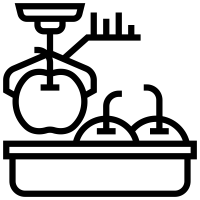
Goods-In-Process
Accounting rules demand a breakdown of this process, requiring these companies to keep separate accounts for the goods they stock as they enter each stage of production. Goods-in-process is one of three manufacturing inventory classifications and can be described as an intermediate state between the other two: raw materials and finished goods. Inventory, a current asset on the company's balance sheet, is the total of the three states of production. The numerical accounting for goods-in-process at the end of any period is the beginning balance of good-in-process, plus the value of raw materials transferred into the account, minus the ending balance of goods-in-process. In the note to its financial statements, this figure was broken down into $2.2 billion in raw materials and supplies, $0.8 billion in goods-in-process, or work-in-process, and $4.8 billion in finished goods and parts. Typically, the goods-in-process sub-account carries the smallest amount among the three inventory classifications if the company engages in high production volumes of whatever it makes.
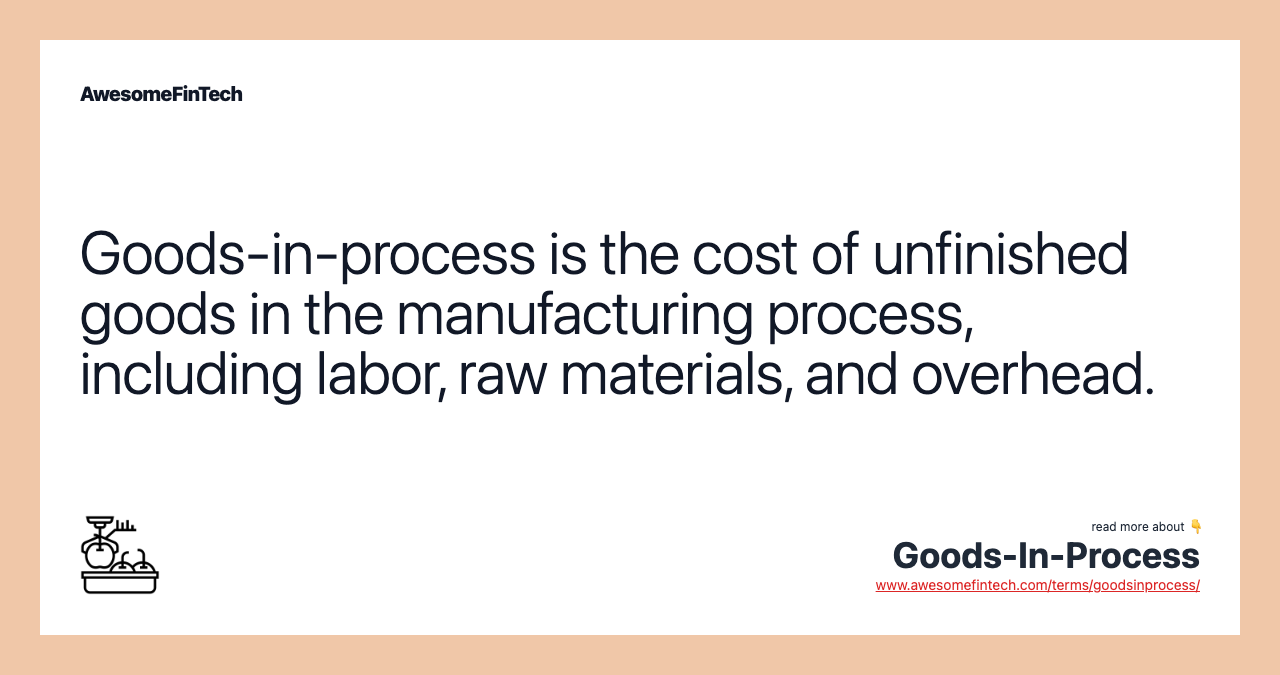
What Is Goods-in-Process?
Goods-in-process is part of an inventory account on the balance sheet of a manufacturing company. It relates to partially completed goods that are somewhere in the manufacturing process and not yet ready for sale.
Goods-in-process is also known as "work-in-process" or "work-in-progress."
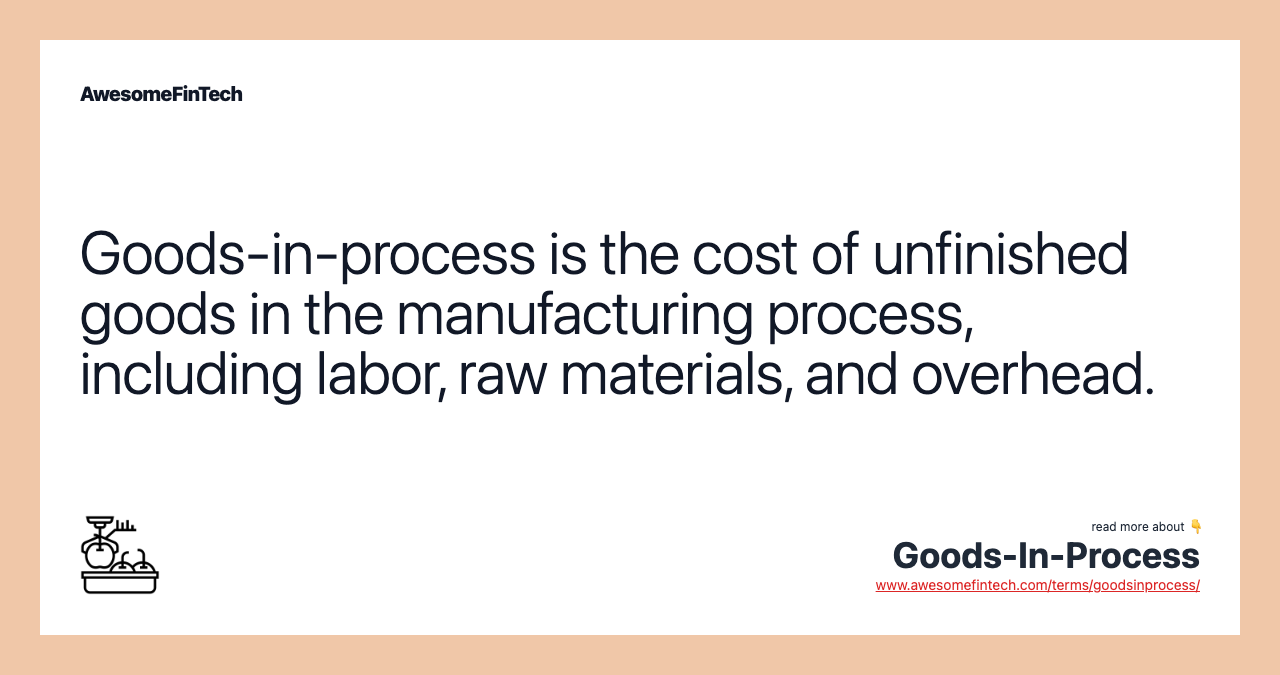
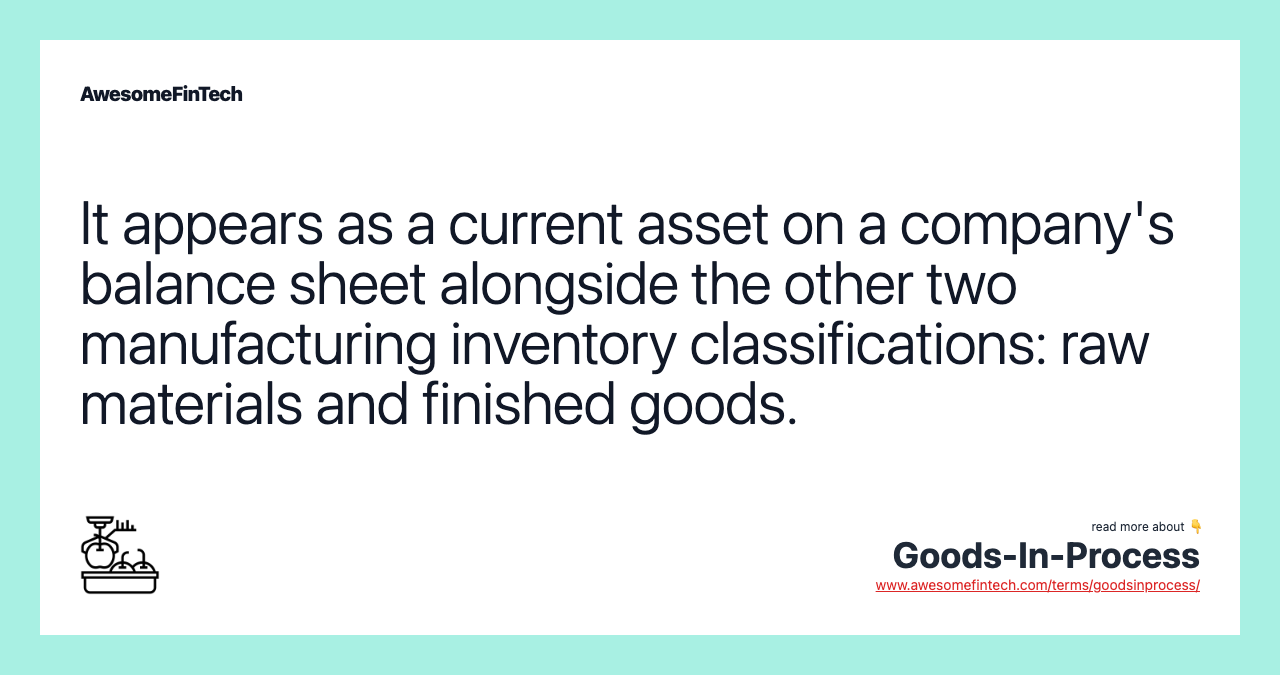
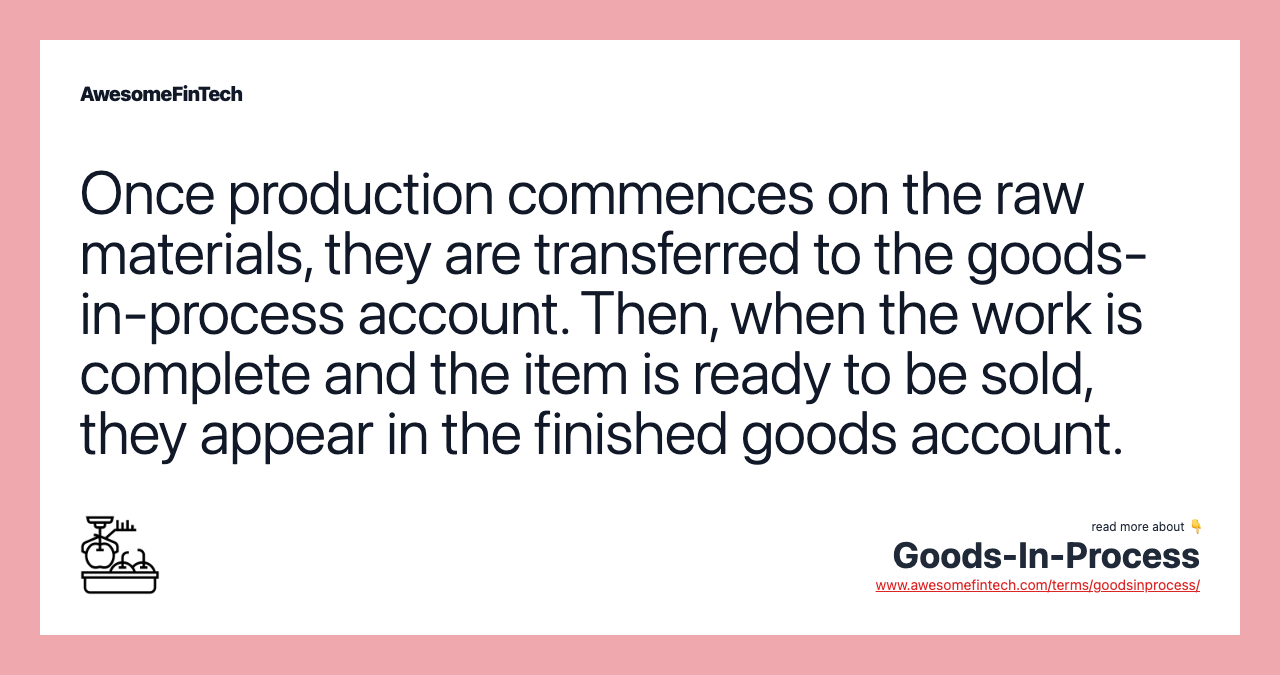
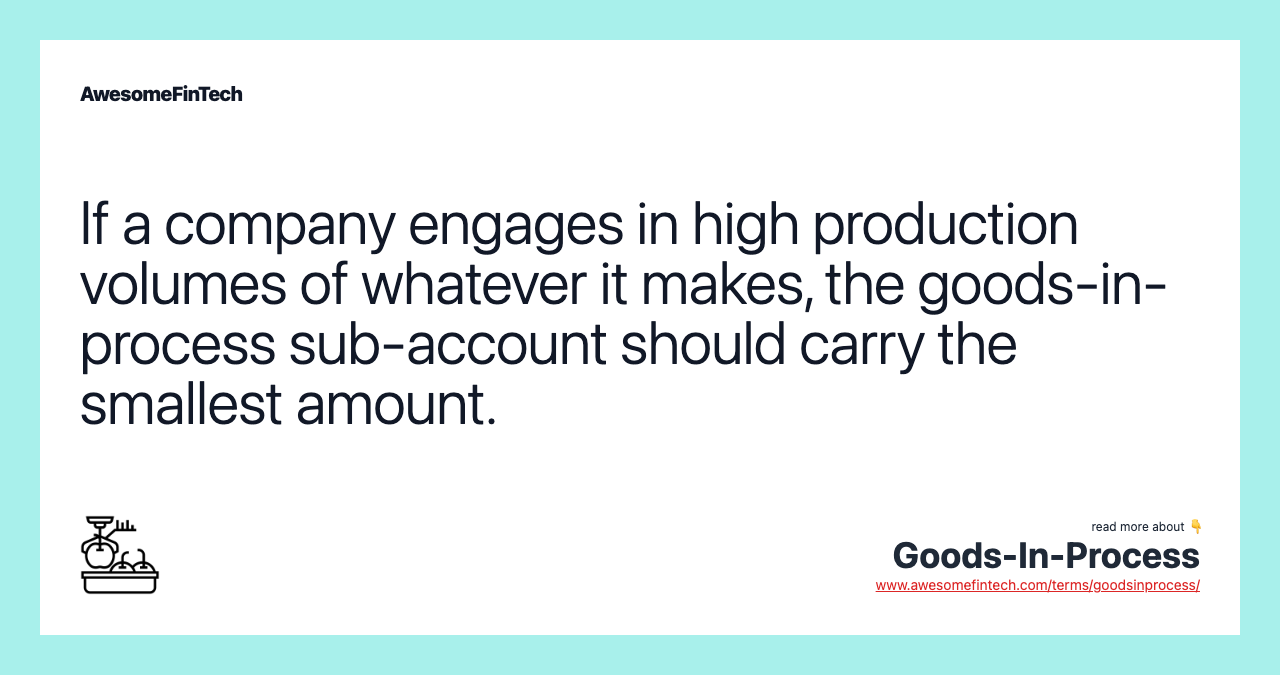
Understanding Goods-in-Process
Unlike some other companies, manufacturers physically produce their inventory, sourcing raw materials, and then moving them into production or assembly mode until they are completed and ready to sell to customers.
Accounting rules demand a breakdown of this process, requiring these companies to keep separate accounts for the goods they stock as they enter each stage of production.
Goods-in-process is one of three manufacturing inventory classifications and can be described as an intermediate state between the other two: raw materials and finished goods. Inventory, a current asset on the company's balance sheet, is the total of the three states of production.
The numerical accounting for goods-in-process at the end of any period is the beginning balance of good-in-process, plus the value of raw materials transferred into the account, minus the ending balance of goods-in-process. Included in this account are costs of direct labor and material, as well as an allocation of manufacturing overhead.
Goods-in-process reveals the raw materials, labor, and overhead costs incurred for products that are at various stages of the production process.
Once production of these goods is completed, they are moved to the finished inventory account and then, later on, registered as cost of goods sold (COGS). Typically, the goods-in-process sub-account carries the smallest amount among the three inventory classifications if the company engages in high production volumes of whatever it makes.
Example of Goods-in-Process
Deere & Company (DE), a manufacturer of farming, snow removal, lawn mowing, and construction equipment, purchases raw materials, mainly consisting of steel products, steel, and iron castings, forgings, plastics, electronics, and ready-to-assemble components, on a regular basis. Once these materials are shipped in, factory floor machinists and assembly line workers begin to fabricate equipment out of them to sell to the company’s customers.
As soon as work commences on the raw materials, they are transferred to the goods-in-process account. That remains the case until the materials are transformed into the completed item, at which point they are then moved across to the finished goods account.
For its 2018 fiscal year (FY), Deere & Co. recorded an inventory value of $6.1 billion. In the note to its financial statements, this figure was broken down into $2.2 billion in raw materials and supplies, $0.8 billion in goods-in-process, or work-in-process, and $4.8 billion in finished goods and parts.
After a $1.6 billion adjustment to "last-in, first-out" (LIFO) value, the inventory account totaled $6.1 billion. Note that the goods-in-process sub-account is a minor fraction of the total.
Benefits of Goods-in-Process
Changes in goods-in-process can tell us a lot about how a company is faring. An uptick could indicate a rush to the factory floor to cater to an increase in demand for the company’s products. That’s generally a good omen for shareholders, and when widespread, the overall economy.
Decreases are generally viewed less favorably. What they tend to signal is a slowdown in production, reflecting weakening demand.
Special Considerations
Investors should seek to determine how a company measures goods-in-process and other inventory accounts. Accountants sometimes employ different calculation strategies, so goods-in-process are not always comparable across companies.
Related terms:
Accountant
An accountant is a certified financial professional who performs functions such as audits or financial statement analysis according to prescribed methods. read more
Accounting Standard
An accounting standard is a common set of principles, standards, and procedures that define the basis of financial accounting policies and practices. read more
Balance Sheet : Formula & Examples
A balance sheet is a financial statement that reports a company's assets, liabilities and shareholder equity at a specific point in time. read more
Cost of Goods Sold – COGS
Cost of goods sold (COGS) is defined as the direct costs attributable to the production of the goods sold in a company. read more
Current Assets
Current assets are a balance sheet item that represents the value of all assets that could reasonably be expected to be converted into cash within one year. read more
Demand
Demand is an economic principle that describes consumer willingness to pay a price for a good or service. read more
Ending Inventory
Ending inventory is a common financial metric measuring the final value of goods still available for sale at the end of an accounting period. read more
Fiscal Year (FY)
A fiscal year is a one-year period of time that a company or government uses for accounting purposes and preparation of its financial statements. read more
What Are Footnotes to the Financial Statements?
Footnotes to the financial statements refer to additional information that help explain how a company arrived at its financial statement figures. read more
Inventory Management
Inventory management is the process of ordering, storing and using a company's inventory: raw materials, components, and finished products. read more