly lines are the most commonly used method in the mass production of products. They reduce labor costs because unskilled workers are trained to perform specific tasks. Rather than hire a skilled craftsperson to put together an entire piece of furniture or vehicle engine, companies hire workers only to add a leg to a stool or a bolt to a machine.
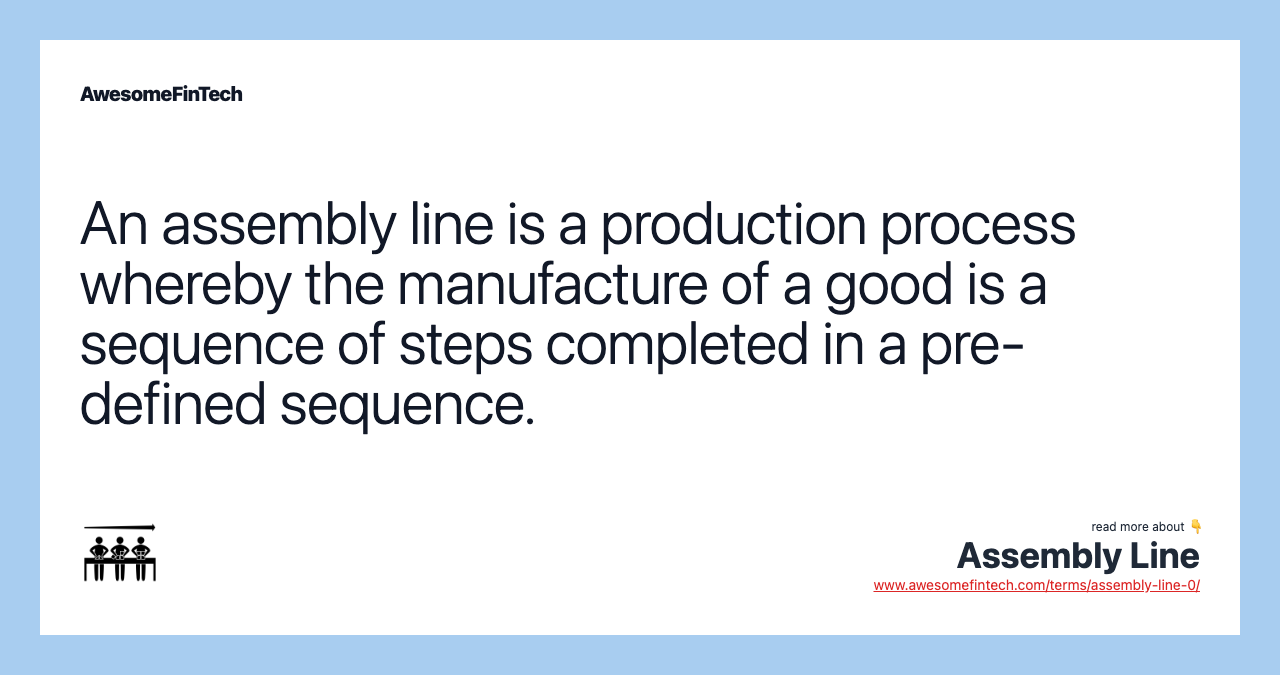
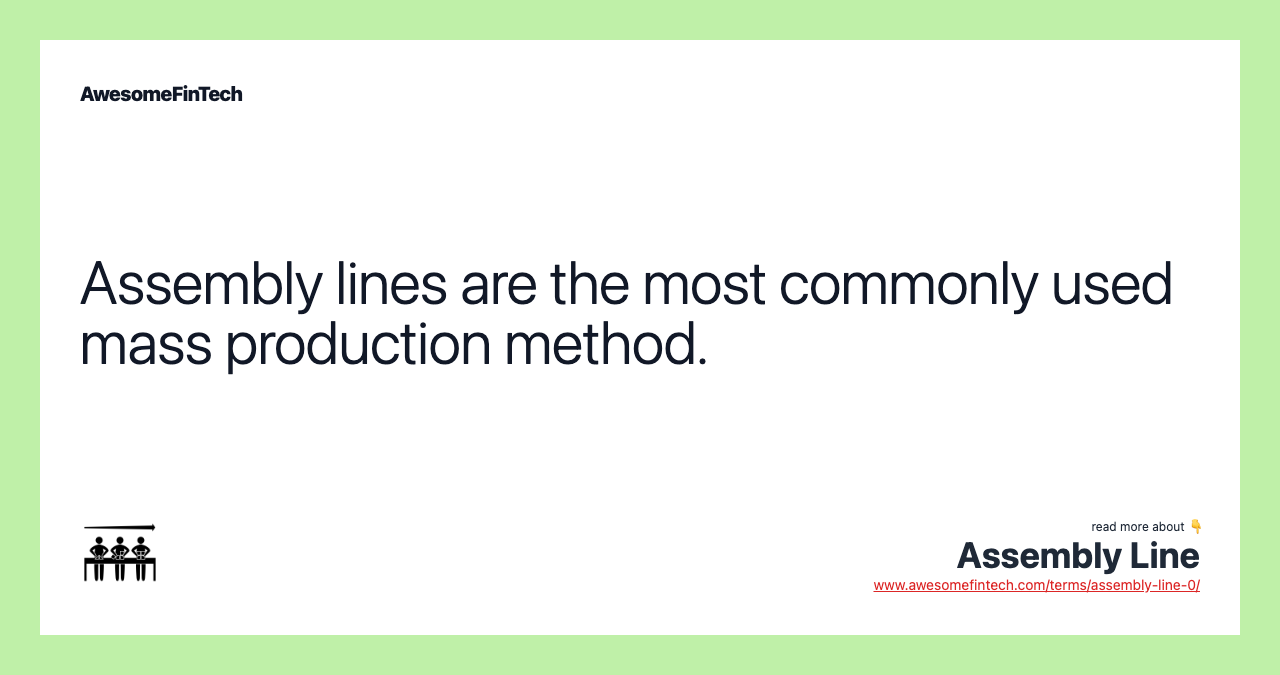
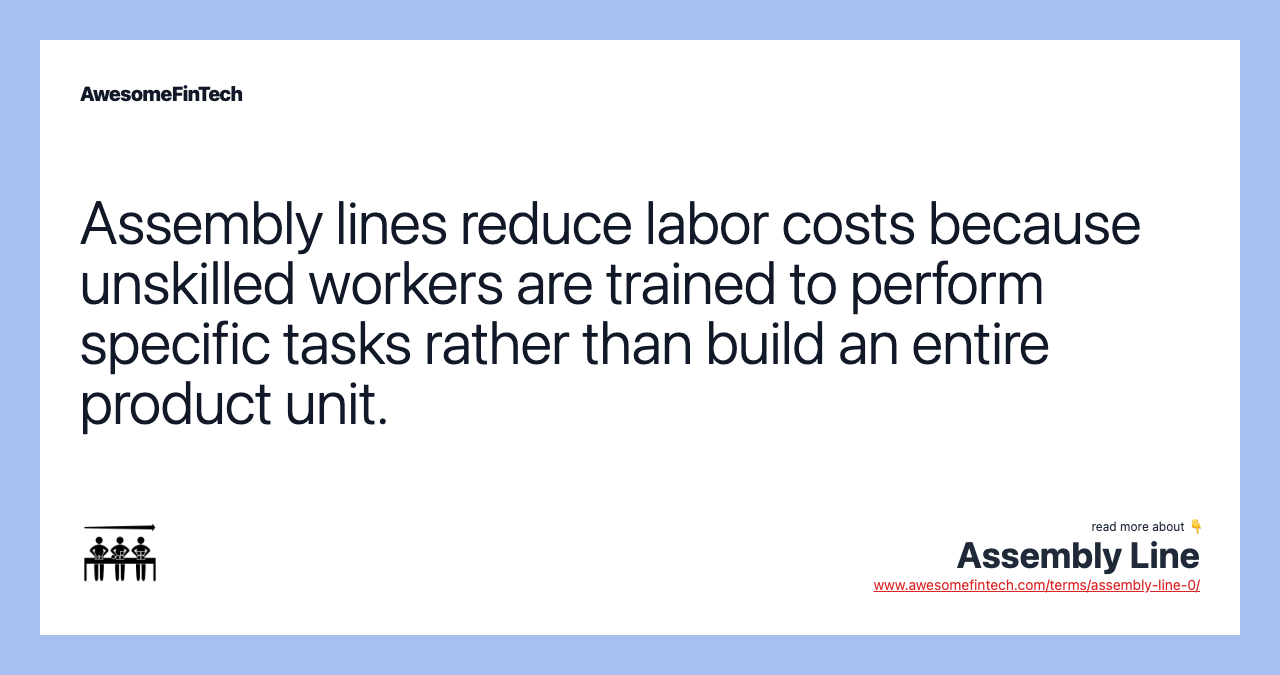
Understanding Assembly Lines
An assembly line is where semi-finished products move from workstation to workstation. Parts are added in sequence until the final assembly is produced. Today, automated assembly lines are by machines with minimal human supervision.
The introduction of the assembly line drastically changed the way goods were manufactured. Credit Henry Ford, who set up an assembly line in 1908 to manufacture his Model T cars. Before, workers would assemble a product (or a large part of it) in place, often with one worker completing all tasks associated with the product's creation.
Assembly lines, on the other hand, have workers (or machines) complete a specific task on the product as it continues along the production line rather than complete a series of tasks. This increases efficiency by maximizing the amount a worker could produce relative to the cost of labor.
Determining what individual tasks must be completed, when they need to be completed, and who will complete them is a crucial step in establishing an effective assembly line. Complicated products, such as cars, have to be broken down into components that machines and workers can quickly assemble.
Companies use a design for assembly (DFA) approach to analyze a product and its design in order to determine assembly order and identify issues that can affect each task. Each task is then categorized as either manual, robotic, or automatic, and is then assigned to individual stations along the manufacturing plant floor.
Special Considerations for Assembly Lines
Companies can also design products with their assembly in mind, referred to as concurrent engineering. This allows the company to manufacture a new product that has been designed with mass production in mind, with the tasks, task order, and assembly line layout already predetermined. This can significantly reduce the lead time between the initial product design release and the final product roll out.
Modern assembly lines combine digital technology with human input. New kinds of sensors and IIoT devices collect data from humans and machines in real time. Advanced robotics, collaborative automation, and more sophisticated software allow humans to work dynamically with machines on assembly lines.
Related terms:
Batch Processing
Batch processing is the processing transactions that are processed in a group or batch as opposed to individually. It applies to the computation of information or data. read more
Business Valuation , Methods, & Examples
Business valuation is the process of estimating the value of a business or company. read more
Factors of Production
Factors of production are the inputs needed for the creation of a good or service. The factors of production include land, labor, entrepreneurship, and capital. read more
Manufacturing
Manufacturing is the processing of raw materials into finished goods using tools and processes. read more
Mass Production
Mass production is the manufacturing of large quantities of standardized products, often using assembly lines or automated technology. read more
Production Rate
Production rate is the pace at which units of a product are manufactured within a scheduled time frame. Production rate can also refer to the amount of time it takes to produce one unit of a good. read more