
Backflush Costing
Backflush costing is a product costing system generally used in a just-in-time (JIT) inventory system. Backflush costing can be difficult to do and not every company meets the criteria to conduct backflush costing. “Flushing” costs to the end of the production run eliminates the detailed tracking of expenses, such as raw material and labor costs, throughout the manufacturing process, which is a feature of traditional costing systems. Moreover, there are some other big caveats: businesses that do backflush costing lack a sequential audit trail and may not always conform to generally accepted accounting principles (GAAP). Companies using backflush costing generally meet the following three conditions: **Short production cycles:** Backflush costing shouldn’t be used for goods that take a long time to manufacture. Sometimes costs differ, so companies eventually need to recognize the variances in standard costs and actual costs. Usually, the costs of products are calculated during various stages of the production cycle. This allows the company to simplify its expense tracking processes, thus saving accounting and process costs, but it may also limit the detail of information that the company retains related to individual costs for production and sales.
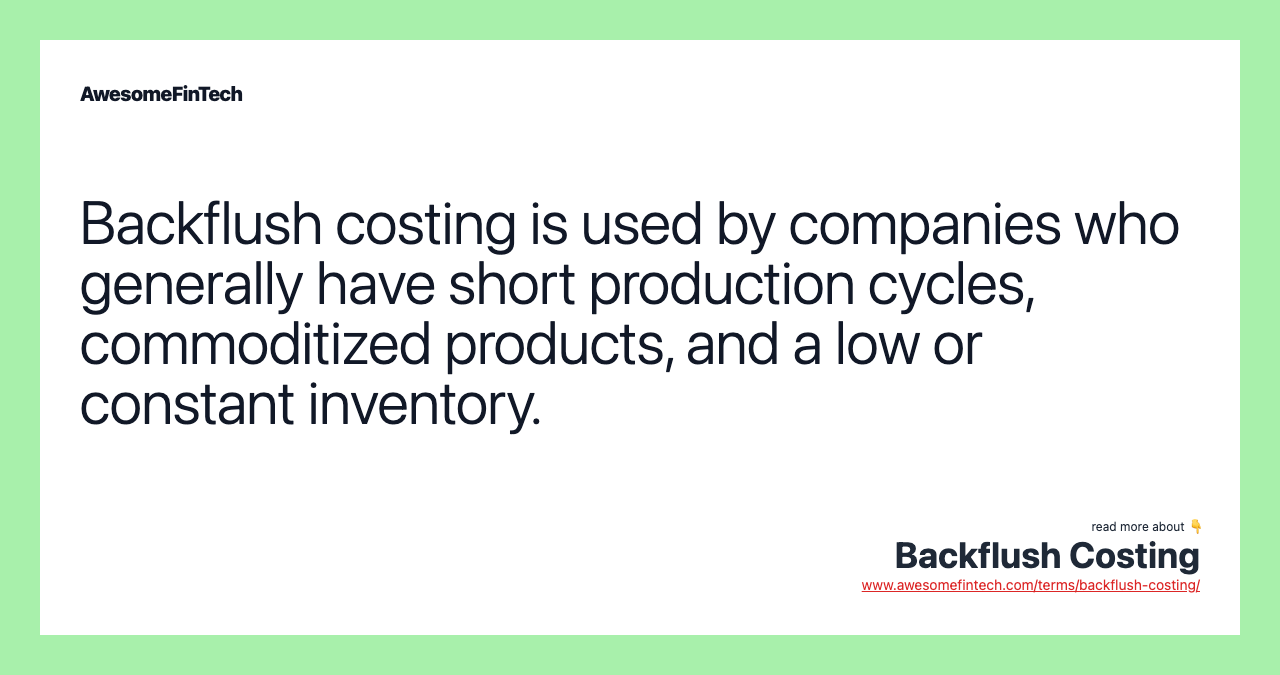
What Is Backflush Costing?
Backflush costing is a product costing system generally used in a just-in-time (JIT) inventory system. In short, it is an accounting method that records the costs associated with producing a good or service only after they are produced, completed, or sold. Backflush costing is also commonly referred to as backflush accounting.
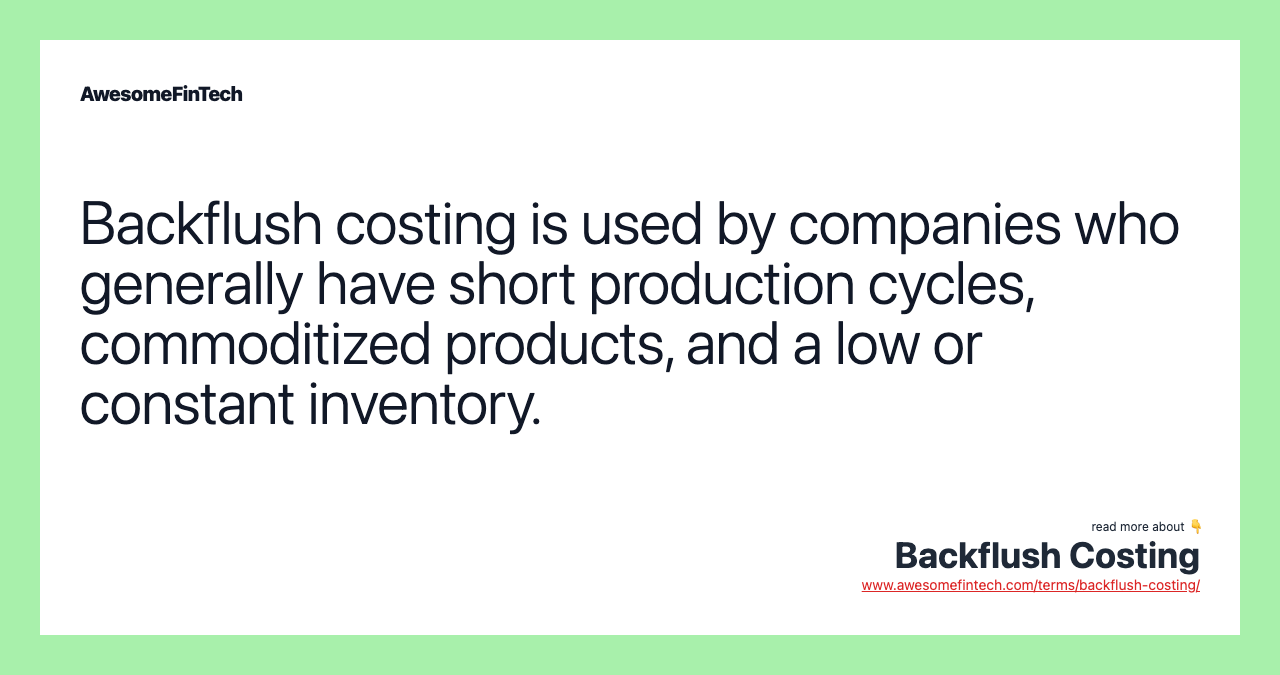
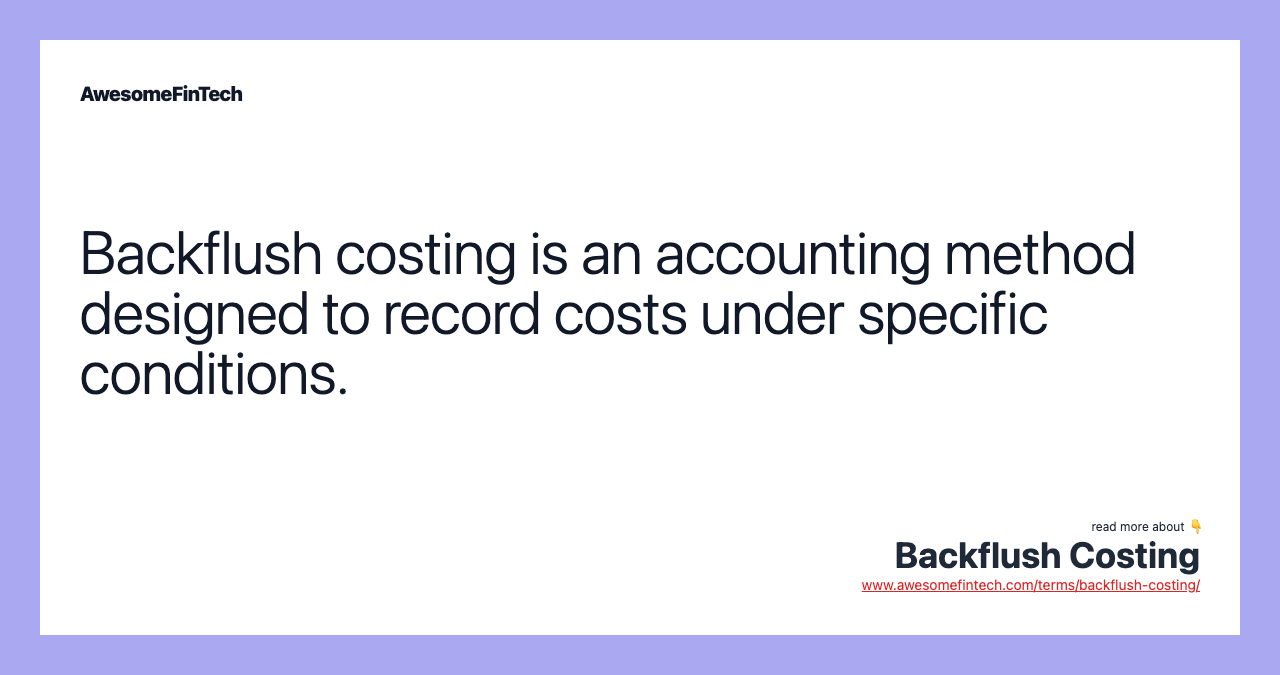
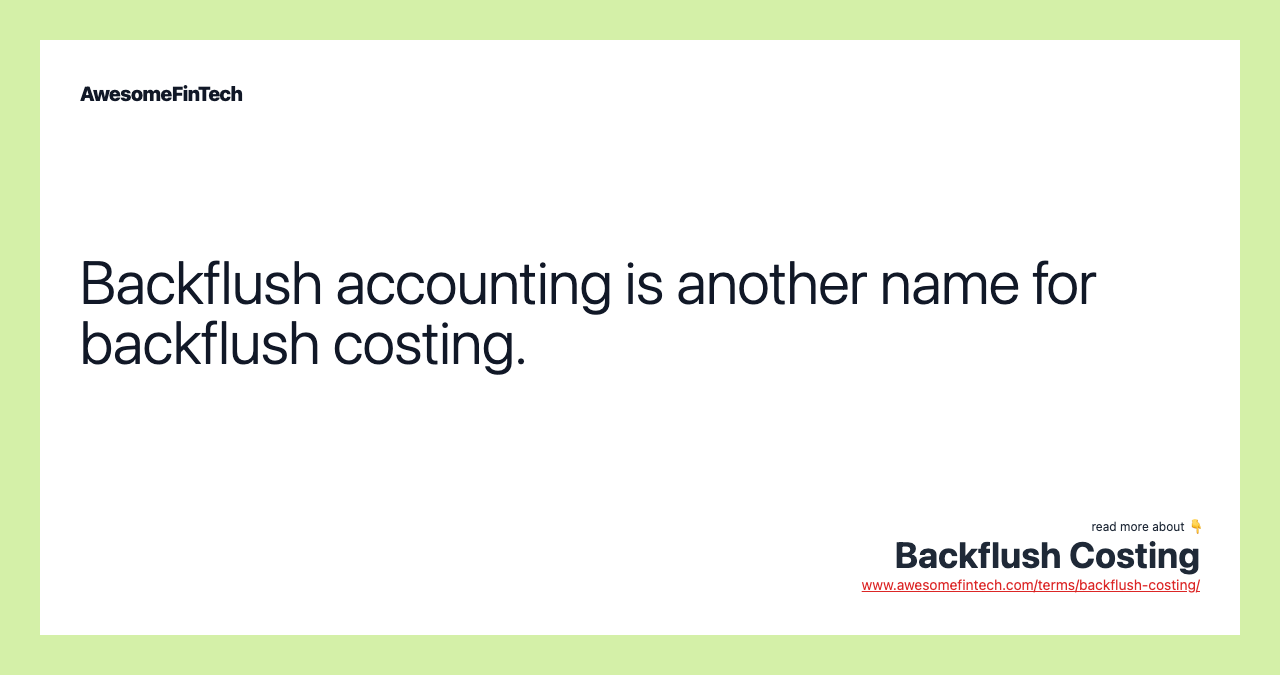
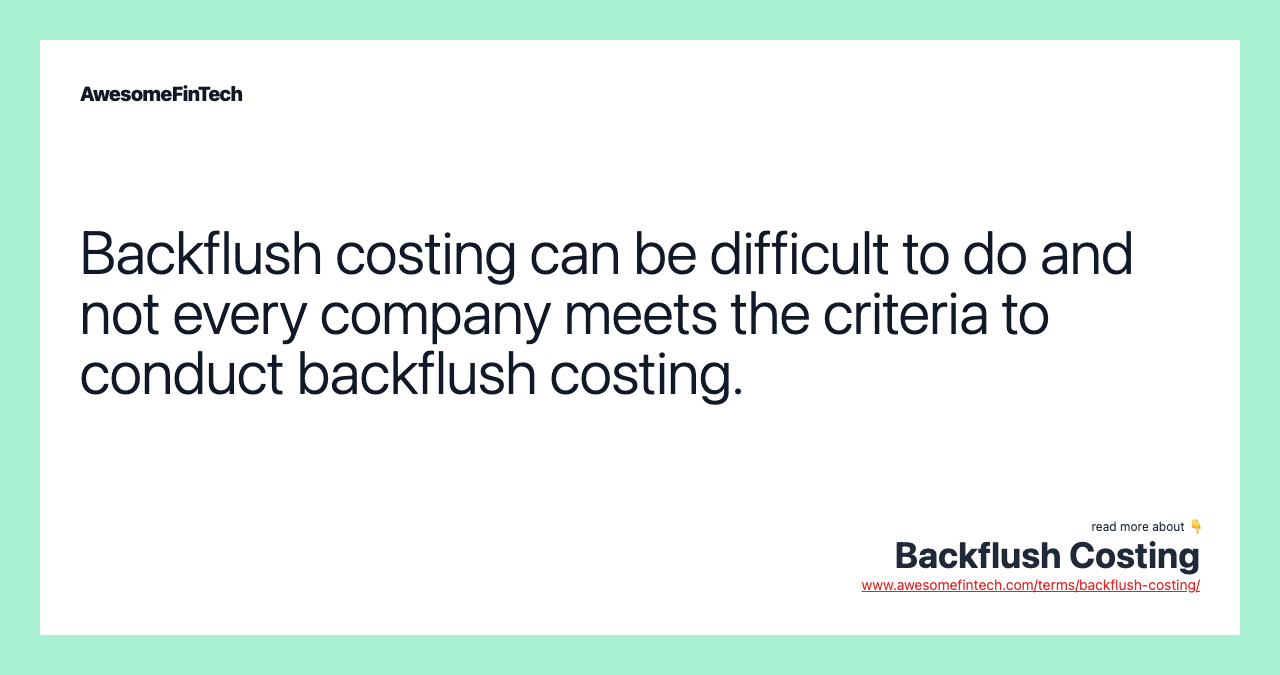
How Backflush Costing Works
“Flushing” costs to the end of the production run eliminates the detailed tracking of expenses, such as raw material and labor costs, throughout the manufacturing process, which is a feature of traditional costing systems. This allows the company to simplify its expense tracking processes, thus saving accounting and process costs, but it may also limit the detail of information that the company retains related to individual costs for production and sales.
The total costs of a production run are recorded all at once, at the end of the process. Companies using backflush costing, therefore, primarily work backward, calculating the costs of products after they're sold, finished, or shipped. To do this, businesses assign standard charges to the goods they produce. Sometimes costs differ, so companies eventually need to recognize the variances in standard costs and actual costs.
Usually, the costs of products are calculated during various stages of the production cycle. By eliminating work-in-process (WIP) accounts, backflush costing is designed to simplify the accounting process and save businesses money.
Advantages and Disadvantages of Backflush Costing
In theory, backflushing appears to be a sensible way to avoid the many complexities associated with assigning costs to products and inventory. Not logging costs during the various production stages enable companies to save time and reduce their expenses. Companies looking for ways to reduce their bottom lines may use backflush costing, but it isn't always an easy accounting method to implement.
The process of backflush costing makes it difficult for companies to audit because it doesn't always adhere to the basic fundamentals of accounting.
However, backflushing can also be challenging to implement and is not an option available to all companies. Moreover, there are some other big caveats: businesses that do backflush costing lack a sequential audit trail and may not always conform to generally accepted accounting principles (GAAP).
Special Considerations
Companies using backflush costing generally meet the following three conditions:
Related terms:
Cost Accounting
Cost accounting is a form of managerial accounting that aims to capture a company's total cost of production by assessing its variable and fixed costs. read more
Full Costing
Full costing is a managerial accounting method that describes when all fixed and variable costs are used to compute the total cost per unit. read more
Inventory Management
Inventory management is the process of ordering, storing and using a company's inventory: raw materials, components, and finished products. read more
Inventory Accounting
Inventory accounting is the body of accounting that deals with valuing and accounting for changes in inventoried assets. read more
Just in Time (JIT) Inventory
A just-in-time (JIT) inventory system is a management strategy that aligns raw-material orders from suppliers directly with production schedules. read more
Raw Materials
Raw materials are commodities companies use in the primary production or manufacturing of goods. read more
Work-in-Progress (WIP) & Example
A work-in-progress (WIP) is a partially finished good awaiting completion and includes such costs as overhead, labor, and raw materials. read more