
Three-Sigma Limits
Three-sigma limits is a statistical calculation where the data are within three standard deviations from a mean. Three-sigma limits (3-sigma limits) is a statistical calculation that refers to data within three standard deviations from a mean. The upper control limit (UCL) is set three-sigma levels above the mean, and the lower control limit (LCL) is set at three sigma levels below the mean. First, **calculate the mean of the observed data.*(8.4 + 8.5 + 9.1 + 9.3 + 9.4 + 9.5 + 9.7 + 9.7 + 9.9 + 9.9) / 10, which equals 93.4 / 10 = 9.34. 2. Second, **calculate the variance of the set.*Variance is the spread between data points and is calculated as the sum of the squares of the difference between each data point and the mean divided by the number of observations. Three-sigma limits are used to set the upper and lower control limits in statistical quality control charts.
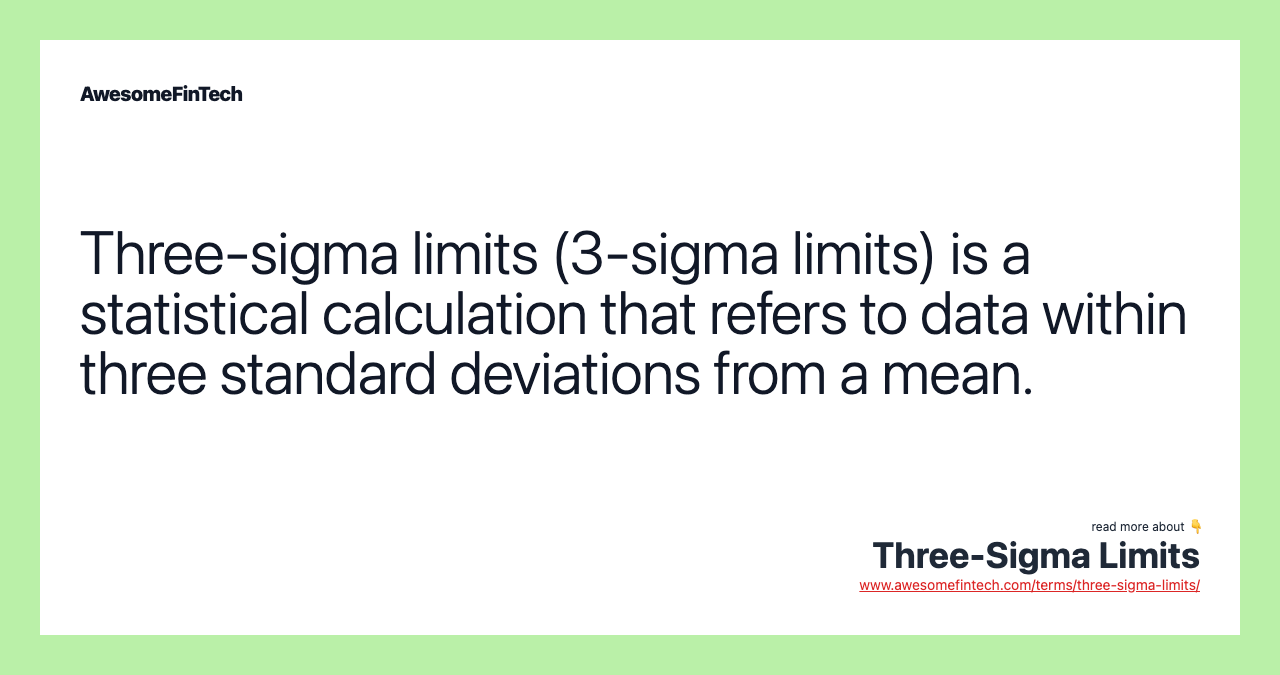
What Is a Three-Sigma Limit?
Three-sigma limits is a statistical calculation where the data are within three standard deviations from a mean. In business applications, three-sigma refers to processes that operate efficiently and produce items of the highest quality.
Three-sigma limits are used to set the upper and lower control limits in statistical quality control charts. Control charts are used to establish limits for a manufacturing or business process that is in a state of statistical control.
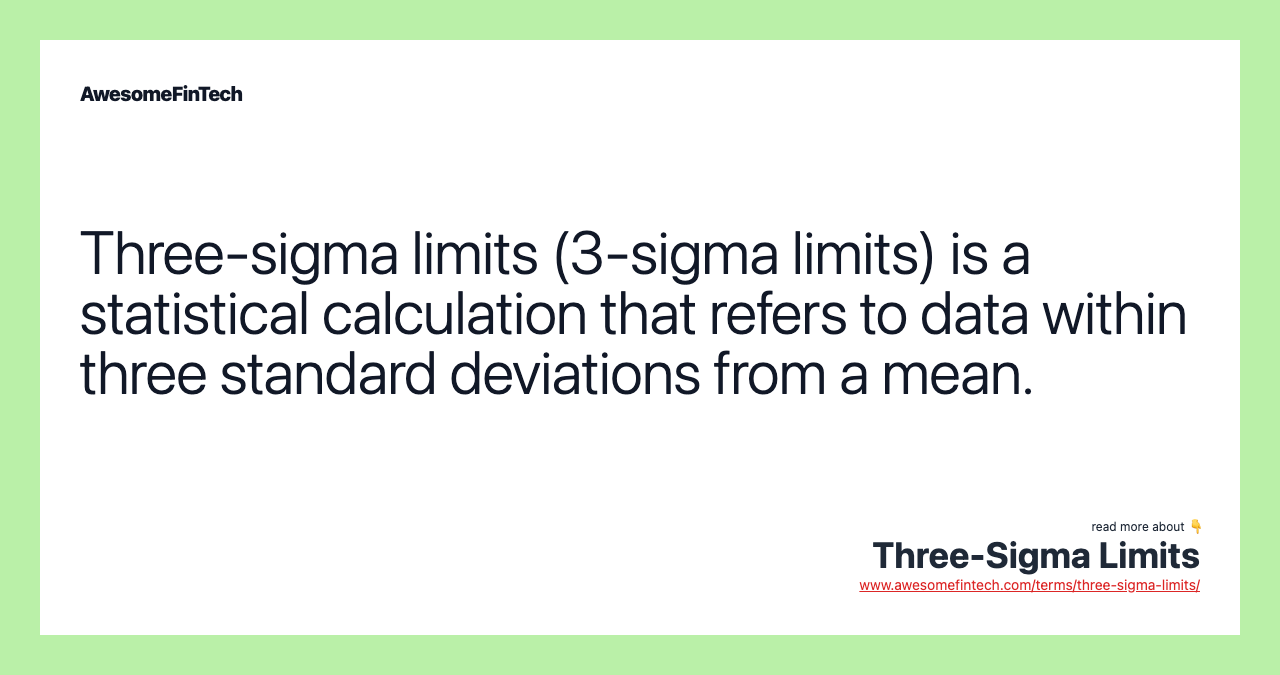
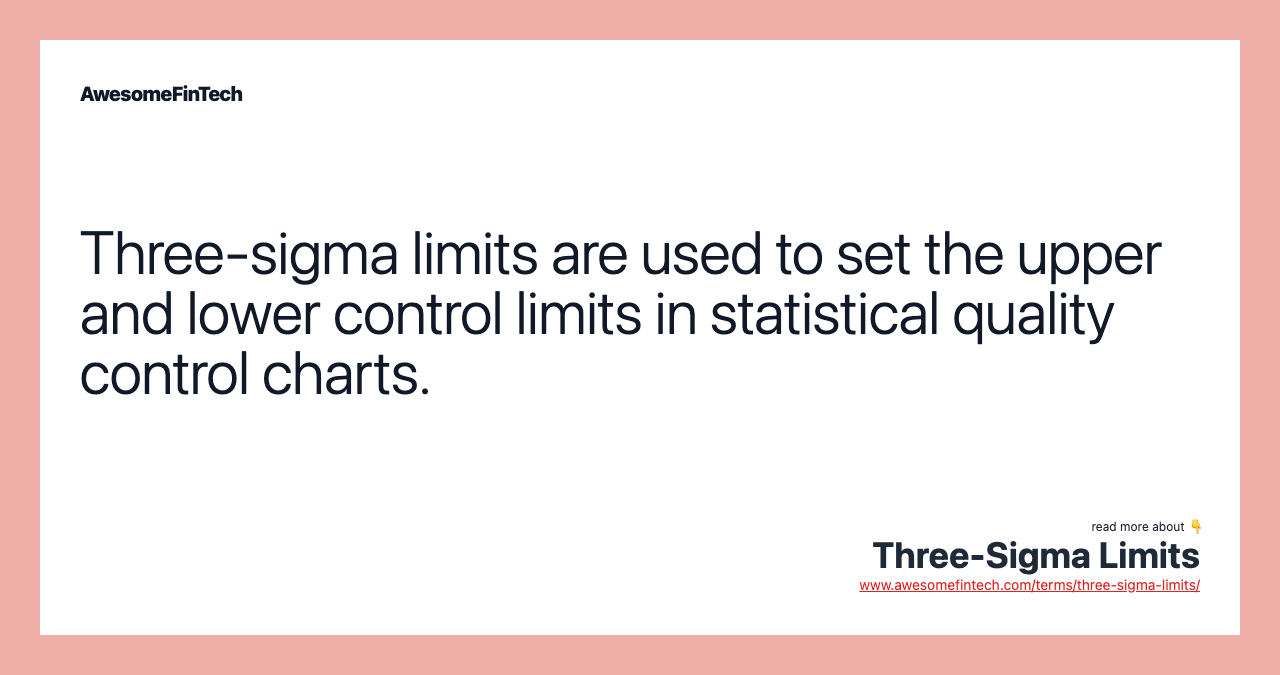
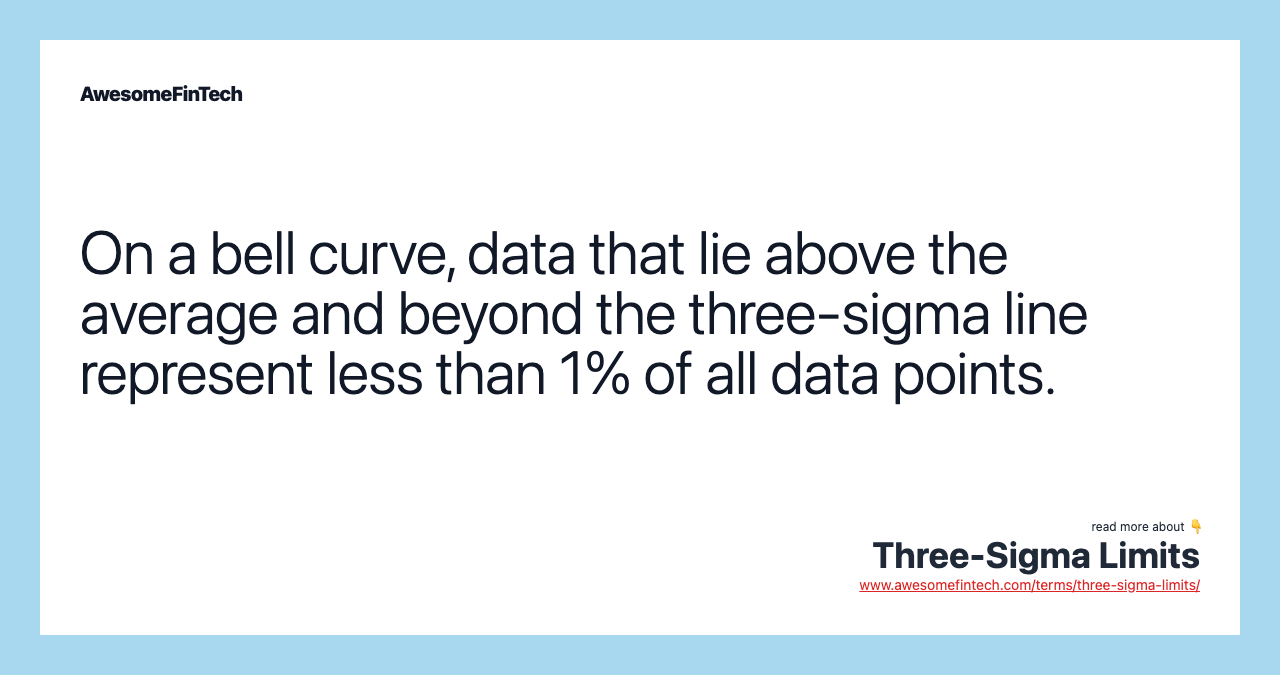
Understanding Three-Sigma Limits
Control charts are also known as Shewhart charts, named after Walter A. Shewhart, an American physicist, engineer, and statistician (1891–1967). Control charts are based on the theory that even in perfectly designed processes, a certain amount of variability in output measurements is inherent.
Control charts determine if there is a controlled or uncontrolled variation in a process. Variations in process quality due to random causes are said to be in-control; out-of-control processes include both random and special causes of variation. Control charts are intended to determine the presence of special causes.
To measure variations, statisticians and analysts use a metric known as the standard deviation, also called sigma. Sigma is a statistical measurement of variability, showing how much variation exists from a statistical average.
Sigma measures how far an observed data deviates from the mean or average; investors use standard deviation to gauge expected volatility, which is known as historical volatility.
To understand this measurement, consider the normal bell curve, which has a normal distribution. The farther to the right or left a data point is recorded on the bell curve, the higher or lower, respectively, the data is than the mean. From another point of view, low values indicate that the data points fall close to the mean; high values indicate the data is widespread and not close to the average.
An Example of Calculating Three-Sigma Limit
Let’s consider a manufacturing firm that runs a series of 10 tests to determine whether there is a variation in the quality of its products. The data points for the 10 tests are 8.4, 8.5, 9.1, 9.3, 9.4, 9.5, 9.7, 9.7, 9.9, and 9.9.
- First, calculate the mean of the observed data. (8.4 + 8.5 + 9.1 + 9.3 + 9.4 + 9.5 + 9.7 + 9.7 + 9.9 + 9.9) / 10, which equals 93.4 / 10 = 9.34.
- Second, calculate the variance of the set. Variance is the spread between data points and is calculated as the sum of the squares of the difference between each data point and the mean divided by the number of observations. The first difference square will be calculated as (8.4 - 9.34)2 = 0.8836, the second square of difference will be (8.5 - 9.34)2 = 0.7056, the third square can be calculated as (9.1 - 9.34)2 = 0.0576, and so on. The sum of the different squares of all 10 data points is 2.564. The variance is, therefore, 2.564 / 10 = 0.2564.
- Third, calculate the standard deviation, which is simply the square root of the variance. So, the standard deviation = √0.2564 = 0.5064.
- Fourth, calculate three-sigma, which is three standard deviations above the mean. In numerical format, this is (3 x 0.5064) + 9.34 = 10.9. Since none of the data is at such a high point, the manufacturing testing process has not yet reached three-sigma quality levels.
Special Considerations
The term "three-sigma" points to three standard deviations. Shewhart set three standard deviation (3-sigma) limits as a rational and economic guide to minimum economic loss. Three-sigma limits set a range for the process parameter at 0.27% control limits. Three-sigma control limits are used to check data from a process and if it is within statistical control. This is done by checking if data points are within three standard deviations from the mean. The upper control limit (UCL) is set three-sigma levels above the mean, and the lower control limit (LCL) is set at three sigma levels below the mean.
Since around 99.73% of a controlled process will occur within plus or minus three sigmas, the data from a process ought to approximate a general distribution around the mean and within the pre-defined limits. On a bell curve, data that lie above the average and beyond the three-sigma line represent less than 1% of all data points.
Related terms:
Arithmetic Mean
The arithmetic mean is the sum of all the numbers in the series divided by the count of all numbers in the series. read more
Bell Curve
A bell curve describes the shape of data conforming to a normal distribution. read more
Business Valuation , Methods, & Examples
Business valuation is the process of estimating the value of a business or company. read more
Empirical Rule
The empirical rule is a statistical fact stating that for a normal distribution, 99.7% of observations will fall within three standard deviations from the mean. read more
Quality Control Chart
A quality control chart is a graphic that depicts whether sampled products or processes are meeting their intended specifications. read more
Standard Deviation
The standard deviation is a statistic that measures the dispersion of a dataset relative to its mean. It is calculated as the square root of variance by determining the variation between each data point relative to the mean. read more
Statistics
Statistics is the collection, description, analysis, and inference of conclusions from quantitative data. read more
Sum of Squares
Sum of squares is a statistical technique used in regression analysis to determine the dispersion of data points from their mean value. In a regression analysis, the goal is to determine how well a data series can be fitted to a function that might help to explain how the data series was generated. read more
T-Test
A t-test is a type of inferential statistic used to determine if there is a significant difference between the means of two groups, which may be related in certain features. read more
Variance , Formula, & Calculation
Variance is a measurement of the spread between numbers in a data set. Investors use the variance equation to evaluate a portfolio’s asset allocation. read more