
What Are Holding Costs?
Holding costs are those associated with storing inventory that remains unsold. A firm’s holding costs include the price of goods damaged or spoiled, as well as that of storage space, labor, and insurance. Holding costs are costs associated with storing unsold inventory. A firm’s holding costs include storage space, labor, and insurance, as well as the price of damaged or spoiled goods. Minimizing inventory costs is an important supply-chain management strategy. Strategies to avoid holding costs include quick payment collection and calculating accurate reorder points. Minimizing inventory costs is an important supply-chain management strategy. Another important strategy to minimize holding costs and other inventory spending is to calculate a reorder point, or the level of inventory that alerts the company to order more inventory from a supplier. Businesses measure the frequency of cash collections using the inventory turnover ratio, which is calculated as the cost of goods sold (COGS) divided by average inventory. These costs are one component of total inventory costs, along with ordering and shortage costs.
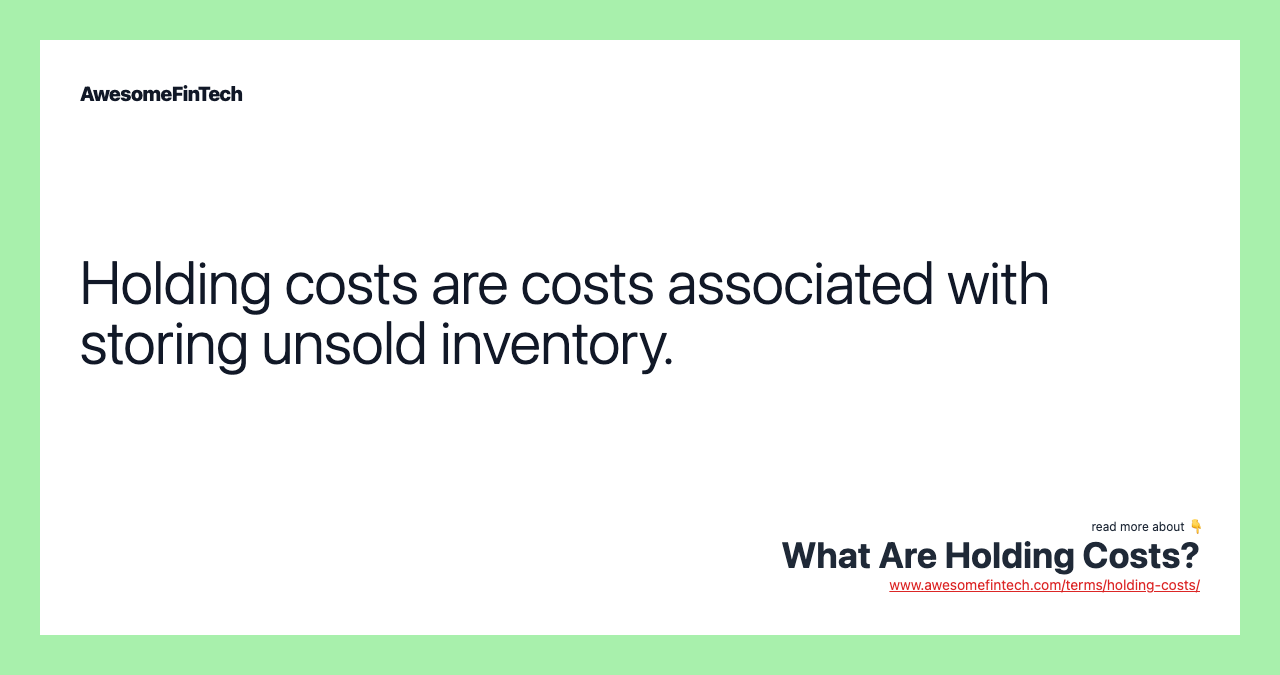
What Are Holding Costs?
Holding costs are those associated with storing inventory that remains unsold. These costs are one component of total inventory costs, along with ordering and shortage costs.
A firm’s holding costs include the price of goods damaged or spoiled, as well as that of storage space, labor, and insurance.
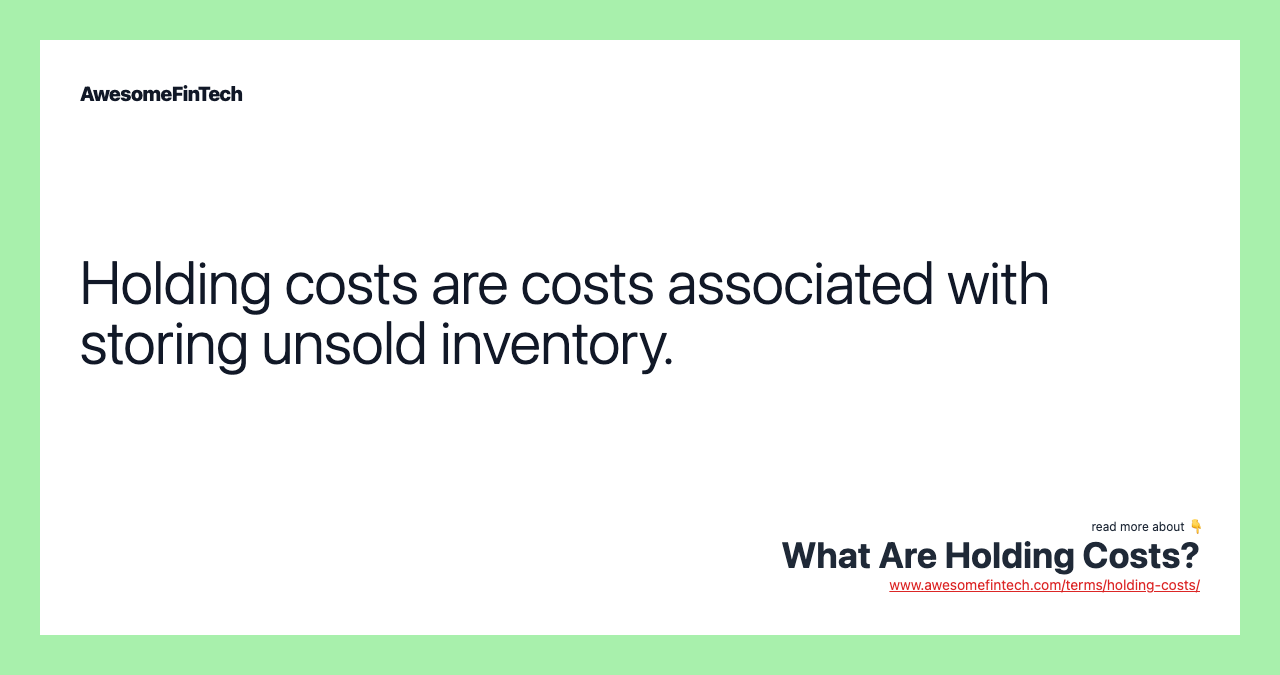
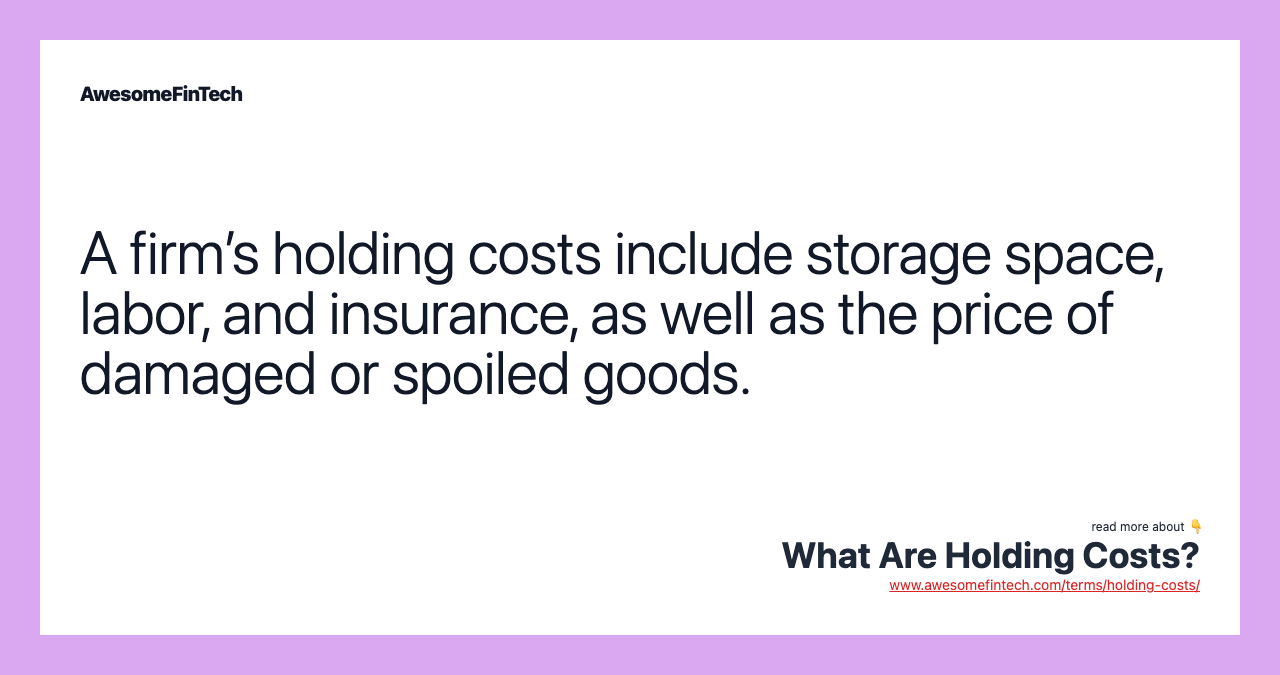
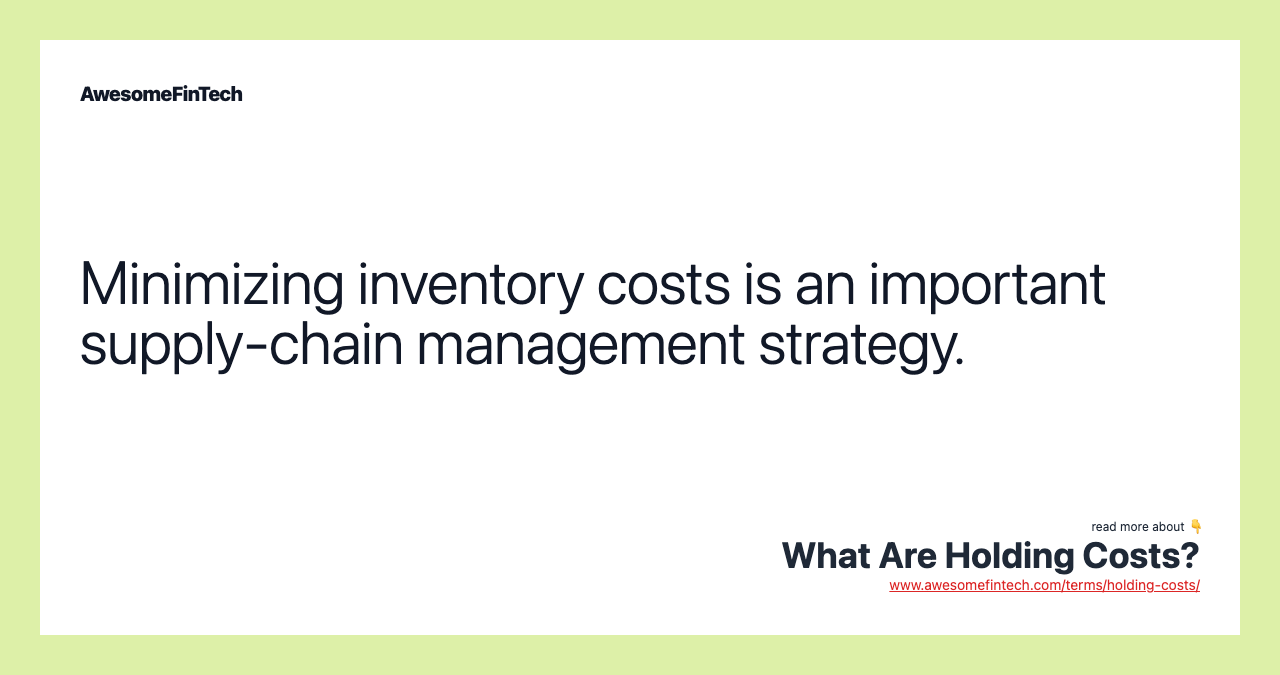
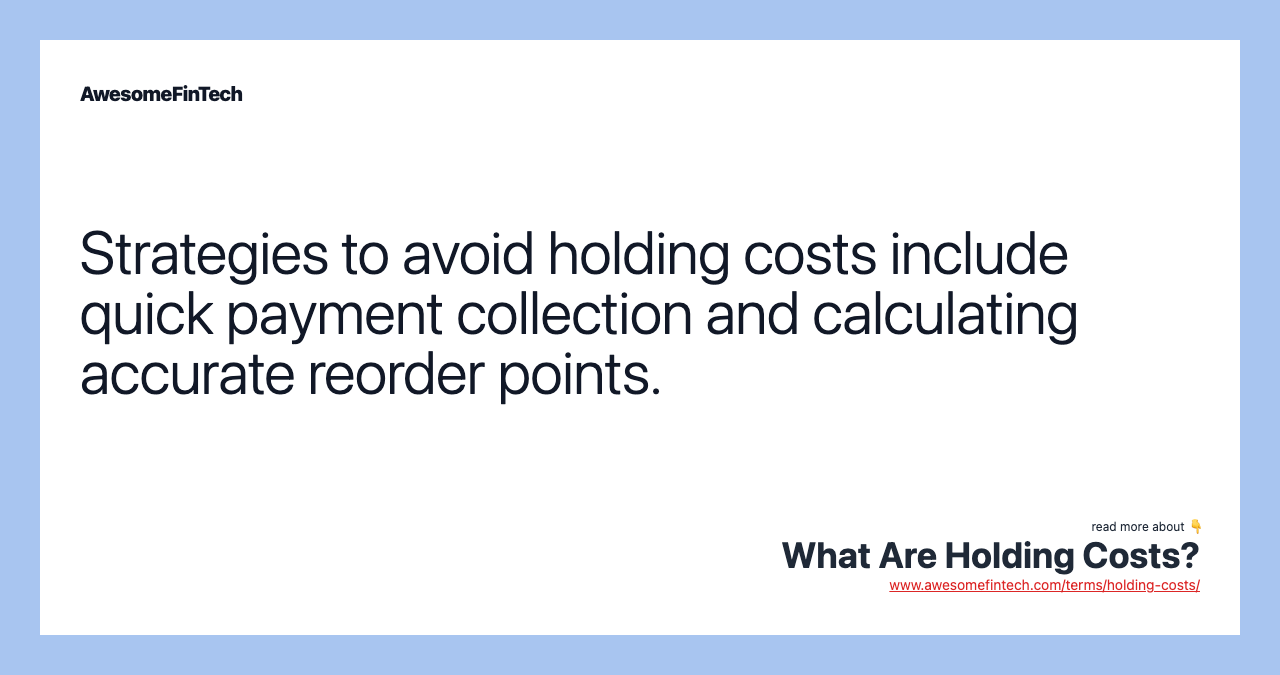
Understanding Holding Costs
Minimizing inventory costs is an important supply-chain management strategy. Inventory is an asset account that requires a large amount of cash outlay, and decisions about inventory spending can reduce the amount of cash available for other purposes.
For example, increasing the inventory balance by $10,000 means that less cash is available to operate the business each month. This situation is considered an opportunity cost.
Holding Costs Example
Assume that ABC Manufacturing produces furniture that is stored in a warehouse and then shipped to retailers. ABC must either lease or purchase warehouse space and pay for utilities, insurance, and security for the location.
The company must also pay staff to move inventory into the warehouse and then load the sold merchandise onto trucks for shipping. The firm incurs some risk that the furniture may be damaged as it is moved into and out of the warehouse.
Holding Cost Reduction Methods
One way to ensure a company has sufficient cash to run its operations is to sell inventory and collect payments quickly. The sooner cash is collected from customers, and the less total cash the firm must come up with to continue operations. Businesses measure the frequency of cash collections using the inventory turnover ratio, which is calculated as the cost of goods sold (COGS) divided by average inventory.
For example, a company with $1 million in cost of goods sold and an inventory balance of $200,000 has a turnover ratio of five. The goal is to increase sales and reduce the required amount of inventory so that the turnover ratio increases.
Another important strategy to minimize holding costs and other inventory spending is to calculate a reorder point, or the level of inventory that alerts the company to order more inventory from a supplier. An accurate reorder point allows the firm to fill customer orders without overspending on storing inventory. Companies that use a reorder point avoid shortage costs, which is the risk of losing a customer order due to low inventory levels.
The reorder point considers how long it takes to receive an order from a supplier, as well as the weekly or monthly level of product sales. A reorder point also helps the business compute the economic order quantity (EOQ), or the ideal amount of inventory that should be ordered from a supplier. EOQ can be calculated using inventory software.
Related terms:
Asset
An asset is a resource with economic value that an individual or corporation owns or controls with the expectation that it will provide a future benefit. read more
Average Inventory
Average inventory is a calculation that estimates the value or number of a particular good or set of goods during two or more specified time periods. read more
Backorder Costs
Backorder costs are costs incurred by a business when it is unable to immediately fill an order with readily available inventory and must extend the delivery time. read more
Bottleneck
A bottleneck is a point of congestion in a production system that occurs when workloads arrive at a point more quickly than that point can handle them. read more
Carrying Costs
Carrying costs, also known as holding costs and inventory carrying costs, are the costs a business pays for holding inventory in stock. read more
Cost of Goods Sold – COGS
Cost of goods sold (COGS) is defined as the direct costs attributable to the production of the goods sold in a company. read more
Economic Order Quantity (EOQ) & Formula
Economic order quantity (EOQ) is the ideal order quantity that a company should make for its inventory given a set cost of production, demand rate, and other variables. read more
Free On Board (FOB) : Uses & Examples
Free On Board (FOB) is a trade term indicating the point at which a buyer or seller becomes liable for goods being transported on a vessel. read more
Inventory Management
Inventory management is the process of ordering, storing and using a company's inventory: raw materials, components, and finished products. read more
Inventory :
Inventory is the term for merchandise or raw materials that a company has on hand. read more