
Overhead Rate
Table of Contents What Is the Overhead Rate? Formula and Calculation To calculate the overhead rate: Divide $20 million (indirect costs) by $5 million (direct labor costs). Overhead rate = $4 or ($20/$5), meaning that it costs the company $4 in overhead costs for every dollar in direct labor expenses. The overhead rate can also be expressed in terms of the number of hours. The overhead rate allocates indirect costs to the direct costs tied to production by spreading or allocating the overhead costs based on the dollar amount for direct costs, total labor hours, or even machine hours. To calculate the overhead rate: Divide $500,000 (indirect costs) by 30,000 (machine hours). Overhead rate = $16.66, meaning that it costs the company $16.66 in overhead costs for every hour the machine is in production. To allocate overhead costs, an overhead rate is applied to the direct costs tied to production by spreading or allocating the overhead costs based on specific measures.
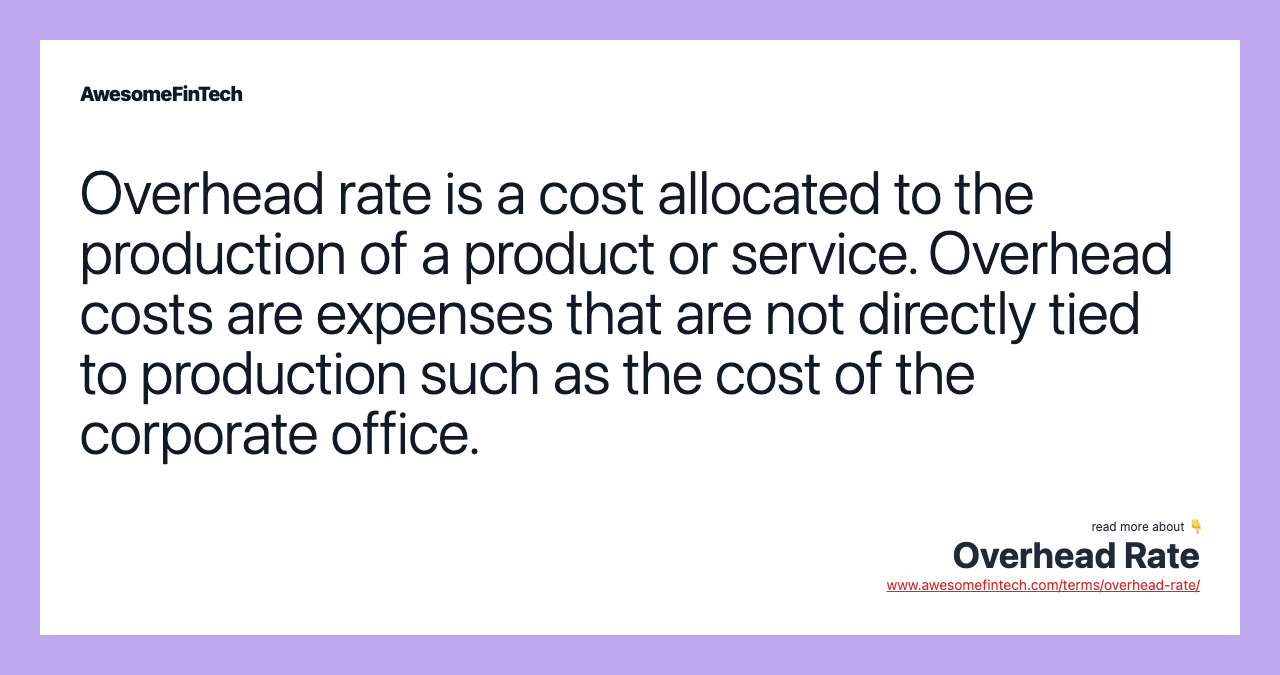
What Is the Overhead Rate?
The overhead rate is a cost allocated to the production of a product or service. Overhead costs are expenses that are not directly tied to production such as the cost of the corporate office. To allocate overhead costs, an overhead rate is applied to the direct costs tied to production by spreading or allocating the overhead costs based on specific measures.
For example, overhead costs may be applied at a set rate based on the number of machine hours or labor hours required for the product.
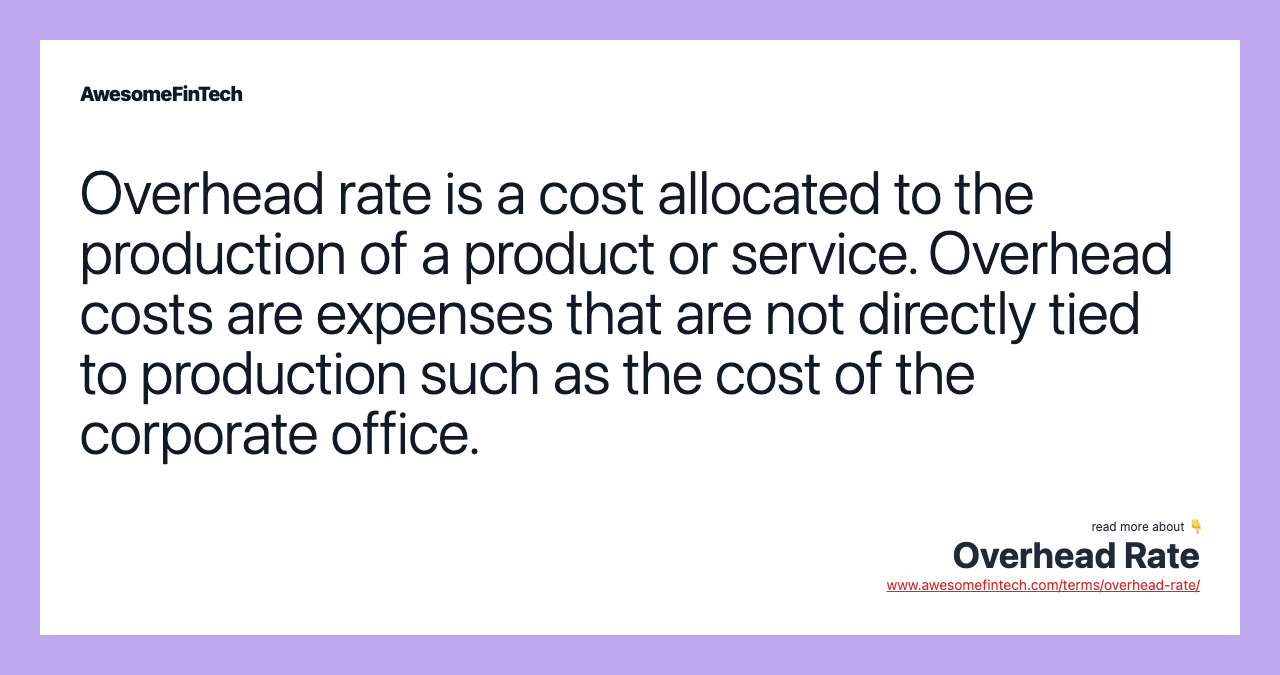
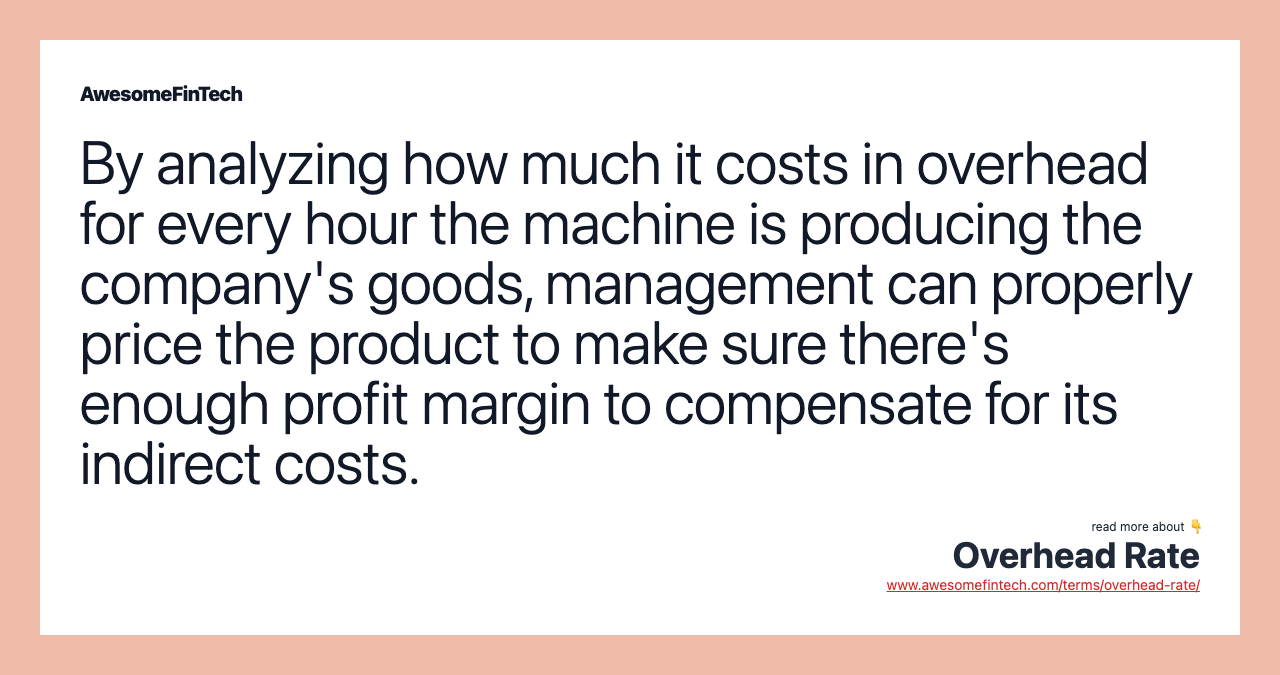
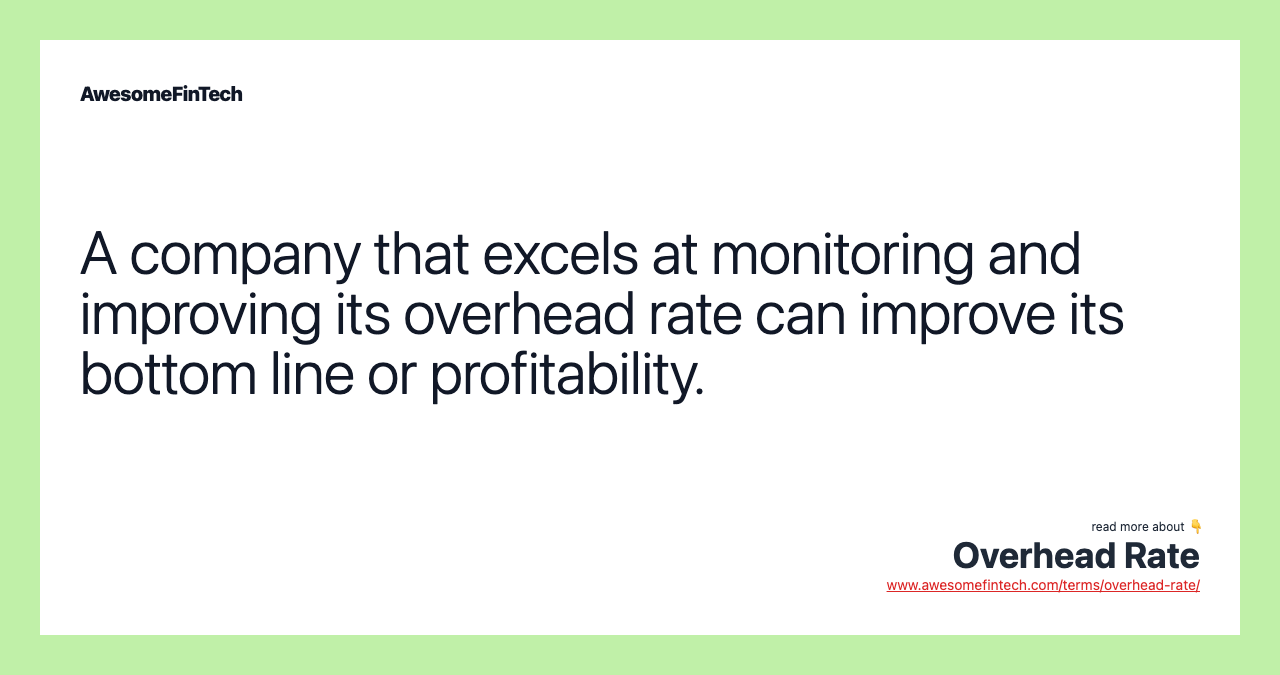
Overhead Rate Formula and Calculation
Although there are multiple ways to calculate an overhead rate, below is the basis for any calculation:
Overhead rate = Indirect costs Allocation measure \text{Overhead rate} = \frac{\text{Indirect costs}}{\text{Allocation measure}} Overhead rate=Allocation measureIndirect costs
The calculation of the overhead rate has a basis on a specific period. So, if you wanted to determine the indirect costs for a week, you would total up your weekly indirect or overhead costs. You would then take the measurement of what goes into production for the same period. So, if you were to measure the total direct labor cost for the week, the denominator would be the total weekly cost of direct labor for production that week. Finally, you would divide the indirect costs by the allocation measure to achieve how much in overhead costs for every dollar spent on direct labor for the week.
Using the Overhead Rate
The overhead rate is a cost added on to the direct costs of production in order to more accurately assess the profitability of each product. In more complicated cases, a combination of several cost drivers may be used to approximate overhead costs.
Overhead expenses are generally fixed costs, meaning they're incurred whether or not a factory produces a single item or a retail store sells a single product. Fixed costs would include building or office space rent, utilities, insurance, supplies, maintenance, and repair. Overhead costs also include administrative salaries and some professional and miscellaneous fees that are tucked under selling, general, and administrative (SG&A) within a firm's operating expenses on the income statement. Unless a cost can be directly attributable to a specific revenue-generating product or service, it will be classified as overhead, or as an indirect expense.
It is often difficult to assess precisely the amount of overhead costs that should be attributed to each production process. Costs must thus be estimated based on an overhead rate for each cost driver or activity. It is important to include indirect costs that are based on this overhead rate in order to price a product or service appropriately. If a company prices its products so low that revenues do not cover its overhead costs, the business will be unprofitable.
Direct Costs vs. the Overhead Rate
Direct costs are costs directly tied to a product or service that a company produces. Direct costs can be easily traced to their cost objects. Cost objects can include goods, services, departments, or projects. Direct costs include direct labor, direct materials, manufacturing supplies, and wages tied to production.
The overhead rate allocates indirect costs to the direct costs tied to production by spreading or allocating the overhead costs based on the dollar amount for direct costs, total labor hours, or even machine hours.
Limitations of the Overhead Rate
The overhead rate has limitations when applying it to companies that have few overhead costs or when their costs are mostly tied to production. Also, it's important to compare the overhead rate to companies within the same industry. A large company with a corporate office, a benefits department, and a human resources division will have a higher overhead rate than a company that's far smaller and with less indirect costs.
Examples of Overhead Rates
The equation for the overhead rate is overhead (or indirect) costs divided by direct costs or whatever you're measuring. Direct costs typically are direct labor, direct machine costs, or direct material costs — all expressed in dollar amounts. Each one of these is also known as an "activity driver" or "allocation measure."
Example 1: Costs in Dollars
Let's assume a company has overhead expenses that total $20 million for the period. The company wants to know how much overhead relates to direct labor costs. The company has direct labor expenses totaling $5 million for the same period.
To calculate the overhead rate:
Example 2: Cost per Hour
The overhead rate can also be expressed in terms of the number of hours. Let's say a company has overhead expenses totaling $500,000 for one month. During that same month, the company logs 30,000 machine hours to produce their goods.
To calculate the overhead rate:
By analyzing how much it costs in overhead for every hour the machine is producing the company's goods, management can properly price the product to make sure there's enough profit margin to compensate for the $16.66 per hour in indirect costs.
Of course, management also has to price the product to cover the direct costs involved in the production, including direct labor, electricity, and raw materials. A company that excels at monitoring and improving its overhead rate can improve its bottom line or profitability.
Related terms:
Absorbed
Absorbed as a business term generally refers to taking in, acquiring or bearing. The term can be applied in a number of situations. read more
Absorption Costing
Absorption costing is a managerial accounting method for capturing all costs associated with the manufacture of a particular product. read more
Accounting
Accounting is the process of recording, summarizing, analyzing, and reporting financial transactions of a business to oversight agencies, regulators, and the IRS. read more
Applied Overhead
Applied overhead is a fixed charge assigned to a specific production job or department within a business. read more
Bottom Line
The bottom line refers to a company's earnings, profit, net income, or earnings per share (EPS). Learn how companies can improve their bottom line. read more
Corporation
A corporation is a legal entity that is separate and distinct from its owners and has many of the same rights and responsibilities as individuals. read more
Departmental Overhead Rate
The departmental overhead rate is defined as an expense rate for every department in a factory production process. read more
Direct Cost
A direct cost is a price that can be completely attributed to the production of specific goods or services. read more
Income Statement : Uses & Examples
An income statement is one of the three major financial statements that reports a company's financial performance over a specific accounting period. read more