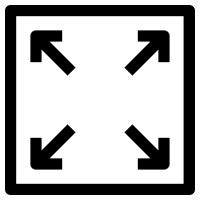
Capacity
Capacity is the maximum level of output that a company can sustain to make a product or provide a service. A capacity manager might deal with external goods or services like outgoing and incoming freight; they might manage a more technical type of capacity, like knowing the output capacity of a computer network; or they could manage employees on hand at any given time for a large customer service provider. Depending on the business type, capacity can refer to a production process, human resources allocation, technical thresholds, or several other related concepts. Depending on the business type, capacity can refer to a production process, human resources allocation, technical thresholds, or several other related concepts. Sometimes, especially at larger companies or those with a highly technical focus, dedicated capacity managers who often have specialized education and training in logistics, handle capacity management.
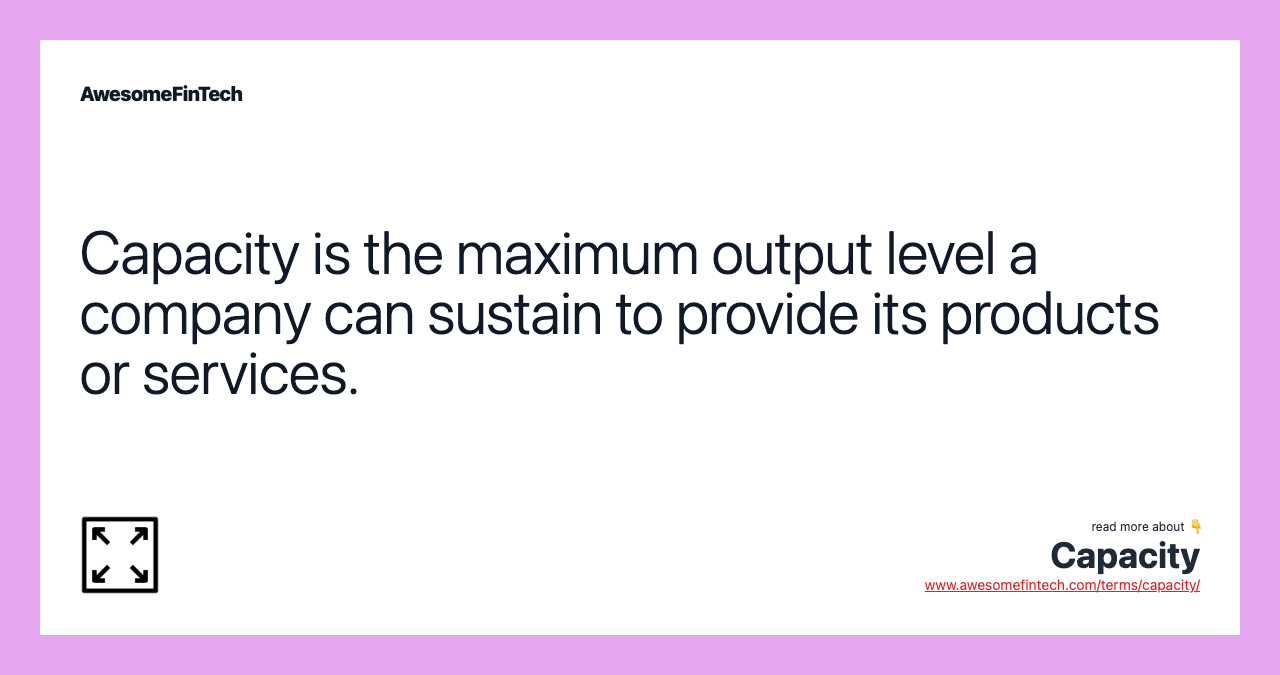
What Is Capacity?
Capacity is the maximum level of output that a company can sustain to make a product or provide a service. Planning for capacity requires management to accept limitations on the production process.
Depending on the business type, capacity can refer to a production process, human resources allocation, technical thresholds, or several other related concepts.
No system can operate at full capacity for a prolonged period; inefficiencies and delays make it impossible to reach a theoretical level of output over the long run.
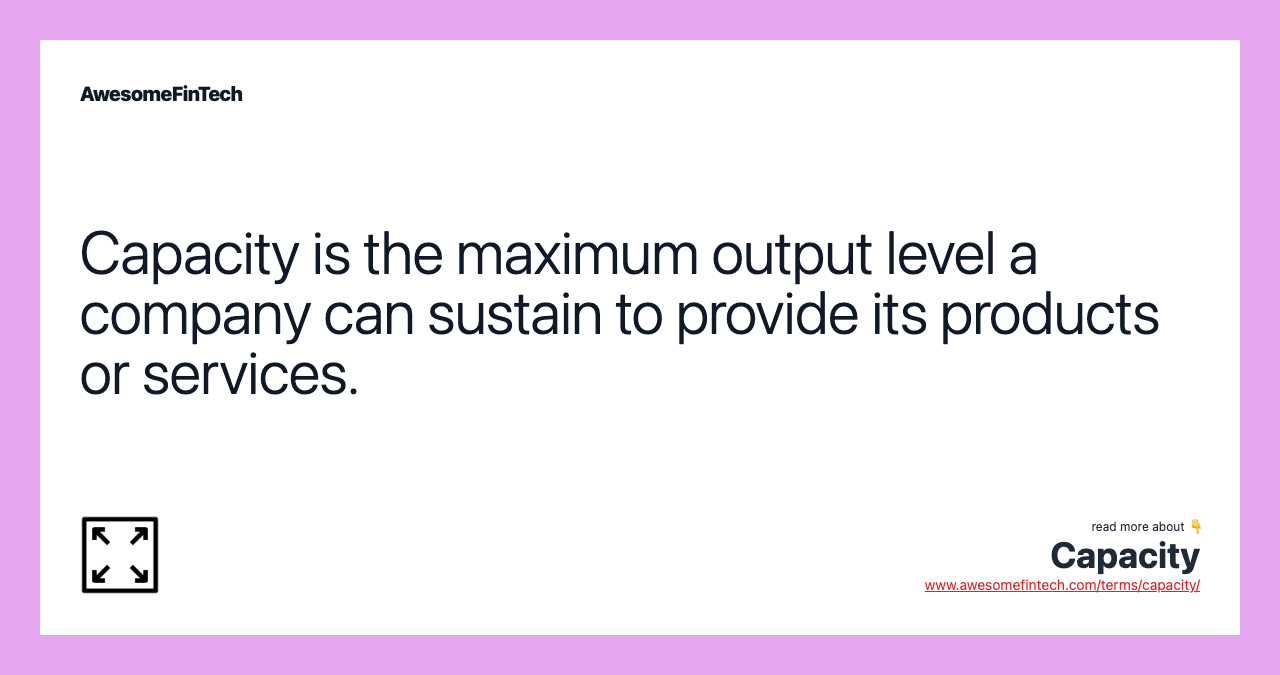
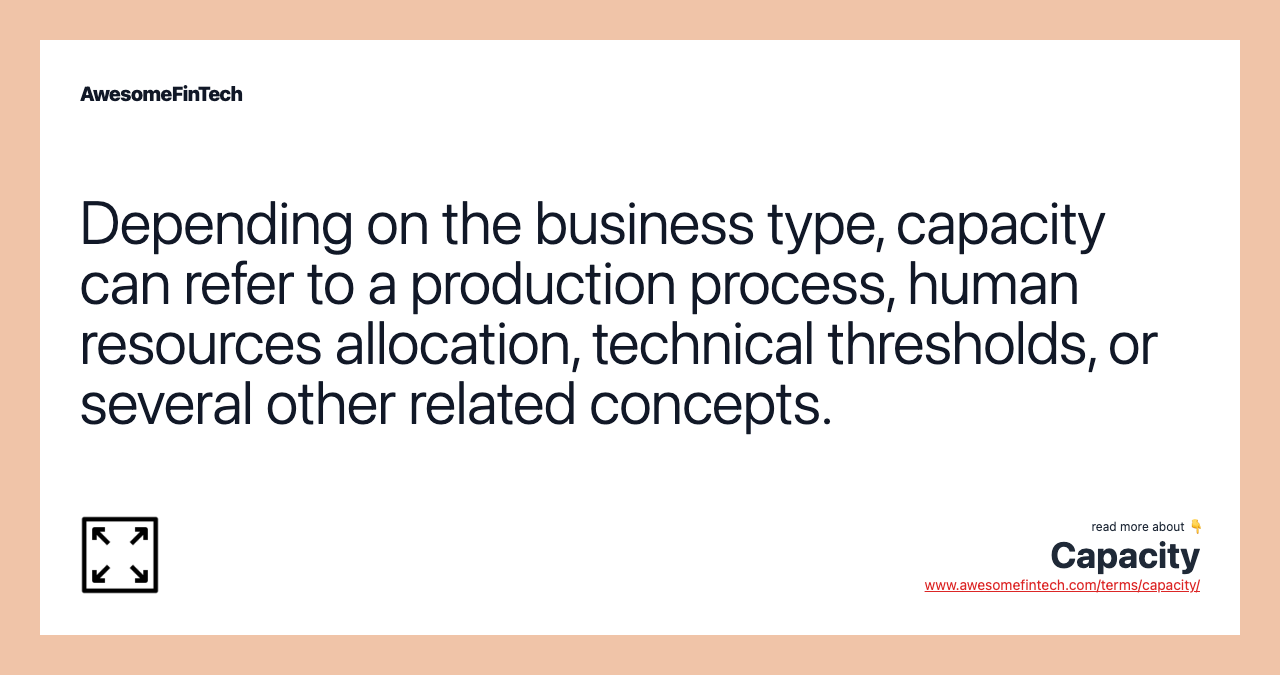
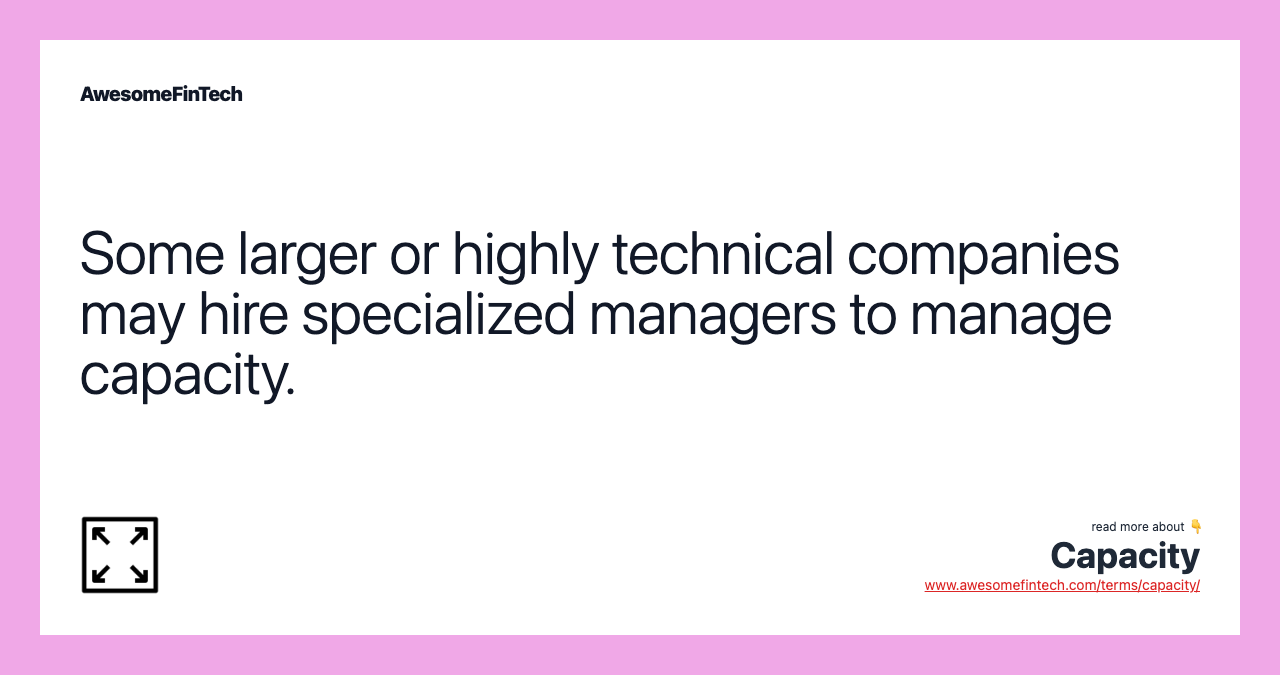
Understanding Capacity
Capacity ties into the fact that all production operates within a relevant range. No piece of machinery or equipment can operate above the relevant range for very long. Assume, for example, ABC Manufacturing makes jeans, and that a commercial sewing machine can operate effectively when used between 1,500 and 2,000 hours a month.
If the firm sees a spike in production, the machine can operate at more than 2,000 hours for a month, but the risk of a breakdown increases. Management has to plan production so that the machine can operate within a relevant range.
Capacity Level Differences
Capacity assumes a constant level of maximum output. This production level assumes no machine or equipment breakdowns and no stoppages due to employee vacations or absences. Since this level of capacity is not possible, companies should instead use practical capacity, which accounts for repair and maintenance on machines and employee scheduling.
How the Flow of Manufacturing Cost Works
Managers plan for production capacity by understanding the flow of costs through the manufacturing process. ABC, for example, purchases denim material and ships the material to the factory floor. Workers load the material into machines that cut and dye the denim. Another group of workers sews parts of the jeans by hand, and then the jeans are packaged and sent to a warehouse as inventory.
Capacity Managers
Sometimes, especially at larger companies or those with a highly technical focus, dedicated capacity managers who often have specialized education and training in logistics, handle capacity management.
A capacity manager might deal with external goods or services like outgoing and incoming freight; they might manage a more technical type of capacity, like knowing the output capacity of a computer network; or they could manage employees on hand at any given time for a large customer service provider.
Factoring in Bottlenecks
A manager can maintain a high level of capacity by avoiding bottlenecks in the production process. A bottleneck is a point of congestion that slows the process, such as a delay in getting denim materials to the factory floor or producing flawed pairs of jeans due to poor employee training.
Any event that stops production increases costs and may delay a shipment of goods to a customer. Delays may mean the loss of a customer order and possibly the loss of future business from the client. Management can avoid bottlenecks by working with reliable vendors and properly training employees.
Every business should budget for sales and production levels and then review actual results to determine whether production is operating efficiently.
Related terms:
Accounting
Accounting is the process of recording, summarizing, analyzing, and reporting financial transactions of a business to oversight agencies, regulators, and the IRS. read more
Bottleneck
A bottleneck is a point of congestion in a production system that occurs when workloads arrive at a point more quickly than that point can handle them. read more
Capacity Cost
A capacity cost is incurred in an attempt to expand operations or scale for a business or organization. read more
Closed Loop MRP
Closed Loop MRP (Manufacturing Resource Planning) is a computerized system used for production planning and inventory control. read more
Excess Capacity
Excess capacity occurs when a business produces less output than it actually could because there is not a demand for the product. read more
Factors of Production
Factors of production are the inputs needed for the creation of a good or service. The factors of production include land, labor, entrepreneurship, and capital. read more
Industrial Revolution
The Industrial Revolution was a period of major innovation that started in Great Britain and spread around the world during the 1700s and 1800s. read more
Manufacturing Production
Manufacturing production refers to methods used to manufacture and produce goods for sale. Read how efficient manufacturing production increases profits. read more
Production Costs
Production costs are incurred by a business when it manufactures a product or provides a service. These costs include a variety of expenses. read more
Throughput
Throughput is the rate at which a company can produce and sell its goods. read more