
Capacity Requirements Planning (CRP)
Capacity requirements planning (CRP) is the process of discerning a firm's available production capacity and whether it can meet its production goals. Capacity requirements planning is the process through which a company — primarily in manufacturing — figures out how much product it needs to make, and determines if it has the ability to meet its production goals. You can also understand CRP as a management tool that's based on using a company's resources efficiently by projecting its production expectations accurately. If a company finds that its production capacity is inadequate, it may alter its production goals, or take other steps to bring expectations in line with capacity — which could include contracting with another firm that has excess capacity to handle its production. **Determining the unit of work**: Create a definition of satisfactory service for each portion of work; a workload measures the resources needed to accomplish the work, and a unit of work measures the quantity of work completed. **Setting service levels**: A service-level agreement (SLA) lays out the acceptable parameters between provider and consumer. Then, capacity requirements planning weighs this schedule against the company's actual production capabilities to see if the current capacity can successfully meet the existing production schedule.
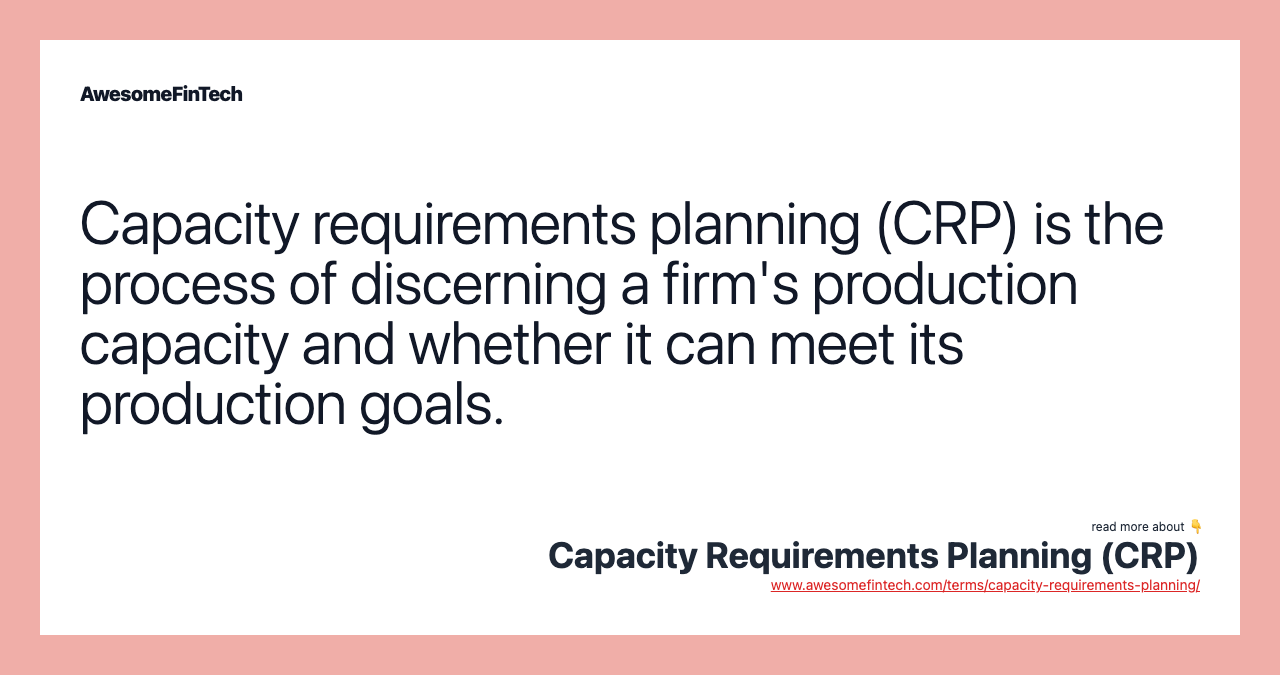
What Is Capacity Requirements Planning (CRP)?
Capacity requirements planning (CRP) is the process of discerning a firm's available production capacity and whether it can meet its production goals. The CRP method first assesses the company's planned manufacturing schedule. Then, capacity requirements planning weighs this schedule against the company's actual production capabilities to see if the current capacity can successfully meet the existing production schedule.
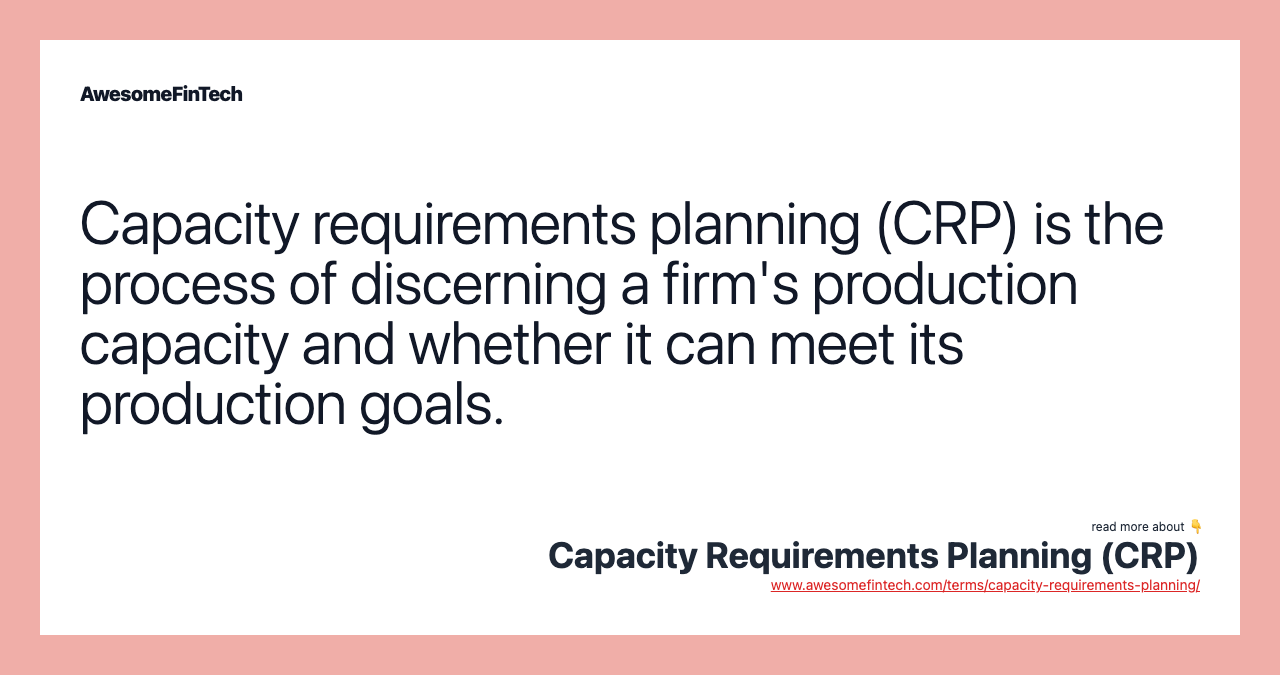
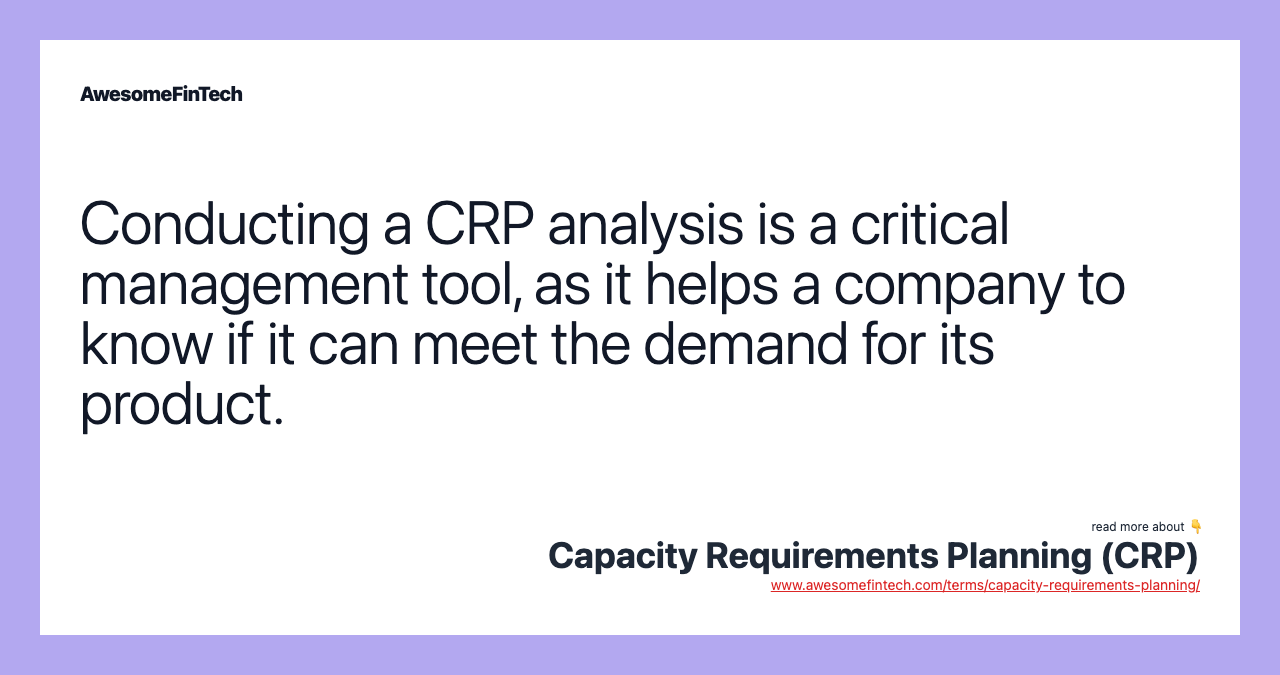
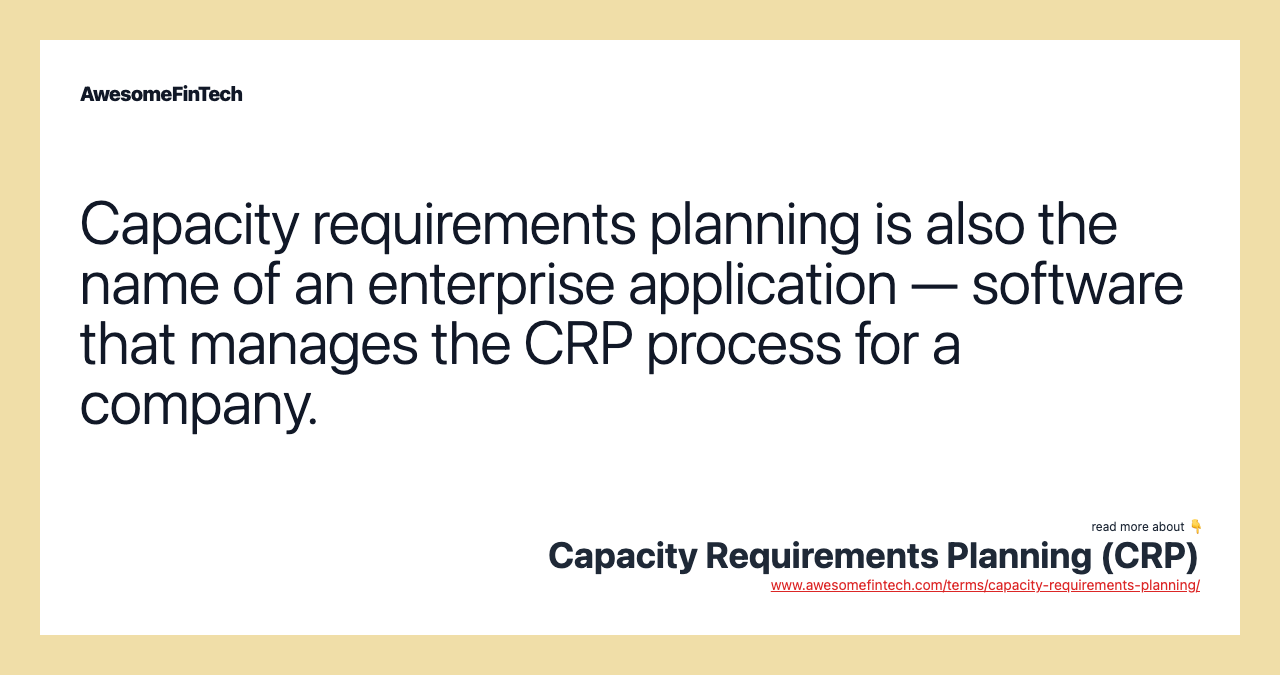
Understanding Capacity Requirements Planning
Capacity requirements planning is the process through which a company — primarily in manufacturing — figures out how much product it needs to make, and determines if it has the ability to meet its production goals.
You can also understand CRP as a management tool that's based on using a company's resources efficiently by projecting its production expectations accurately. If a company finds that its production capacity is inadequate, it may alter its production goals, or take other steps to bring expectations in line with capacity — which could include contracting with another firm that has excess capacity to handle its production.
Why Does CRP Matter?
A large part of a company's success is in planning for the future. Without a solid plan, a business owner may risk encountering unforeseen issues, including those that can affect its bottom line.
Capacity requirements planning has both long- and short-term implications for a firm's success. In the short term, monthly and quarterly sales numbers are heavily affected by whether the company is prepared for the regular ups and downs of customer demand. Not being able to meet customer demand can often mean losing customers to the competition. In the long term, CRP can help to decide how much a company will invest in its employees, materials, and equipment.
Discrepancies between capacity estimates and the actual production output can result in a shortage of products or personnel, which could cause long delays in deliveries and even leave some customers' orders completely unfilled. Poor CRP can also lead to oversupply, in which unused inventory ties up a company’s revenue and depresses reported earnings.
CRP Procedures
Businesses generally develop their own capacity requirements plans based on individual factors, including their industry and sector. However, we may broadly categorize CRP into three rudimentary portions: determining service-level requirements, analyzing current capacity, and planning for the future.
Determining Service-Level Requirements
A business may divide its work into categories and quantify users’ expectations for how that work gets done:
Analyze Current Capacity
Here are some steps that a business can take to analyze its production systems and their individual workloads:
Plan for the Future
Capacity Requirements Planning in IMT
Some companies, however, may choose to use off-the-shelf software packages to help them implement their CRP. In information management technology (IMT), capacity requirements planning refers to an enterprise application. Essentially, the software manages the CRP process for the company. Depending on the data input by management, CRP software can create a personalized production plan that includes labor, materials, systems, and other resources.
Related terms:
Bottleneck
A bottleneck is a point of congestion in a production system that occurs when workloads arrive at a point more quickly than that point can handle them. read more
Bottom Line
The bottom line refers to a company's earnings, profit, net income, or earnings per share (EPS). Learn how companies can improve their bottom line. read more
Capacity Cost
A capacity cost is incurred in an attempt to expand operations or scale for a business or organization. read more
Capacity
Capacity is the maximum level of goods and services output that a given system can produce over a set period of time. read more
Closed Loop MRP
Closed Loop MRP (Manufacturing Resource Planning) is a computerized system used for production planning and inventory control. read more
Demand
Demand is an economic principle that describes consumer willingness to pay a price for a good or service. read more
Due Diligence & Uses for Stocks
Performing due diligence means thoroughly checking the financials of a potential financial decision. Here's how to do due diligence for individual stocks. read more
Enterprise Application Integration
Enterprise application integration is the alignment and translation of data and other commands from one application format into another. read more
Excess Capacity
Excess capacity occurs when a business produces less output than it actually could because there is not a demand for the product. read more
Information Management Technology (IMT)
Information management technology (IMT) is the distribution, organization, and control of the technology and data of a business. read more