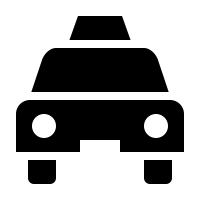
Activity Cost Driver
An activity cost driver is an accounting term. Therefore, every machine hour results in a 50 cent (500 / 1,000) maintenance cost allocated to the product being manufactured based on the cost driver of machine-hours. If a business owner can identify the cost drivers, the business owner can more accurately estimate the true cost of production for the business. More technical cost drivers are machine hours, the number of engineering change orders, the number of customer contacts, the number of product returns, the machine setups required for production, or the number of inspections. In activity-based costing (ABC), an activity cost driver influences the costs of labor, maintenance, or other variable costs.
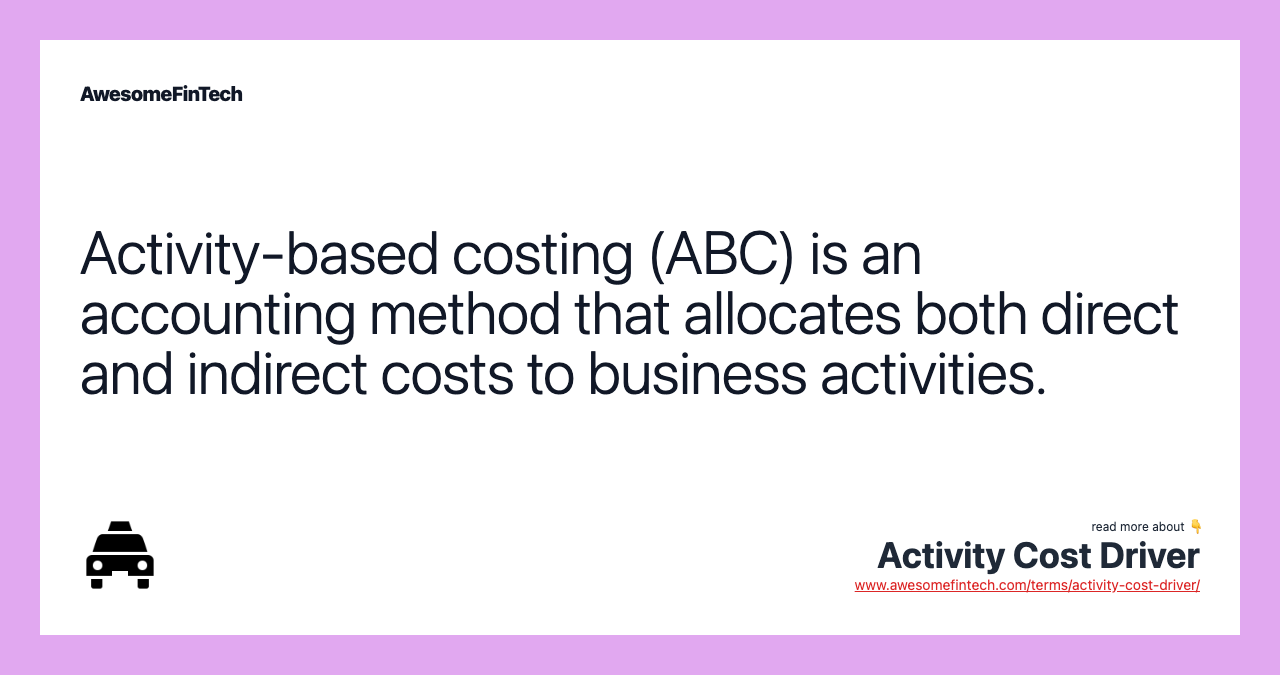
What Is an Activity Cost Driver?
An activity cost driver is an accounting term. A cost driver affects the cost of specific business activities. In activity-based costing (ABC), an activity cost driver influences the costs of labor, maintenance, or other variable costs. Cost drivers are essential in ABC, a branch of managerial accounting that allocates the indirect costs, or overheads, of an activity.
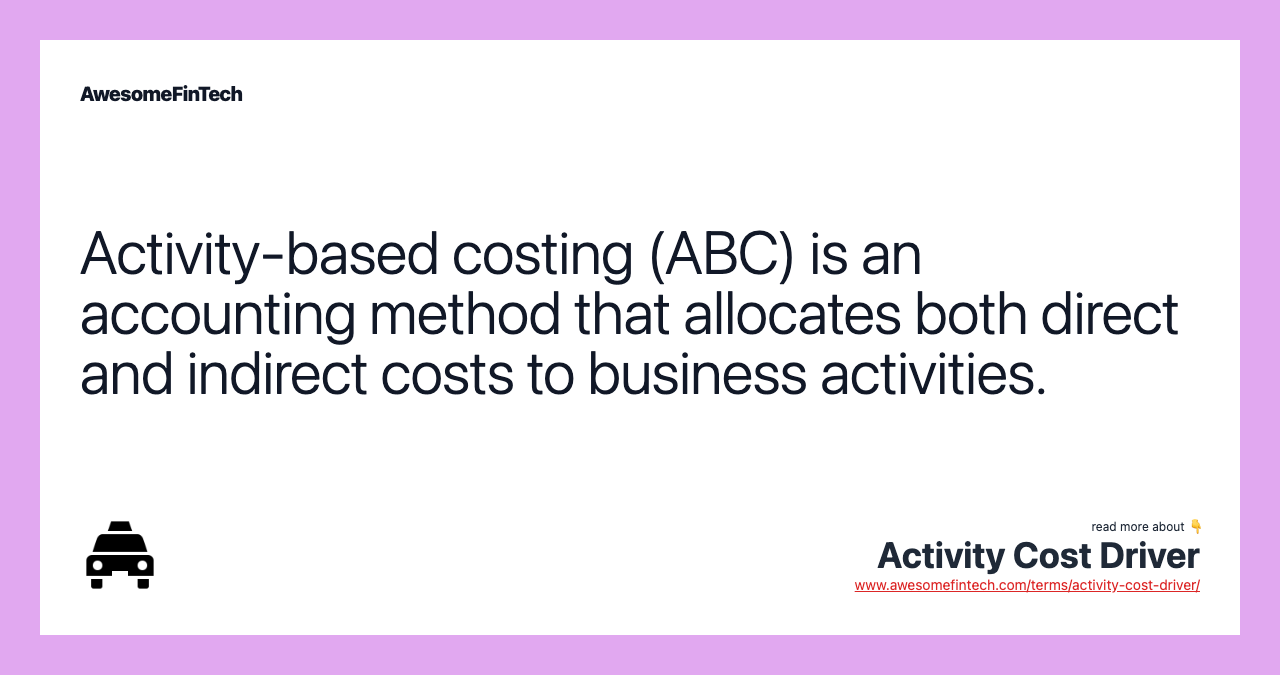
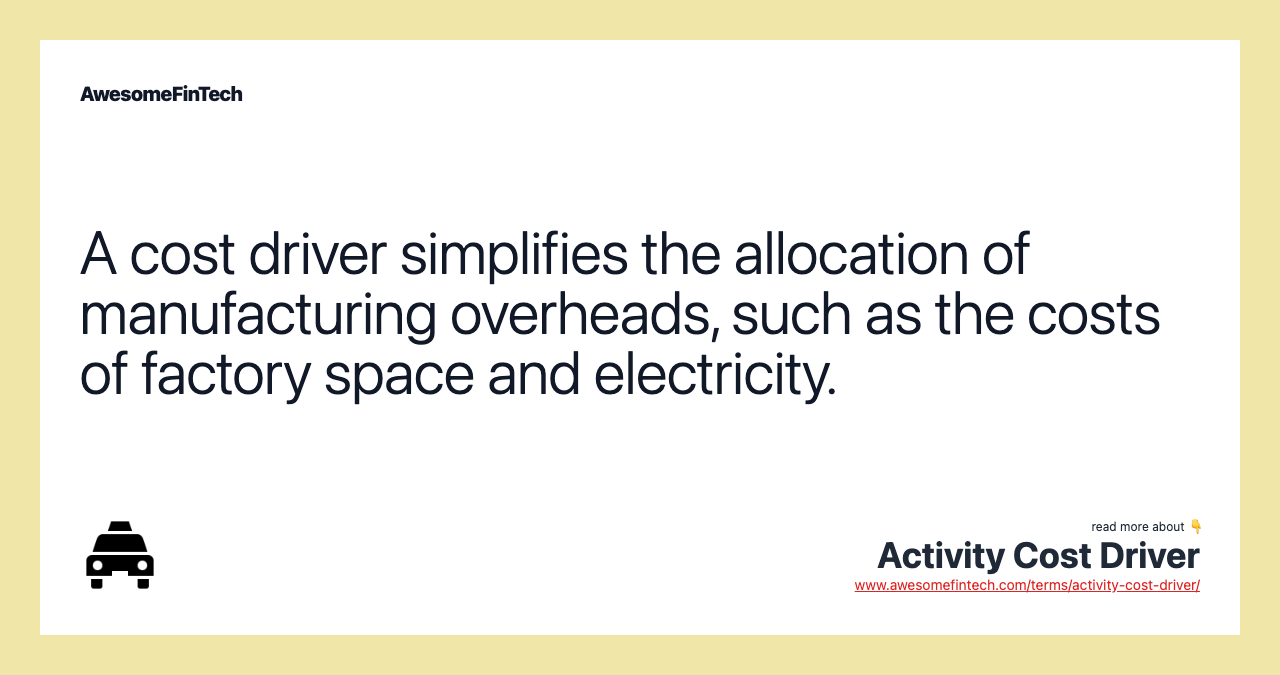
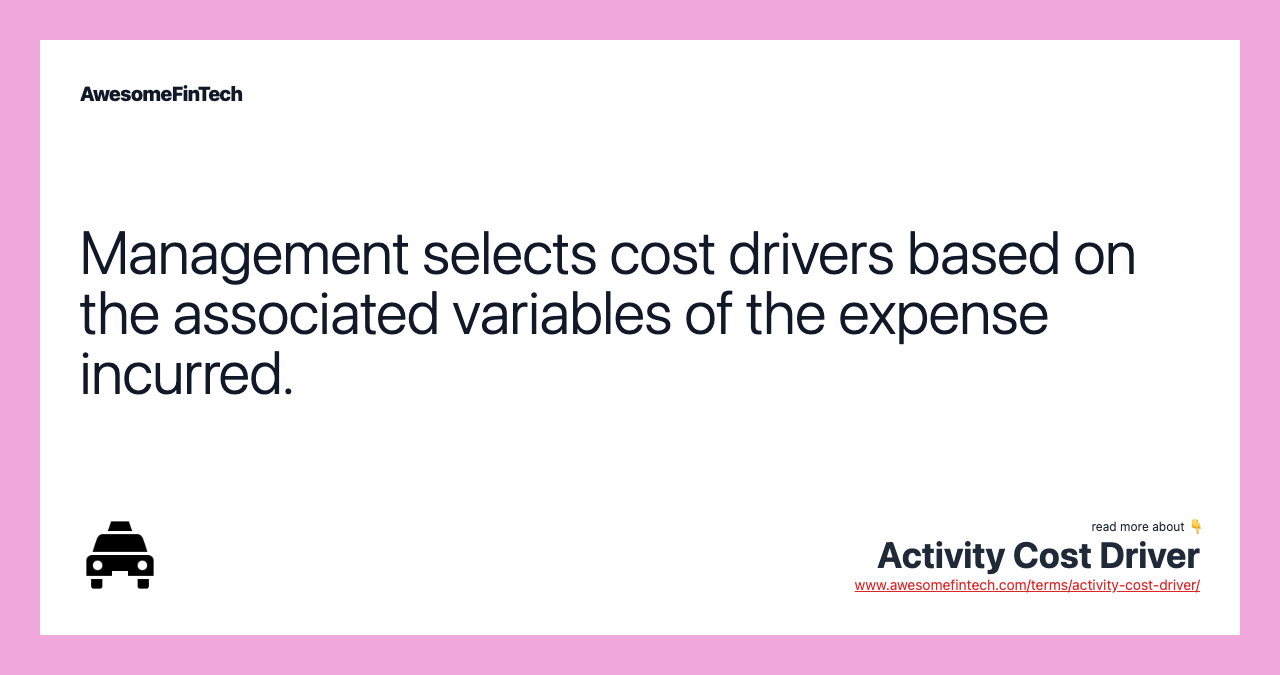
How Activity Cost Drivers Work
A cost driver directly influences a business activity. There may be multiple cost drivers associated with an activity. For example, direct labor hours are a driver of most activities in product manufacturing. If the cost of labor is high, this will increase the cost of producing all company products or services. If the cost of warehousing is high, this will also increase the expenses incurred for product manufacturing or providing services.
An activity cost driver, also known as a causal factor, causes the cost of an activity to increase or decrease. An example is a change in the cost of warehousing or a change in the level of production.
More technical cost drivers are machine hours, the number of engineering change orders, the number of customer contacts, the number of product returns, the machine setups required for production, or the number of inspections. If a business owner can identify the cost drivers, the business owner can more accurately estimate the true cost of production for the business.
Cost Allocation
When a factory machine requires periodic maintenance, the cost of the maintenance is allocated to the products produced by the machine. For example, the cost driver selected is machinery hours. After every 1,000 machine-hours, there is a maintenance expense of $500. Therefore, every machine hour results in a 50 cent (500 / 1,000) maintenance cost allocated to the product being manufactured based on the cost driver of machine-hours.
Distribution of Overhead Costs
A cost driver simplifies the allocation of manufacturing overhead. The correct allocation of manufacturing overhead is important to determine the true cost of a product. Internal management uses the cost of a product to determine the prices of the products they produce. For this reason, the selection of accurate cost drivers has a direct impact on the profitability and operations of an entity.
Fast Fact
Activity-based costing (ABC) is a more accurate way of allocating both direct and indirect costs. ABC calculates the true cost of each product by identifying the amount of resources consumed by a business activity, such as electricity or man hours.
Special Considerations: The Subjectivity of Cost Drivers
Management selects cost drivers as the basis for manufacturing overhead allocation. There are no industry standards stipulating or mandating cost driver selection. Company management selects cost drivers based on the variables of the expenses incurred during production.
Related terms:
Activity-Based Costing (ABC) & Method
Activity-based costing (ABC) is a system that tallies the costs of overhead activities and assigns those costs to products. read more
Absorbed
Absorbed as a business term generally refers to taking in, acquiring or bearing. The term can be applied in a number of situations. read more
Activity Cost Pool
An activity cost pool is an aggregate of all the costs associated with performing a particular business task, such as making a particular product. read more
Applied Overhead
Applied overhead is a fixed charge assigned to a specific production job or department within a business. read more
Departmental Overhead Rate
The departmental overhead rate is defined as an expense rate for every department in a factory production process. read more