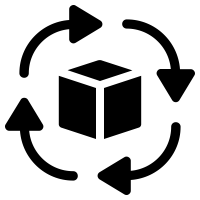
Supply Chain
Table of Contents What Is a Supply Chain? A goal of supply chain management is to improve efficiency by coordinating the efforts of the various entities in the supply chain. Supply chain management is a crucial process because an optimized supply chain results in lower costs and a faster production cycle. The key steps in a supply chain include: 1. Planning the inventory and manufacturing processes to ensure supply and demand are adequately balanced 2. Manufacturing or sourcing materials needed to create the final product 3. Assembling parts and testing the product 4. Packaging the product for shipment (or holding in inventory until a later date) 5. Transporting and delivering the finished product to the distributor, retailer, or consumer 6. Providing customer service support for returned items
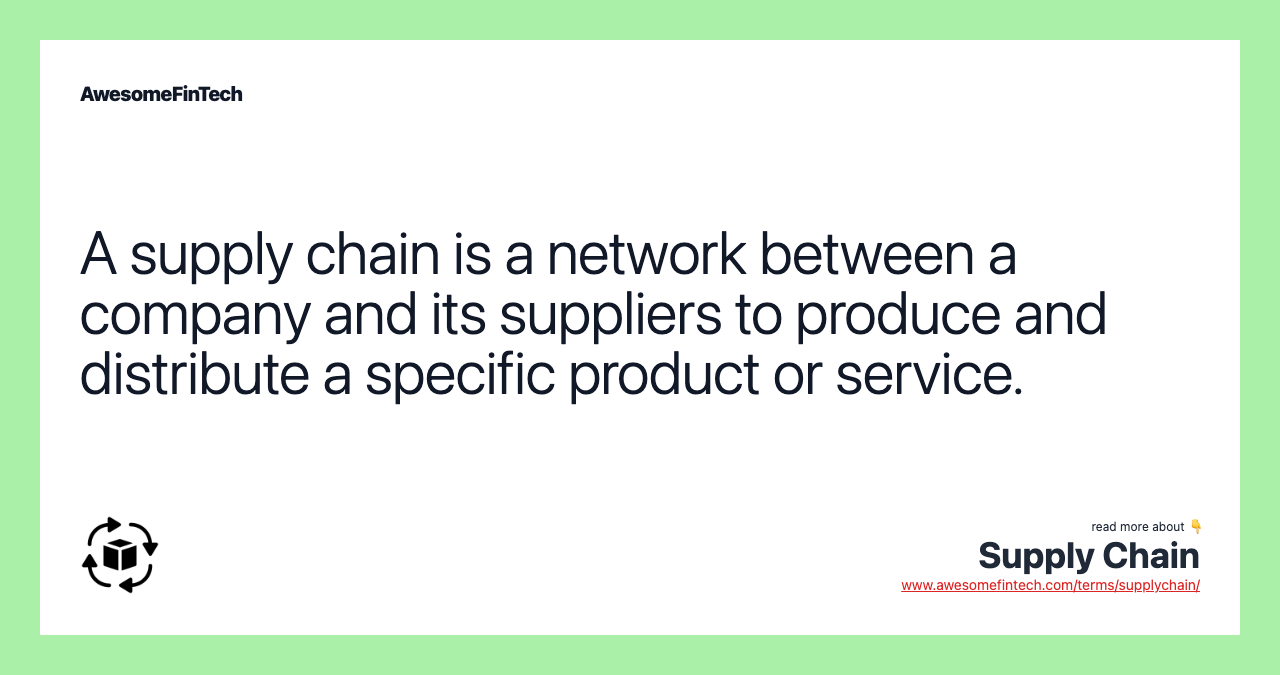
What Is a Supply Chain?
A supply chain is a network between a company and its suppliers to produce and distribute a specific product to the final buyer. This network includes different activities, people, entities, information, and resources. The supply chain also represents the steps it takes to get the product or service from its original state to the customer.
Companies develop supply chains so they can reduce their costs and remain competitive in the business landscape.
Supply chain management is a crucial process because an optimized supply chain results in lower costs and a faster production cycle.
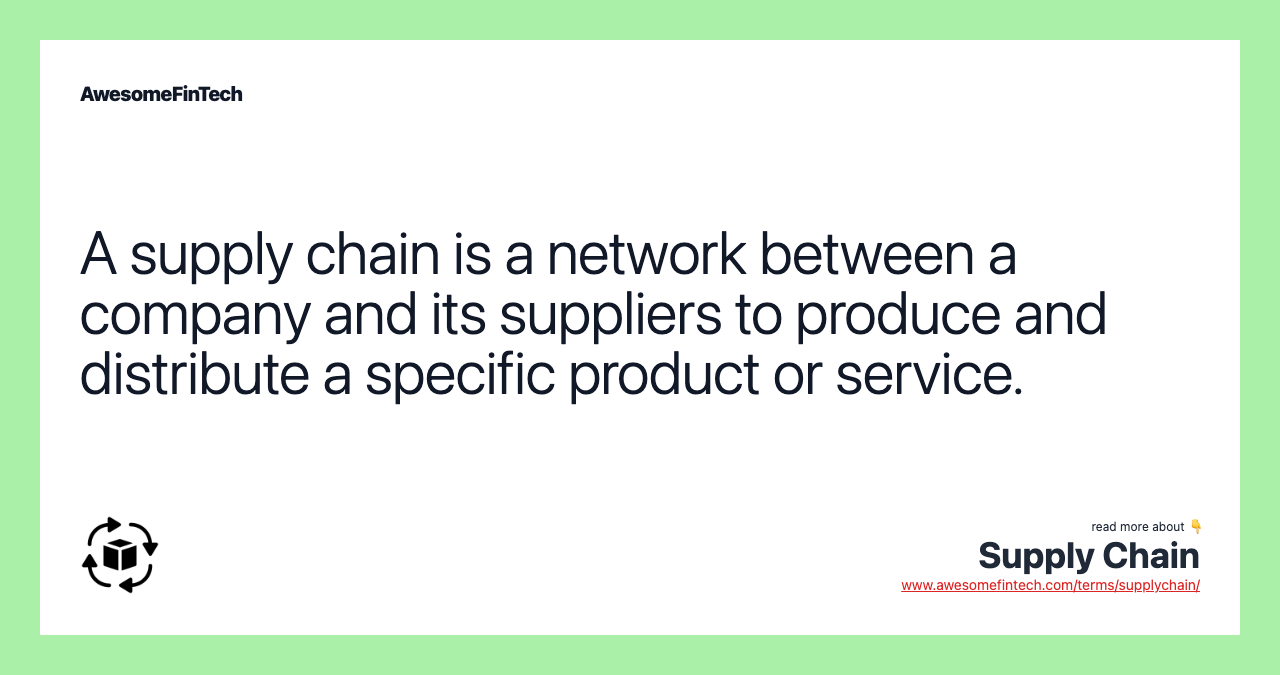
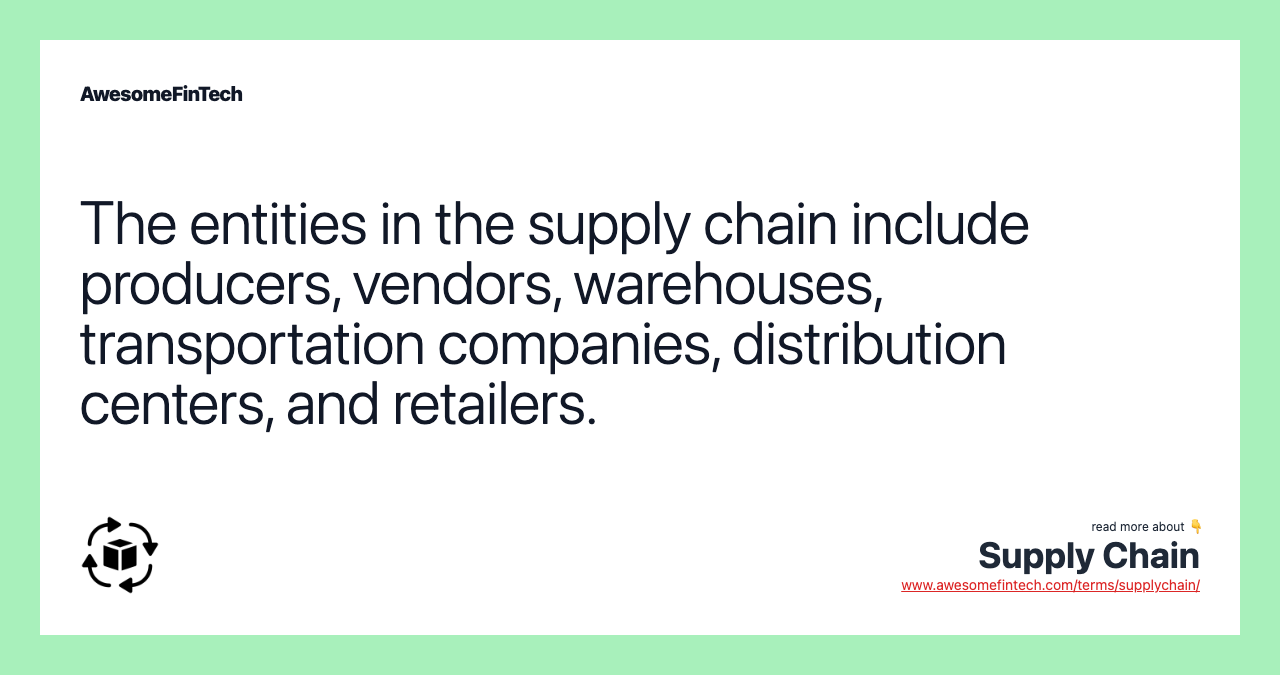
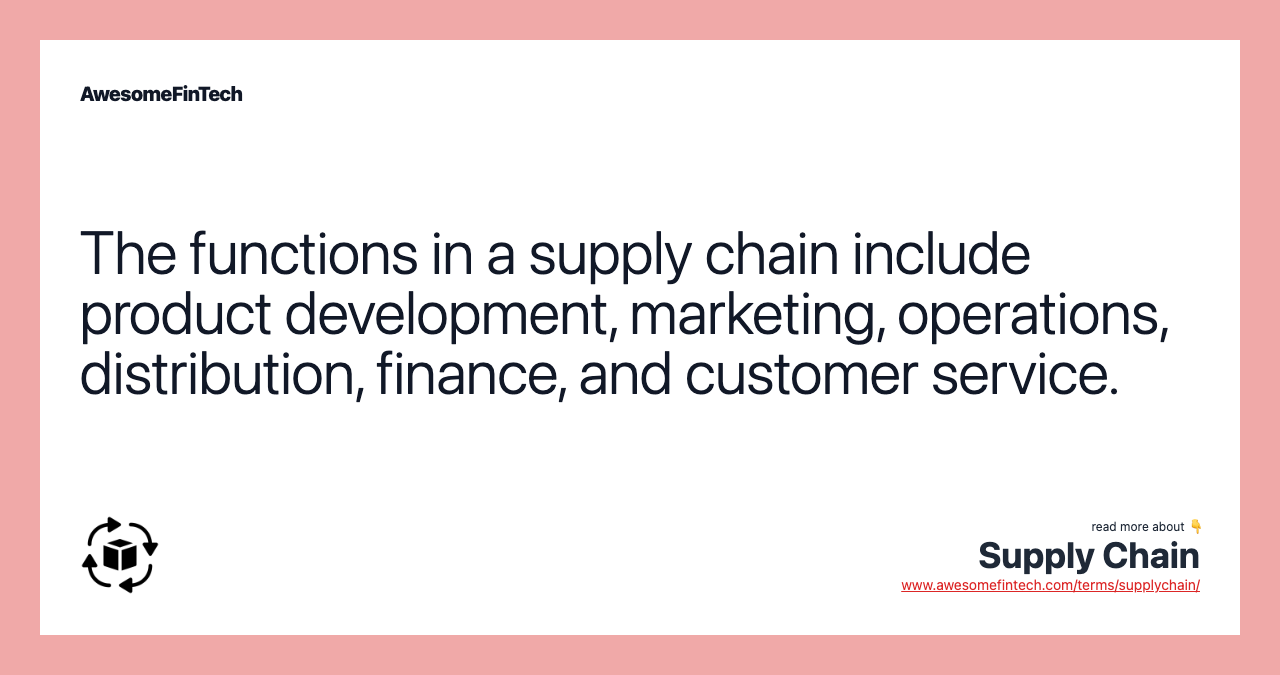
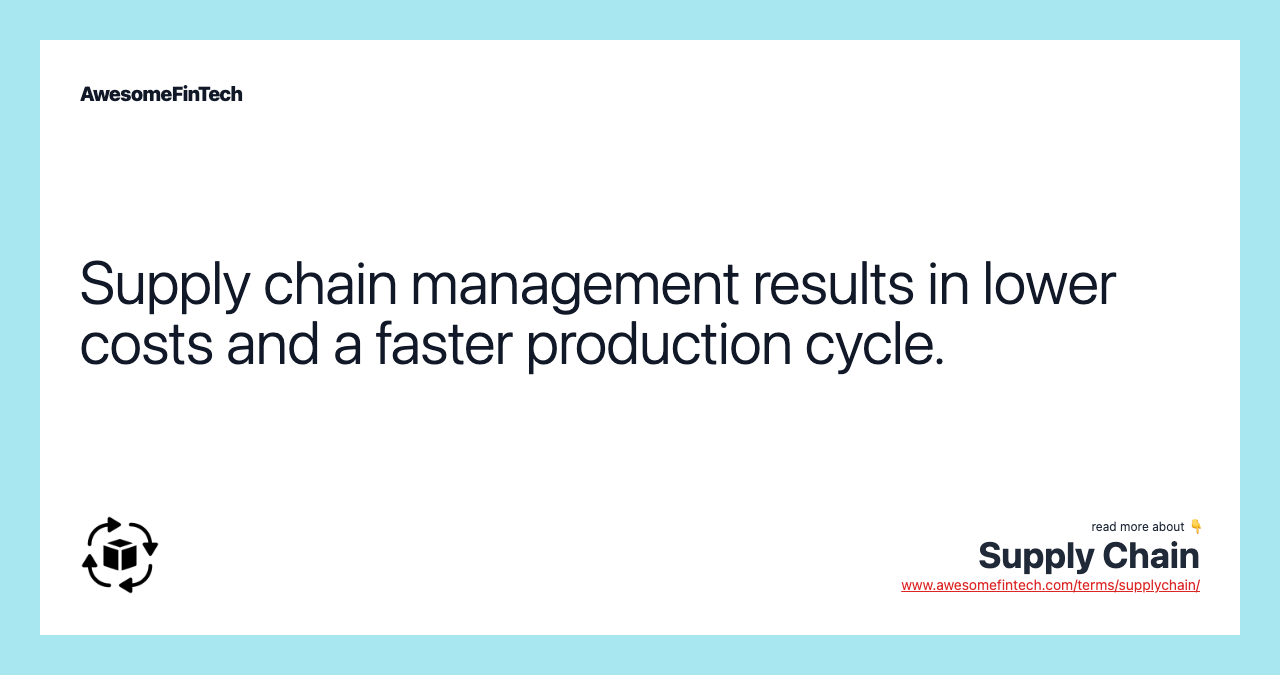
Understanding Supply Chains
A supply chain involves a series of steps involved to get a product or service to the customer. The steps include moving and transforming raw materials into finished products, transporting those products, and distributing them to the end-user. The entities involved in the supply chain include producers, vendors, warehouses, transportation companies, distribution centers, and retailers.
The elements of a supply chain include all the functions that start with receiving an order to meeting the customer's request. These functions include product development, marketing, operations, distribution networks, finance, and customer service.
Supply chain management is a very important part of the business process. There are many different links in this chain that require skill and expertise. When supply chain management is effective, it can lower a company's overall costs and boost profitability. If one link breaks down, it can affect the rest of the chain and can be costly.
Supply Chain Management vs. Business Logistics Management
The terms supply chain management and business logistics management — or simply, logistics — are often used interchangeably. Logistics, which is one link in the supply chain, is different.
Logistics refers specifically to the part of the supply chain that deals with the planning and control of the movement and storage of goods and services from their point of origin to their final destination. Logistics management begins with the raw materials and ends with the delivery of the final product.
Successful logistics management ensures that there is no delay in delivery at any point in the chain and that products and services are delivered in good condition. This, in turn, helps keep the company's costs down.
How the Flow of Manufacturing Costs Works
The flow of manufacturing costs refers to the process of using materials and labor to complete a finished product that can be sold to a customer. A supply chain management system can reduce the cost and complexity of the manufacturing process, particularly for a manufacturer who uses many parts.
For example, a clothing manufacturer may first move raw materials into production, such as fabric, zippers, and other pieces used to make clothing. The manufacturer then incurs labor costs to run machinery and perform other work using the materials. Once the items are completed, they must be packaged and stored until they are sold to a customer.
Reliable Suppliers
An efficient supply chain management process requires reliable suppliers. This means they produce a quality product that meets the manufacturer’s needs, and the product is delivered on time.
Assume, for example, that XYZ Furniture manufactures high-end furniture, and that a supplier provides metal handles and other attachments. The metal components need to be durable so they can be used on the furniture for years, and the metal parts shipped to XYZ should work as intended. The supplier must be able to fill the manufacturer’s orders and ship metal parts to meet XYZ’s production needs. These steps are necessary to produce a quality product that is shipped to a customer in a timely manner.
Supply Chain and Deflation
The evolution and increased efficiencies of supply chains have played a significant role in curbing inflation. As efficiencies in moving products from A to B increase, the costs in doing so decrease, which lowers the final cost to the consumer. While deflation is often regarded as a negative, supply chain efficiencies are one of the few examples where deflation is a good thing.
As globalization continues, supply chain efficiencies become more optimized, which keeps the pressure on input prices.
Supply Chain and COVID-19
The impact of the COVID-19 pandemic on the economy has been felt in nearly every sector, however, supply chain strategy has been one of the hardest-hit facets of every industry. Not only were companies' supply chains put in flux by ever-changing restrictions at national borders, which cut off access to key suppliers, demand for certain products also changed.
In late 2020, EY performed a survey of 200 senior-level supply chain executives. The study pointed to three essential findings: the deep negative effect of the pandemic felt by most respondents (72% reported a negative impact), the shifting priorities for the supply chain industry ("increased visibility" being the top priority for the next 12-36 months), and the fact that the pandemic has accelerated the transition to digitization (64% of surveyed supply chain executives say digital transformation will accelerate due to the pandemic).
It's no doubt the pandemic has had an unprecedented impact on how businesses think about the supply chain. However, the shock to the system may help usher in a new era of increased communication and visibility between suppliers as well as efficient use of technology to expedite supply chain strategies.
What Are the Steps in a Supply Chain?
The key steps in a supply chain include:
- Planning the inventory and manufacturing processes to ensure supply and demand are adequately balanced
- Manufacturing or sourcing materials needed to create the final product
- Assembling parts and testing the product
- Packaging the product for shipment (or holding in inventory until a later date)
- Transporting and delivering the finished product to the distributor, retailer, or consumer
- Providing customer service support for returned items
What Is Supply Chain Management?
Supply chain management (SCM) refers to the oversight and control of all the activities required for a company to convert raw materials into finished products that are then sold to end-users. SCM provides centralized control for the planning, design, manufacturing, inventory, and distribution phases required to produce and sell a company's products.
A goal of supply chain management is to improve efficiency by coordinating the efforts of the various entities in the supply chain. This can result in a company achieving a competitive advantage over its rivals and enhancing the quality of the products it produces, both of which can lead to increased sales and revenue.
What Are the Types of Supply Chains?
There are many different types of supply chain models available to companies interested in implementing a strategy to improve efficiency and workflow. The type of supply chain model a company selects will often depend on how the company is structured and what its specific needs are. Here are a few examples:
Related terms:
Bottleneck
A bottleneck is a point of congestion in a production system that occurs when workloads arrive at a point more quickly than that point can handle them. read more
Deflation
Deflation is the decline in prices for goods and services that happens when the inflation rate dips below 0%. read more
Disintermediation
Disintermediation is the removal of a middleman in the supply chain to allow producers to sell directly to their customers. read more
Distribution Network
A distribution network is a company's interconnected group of storage facilities and transportation systems that move physical goods to customers. read more
Fast Fashion
Fast fashion are clothing designs that quickly move from idea to prototype to mass production to consumers. Learn how fast fashion retailers make money. read more
Inflation
Inflation is a decrease in the purchasing power of money, reflected in a general increase in the prices of goods and services in an economy. read more
Inventory Management
Inventory management is the process of ordering, storing and using a company's inventory: raw materials, components, and finished products. read more
Logistics
Logistics is the overall process of managing the way resources are obtained, stored, and moved to the locations where they are required. read more
Mergers and Acquisitions (M&A)
Mergers and acquisitions (M&A) refers to the consolidation of companies or assets through various types of financial transactions. read more
Operating Cost
Operating costs are expenses associated with normal day-to-day business operations. read more